Brazing is a metal-joining process that uses a filler metal with a melting point above 840°F (450°C) but below the melting point of the base metals being joined. The choice of filler metal depends on the base metals, the application, and the required properties of the joint. Common filler metals used in brazing include aluminum-silicon alloys, copper, copper-phosphorus alloys, silver-based alloys, and nickel-based alloys. Each filler metal has specific characteristics that make it suitable for particular applications, such as high-temperature resistance, corrosion resistance, or electrical conductivity.
Key Points Explained:
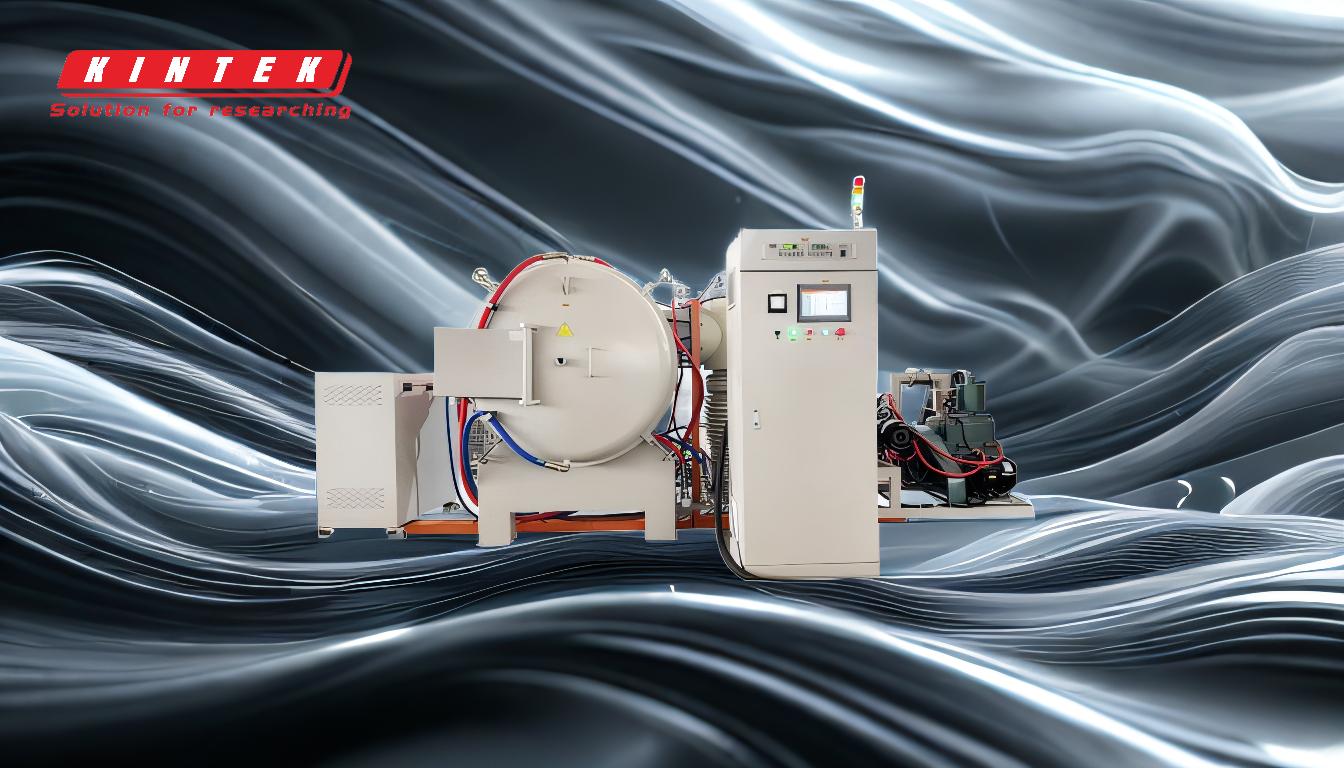
-
Aluminum-Silicon Alloys:
- Composition: Typically contain 7-12% silicon, with small amounts of other elements like copper or magnesium.
- Applications: Used for brazing aluminum and its alloys. These filler metals are ideal for applications requiring good corrosion resistance and strength.
- Properties: They have a relatively low melting point, making them suitable for joining aluminum without melting the base metal.
-
Copper and Copper-Phosphorus Alloys:
- Composition: Pure copper or copper with 5-7% phosphorus, sometimes with added silver.
- Applications: Commonly used for brazing copper and brass. Copper-phosphorus alloys are particularly useful in plumbing and refrigeration systems.
- Properties: These alloys provide excellent flow and wetting characteristics, and the phosphorus acts as a flux, reducing the need for additional flux in some applications.
-
Silver-Based Alloys:
- Composition: Typically contain 20-70% silver, with varying amounts of copper, zinc, and cadmium (though cadmium is being phased out due to health concerns).
- Applications: Widely used in HVAC, electrical, and plumbing industries. Silver-based alloys are versatile and can be used to join a variety of metals, including stainless steel, copper, and nickel alloys.
- Properties: They offer good strength, ductility, and corrosion resistance. The addition of silver improves the flow and wetting properties of the filler metal.
-
Nickel-Based Alloys:
- Composition: Contain nickel as the primary element, with additions of chromium, boron, and silicon.
- Applications: Used for high-temperature applications, such as in aerospace, power generation, and chemical processing industries. These alloys are suitable for brazing stainless steel, nickel alloys, and other high-temperature materials.
- Properties: Nickel-based alloys provide excellent strength and oxidation resistance at elevated temperatures. They are also resistant to corrosion and wear.
-
Gold-Based Alloys:
- Composition: Typically contain gold with additions of copper, nickel, or palladium.
- Applications: Used in specialized applications such as electronics, jewelry, and medical devices. Gold-based alloys are often chosen for their excellent corrosion resistance and biocompatibility.
- Properties: These alloys provide high strength and excellent resistance to oxidation and corrosion, making them suitable for critical applications.
-
Other Filler Metals:
- Magnesium-Based Alloys: Used for brazing magnesium and its alloys. These filler metals are lightweight and provide good strength and corrosion resistance.
- Titanium-Based Alloys: Used for brazing titanium and its alloys. These filler metals are suitable for high-strength, lightweight applications, such as in the aerospace industry.
-
Considerations for Selecting Filler Metals:
- Base Metal Compatibility: The filler metal must be compatible with the base metals being joined. This includes matching the thermal expansion coefficients and ensuring good wetting and bonding.
- Service Conditions: The filler metal must withstand the environmental conditions, such as temperature, corrosion, and mechanical stress, that the joint will be exposed to.
- Joint Design: The design of the joint, including the gap size and the method of heating, will influence the choice of filler metal. Some filler metals flow better in tight gaps, while others are better suited for larger gaps.
- Regulatory and Safety Considerations: Some filler metals, such as those containing cadmium, may have health and environmental regulations that limit their use. It is important to choose filler metals that comply with relevant regulations.
In summary, the choice of filler metal for brazing depends on the specific requirements of the application, including the base metals, the service conditions, and the desired properties of the joint. By carefully selecting the appropriate filler metal, it is possible to create strong, durable, and reliable brazed joints.
Summary Table:
Filler Metal | Composition | Applications | Key Properties |
---|---|---|---|
Aluminum-Silicon | 7-12% silicon, small amounts of Cu/Mg | Brazing aluminum and alloys | Low melting point, corrosion resistance |
Copper/Copper-Phosphorus | Pure copper or 5-7% phosphorus | Plumbing, refrigeration systems | Excellent flow, self-fluxing |
Silver-Based | 20-70% silver, Cu, Zn, Cd (phased out) | HVAC, electrical, plumbing | Good strength, ductility, corrosion resistance |
Nickel-Based | Nickel, Cr, B, Si | Aerospace, power generation | High-temperature strength, oxidation resistance |
Gold-Based | Gold, Cu, Ni, Pd | Electronics, jewelry, medical devices | Corrosion resistance, biocompatibility |
Magnesium-Based | Magnesium alloys | Brazing magnesium alloys | Lightweight, corrosion resistance |
Titanium-Based | Titanium alloys | Aerospace, high-strength applications | High strength, lightweight |
Need help selecting the right filler metal for your brazing project? Contact our experts today!