Induction heating is a process that primarily works with conductive materials, especially metals, due to their ability to generate heat through electromagnetic induction. Non-conductive materials, such as plastics, can only be heated indirectly by first heating a conductive metal inductor and then transferring the heat. Induction heating is widely used for melting and processing a variety of metals, including precious metals like gold, silver, and platinum, as well as non-ferrous metals like copper, aluminum, and their alloys. It is also effective for melting ferrous metals such as steel and iron. The versatility of induction heating makes it a valuable technology in industries ranging from metallurgy to manufacturing.
Key Points Explained:
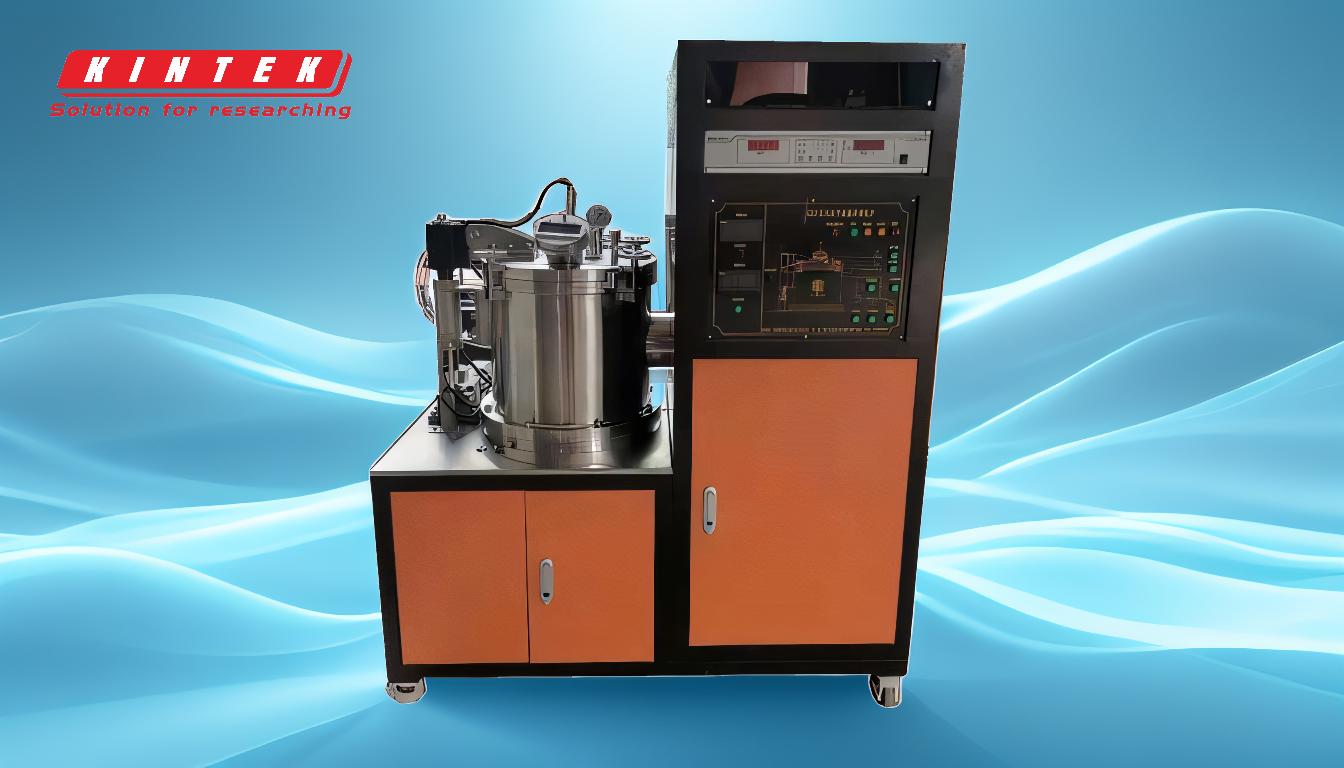
-
Conductive Materials (Metals) for Direct Induction Heating:
- Induction heating works directly on materials that are electrically conductive, primarily metals. This is because the process relies on the generation of eddy currents within the material, which produce heat due to electrical resistance.
- Examples of metals that can be directly heated include:
- Precious metals: gold, silver, platinum, palladium, and rhodium.
- Non-ferrous metals: copper, aluminum, brass, and bronze.
- Ferrous metals: steel, iron, and their alloys.
-
Non-Conductive Materials (Indirect Heating):
- Non-conductive materials, such as plastics, cannot be directly heated using induction heating because they do not conduct electricity and therefore cannot generate eddy currents.
- To heat non-conductive materials, a conductive metal inductor is first heated using induction, and the heat is then transferred to the non-conductive material through conduction or radiation.
-
Applications in Metal Melting:
- Induction heating is extensively used in metal melting processes. Induction furnaces are capable of melting a wide range of metals, including:
- Precious metals: gold, silver, platinum, and palladium.
- Non-ferrous metals: copper, aluminum, and their alloys (e.g., brass, bronze).
- Ferrous metals: steel, iron, and ferroalloys.
- This technology is particularly useful in industries such as jewelry making, metallurgy, and manufacturing, where precise temperature control and efficient heating are required.
- Induction heating is extensively used in metal melting processes. Induction furnaces are capable of melting a wide range of metals, including:
-
Versatility of Induction Heating:
- Induction heating is versatile and can be applied to various metals, making it suitable for different industrial applications. It is used for:
- Melting and casting metals.
- Heat treatment processes like hardening, annealing, and tempering.
- Joining processes such as brazing and soldering.
- The ability to heat metals quickly and efficiently without direct contact makes induction heating a preferred method in many industries.
- Induction heating is versatile and can be applied to various metals, making it suitable for different industrial applications. It is used for:
-
Advantages of Induction Heating:
- Efficiency: Induction heating is highly efficient as it directly heats the material, minimizing energy loss.
- Precision: It allows for precise control over the heating process, which is crucial for applications like metal melting and heat treatment.
- Cleanliness: Since there is no direct flame or combustion, induction heating is a clean process that reduces contamination.
- Speed: The heating process is fast, which is beneficial for high-volume production environments.
-
Limitations of Induction Heating:
- Material Restrictions: Induction heating is limited to conductive materials, primarily metals. Non-conductive materials require indirect heating methods.
- Cost: The initial setup cost for induction heating equipment can be high, although it is often offset by the long-term efficiency and savings.
- Complexity: The process requires specialized equipment and knowledge, which may not be readily available in all settings.
In summary, induction heating is a powerful and versatile technology that is primarily used with conductive materials, especially metals. It is widely applied in metal melting, heat treatment, and joining processes across various industries. While it has some limitations, its advantages in terms of efficiency, precision, and cleanliness make it a valuable tool in modern manufacturing and metallurgy.
Summary Table:
Aspect | Details |
---|---|
Conductive Materials | Metals (gold, silver, copper, aluminum, steel, iron, alloys) |
Non-Conductive Materials | Plastics (require indirect heating via conductive metal inductor) |
Applications | Metal melting, heat treatment, brazing, soldering |
Advantages | High efficiency, precise control, clean process, fast heating |
Limitations | Limited to conductive materials, high initial cost, requires expertise |
Discover how induction heating can revolutionize your metal processing—contact us today for expert guidance!