Press forming is a versatile manufacturing process used to shape various materials into desired forms by applying mechanical pressure. The materials used in press forming are diverse and depend on the specific application, ranging from metals and ceramics to composites and polymers. Below is a detailed explanation of the materials commonly used in press forming, their properties, and their applications.
Key Points Explained:
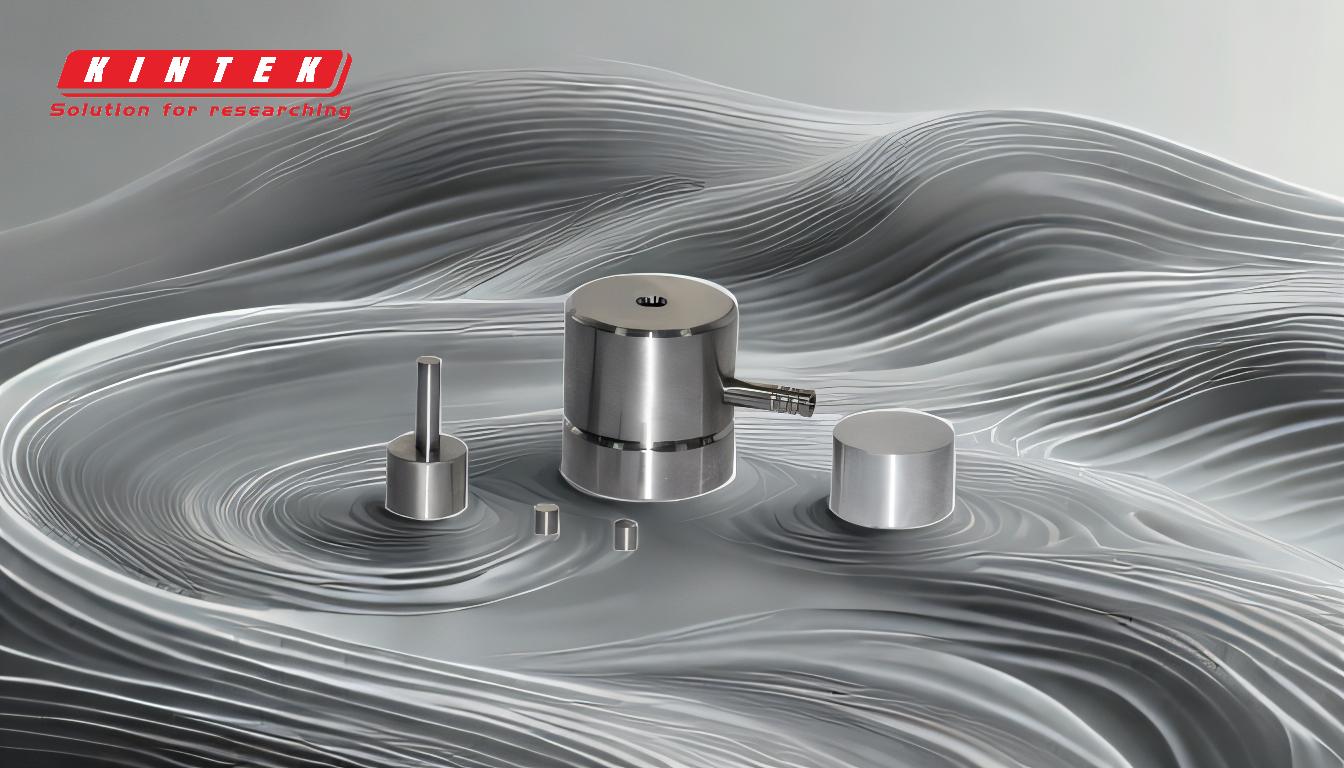
-
Metals and Alloys:
- Metals are the most commonly used materials in press forming due to their ductility, strength, and ability to withstand high pressures. Common metals include:
- Steel: Widely used in automotive and construction industries for its strength and durability.
- Aluminum: Preferred for lightweight applications such as aerospace and packaging due to its high strength-to-weight ratio.
- Copper and Brass: Used in electrical components and decorative applications because of their conductivity and aesthetic appeal.
- Titanium: Utilized in aerospace and medical industries for its high strength, corrosion resistance, and biocompatibility.
- Metals are the most commonly used materials in press forming due to their ductility, strength, and ability to withstand high pressures. Common metals include:
-
Ceramics:
- Ceramics are used in press forming for applications requiring high-temperature resistance, hardness, and electrical insulation. Examples include:
- Alumina (Al2O3): Commonly used in electrical insulators, cutting tools, and wear-resistant components.
- Zirconia (ZrO2): Known for its high fracture toughness, it is used in dental implants, cutting tools, and thermal barrier coatings.
- Ultra-High Temperature Ceramics (UHTCs): Materials like zirconium diboride (ZrB2), hafnium diboride (HfB2), and titanium nitride (TiN) are used in extreme environments such as aerospace and defense for their exceptional thermal and chemical stability.
- Ceramics are used in press forming for applications requiring high-temperature resistance, hardness, and electrical insulation. Examples include:
-
Refractory Metals and Alloys:
- These materials are used in high-temperature and high-stress environments. Examples include:
- Tungsten (W): Used in lighting, electronics, and aerospace due to its high melting point and density.
- Molybdenum (Mo): Employed in furnace components and aerospace applications for its thermal conductivity and strength.
- Tantalum (Ta): Used in chemical processing and medical implants for its corrosion resistance and biocompatibility.
- Rhenium (Re): Often alloyed with other metals to improve high-temperature performance in jet engines and turbines.
- These materials are used in high-temperature and high-stress environments. Examples include:
-
Polymers and Composites:
- Polymers and composites are increasingly used in press forming for lightweight and corrosion-resistant applications. Examples include:
- Thermoplastics: Materials like polyethylene (PE) and polypropylene (PP) are used in packaging, automotive parts, and consumer goods.
- Thermosetting Polymers: Epoxy and phenolic resins are used in electrical insulation and structural components.
- Fiber-Reinforced Composites: Combining polymers with fibers like carbon or glass enhances strength and stiffness, making them ideal for aerospace and automotive industries.
- Polymers and composites are increasingly used in press forming for lightweight and corrosion-resistant applications. Examples include:
-
Specialized Materials:
- Some advanced materials are tailored for specific applications in press forming:
- Shape Memory Alloys: Used in medical devices and actuators for their ability to return to a pre-defined shape when heated.
- Metal Matrix Composites: Combining metals with ceramic reinforcements enhances strength and wear resistance for high-performance applications.
- Some advanced materials are tailored for specific applications in press forming:
In summary, press forming utilizes a wide range of materials, each selected based on the desired properties and application requirements. Metals and alloys dominate due to their versatility, while ceramics and refractory materials are chosen for extreme environments. Polymers and composites offer lightweight and corrosion-resistant alternatives, and specialized materials cater to niche applications. Understanding the properties and applications of these materials is crucial for optimizing the press forming process and achieving high-quality end products.
Summary Table:
Material Category | Examples | Key Properties | Applications |
---|---|---|---|
Metals and Alloys | Steel, Aluminum, Copper, Brass, Titanium | Ductility, strength, high-pressure resistance | Automotive, aerospace, construction, electrical, medical |
Ceramics | Alumina (Al2O3), Zirconia (ZrO2), Ultra-High Temperature Ceramics (UHTCs) | High-temperature resistance, hardness, electrical insulation | Electrical insulators, cutting tools, dental implants, aerospace, defense |
Refractory Metals | Tungsten (W), Molybdenum (Mo), Tantalum (Ta), Rhenium (Re) | High melting point, thermal conductivity, corrosion resistance | Lighting, electronics, aerospace, chemical processing, medical implants |
Polymers and Composites | Thermoplastics (PE, PP), Thermosetting Polymers, Fiber-Reinforced Composites | Lightweight, corrosion-resistant, enhanced strength and stiffness | Packaging, automotive, consumer goods, electrical insulation, aerospace |
Specialized Materials | Shape Memory Alloys, Metal Matrix Composites | Shape memory effect, high strength, wear resistance | Medical devices, actuators, high-performance applications |
Need help selecting the right materials for your press forming project? Contact our experts today for tailored solutions!