Heat treatment is a critical process in metallurgy and manufacturing, requiring careful attention to safety and quality control. Improper handling or oversight during heat treatment can lead to defective products, financial losses, equipment damage, and even workplace injuries. To ensure a safe and effective process, several precautions must be observed, including proper atmosphere control, equipment maintenance, employee training, and adherence to safety protocols. By following these guidelines, manufacturers can minimize risks, improve product quality, and create a safer working environment.
Key Points Explained:
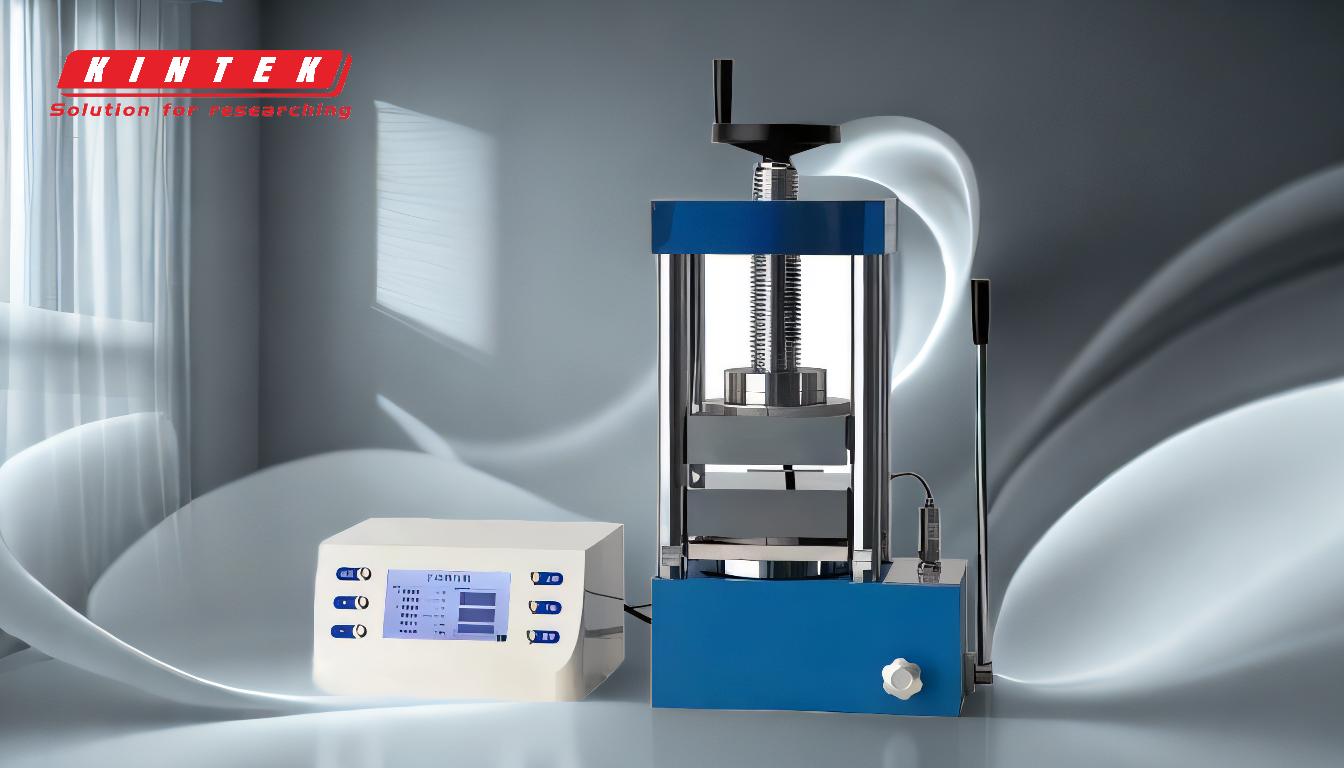
-
Control of the Heat Treatment Atmosphere
- The atmosphere within the furnace must be carefully monitored and controlled to prevent undesirable chemical reactions on the metal surface.
- Improper atmospheres can lead to oxidation, decarburization, or other surface defects, compromising the material's strength and durability.
- Use of inert gases (e.g., nitrogen or argon) or controlled atmospheres (e.g., hydrogen or carbon-based gases) is essential to maintain the desired metallurgical properties.
- Regular calibration of atmosphere control systems and sensors is necessary to ensure accuracy and consistency.
-
Temperature Regulation and Monitoring
- Precise temperature control is critical to achieving the desired material properties (e.g., hardness, toughness, or ductility).
- Overheating or underheating can result in incomplete transformations, warping, or cracking of the metal.
- Use calibrated thermocouples and temperature controllers to maintain uniform heating throughout the furnace.
- Implement a robust temperature monitoring system with alarms to detect deviations and prevent overheating.
-
Proper Handling of Materials
- Ensure that materials are clean and free from contaminants (e.g., oil, grease, or dirt) before heat treatment, as these can cause uneven heating or surface defects.
- Use appropriate fixtures or racks to support parts during treatment, preventing distortion or damage due to improper loading.
- Avoid overloading the furnace, as this can lead to uneven heat distribution and inconsistent results.
-
Equipment Maintenance and Inspection
- Regularly inspect and maintain heat treatment equipment, including furnaces, quenching systems, and cooling units, to prevent malfunctions.
- Check for wear and tear on heating elements, insulation, and seals, as these can affect temperature uniformity and energy efficiency.
- Schedule preventive maintenance to address potential issues before they escalate into costly breakdowns or safety hazards.
-
Employee Training and Safety Protocols
- Train employees on proper heat treatment procedures, including the use of personal protective equipment (PPE) such as heat-resistant gloves, face shields, and aprons.
- Emphasize the importance of following safety protocols, such as avoiding direct contact with hot materials and using proper lifting techniques.
- Conduct regular safety drills and refresher courses to reinforce best practices and emergency response procedures.
-
Fire and Explosion Prevention
- Heat treatment processes often involve high temperatures and flammable materials, increasing the risk of fire or explosion.
- Install fire suppression systems and ensure that fire extinguishers are readily accessible in the heat treatment area.
- Avoid using materials or gases that can react violently at high temperatures, and store flammable substances in designated, well-ventilated areas.
-
Quenching and Cooling Safety
- Quenching is a critical step in heat treatment, but it can pose risks such as thermal shock, cracking, or splashing of hot liquids.
- Use appropriate quenching media (e.g., oil, water, or polymer solutions) based on the material and desired properties.
- Ensure that quenching tanks are properly maintained and equipped with safety features like splash guards and temperature controls.
- Allow sufficient cooling time before handling treated parts to prevent burns or injuries.
-
Environmental and Health Considerations
- Heat treatment processes can generate hazardous fumes, dust, or waste materials that require proper disposal.
- Install ventilation systems to remove toxic gases and particulates from the workplace, ensuring compliance with environmental regulations.
- Provide employees with respiratory protection if necessary and monitor air quality regularly.
-
Quality Control and Testing
- Implement rigorous quality control measures to verify the effectiveness of heat treatment, such as hardness testing, microstructure analysis, or non-destructive testing (NDT).
- Document all process parameters (e.g., temperature, time, and atmosphere) to ensure traceability and consistency.
- Address any deviations or defects promptly to prevent further issues and maintain customer satisfaction.
-
Emergency Preparedness
- Develop and communicate an emergency response plan for incidents such as furnace failures, fires, or chemical spills.
- Ensure that all employees know the location of emergency exits, first aid kits, and firefighting equipment.
- Conduct regular drills to test the effectiveness of the emergency plan and identify areas for improvement.
By adhering to these precautions, manufacturers can minimize risks, enhance product quality, and create a safer working environment for employees. Heat treatment is a complex and potentially hazardous process, but with proper planning, training, and attention to detail, it can be performed efficiently and safely.
Summary Table:
Precaution | Key Details |
---|---|
Control of Atmosphere | Use inert gases or controlled atmospheres; monitor and calibrate systems. |
Temperature Regulation | Maintain precise control; use calibrated thermocouples and alarms. |
Material Handling | Clean materials; use proper fixtures; avoid overloading the furnace. |
Equipment Maintenance | Inspect and maintain furnaces, quenching systems, and cooling units regularly. |
Employee Training | Train on PPE use, safety protocols, and emergency response. |
Fire Prevention | Install fire suppression systems; store flammable materials safely. |
Quenching Safety | Use appropriate quenching media; equip tanks with safety features. |
Environmental Safety | Install ventilation systems; monitor air quality; provide respiratory protection. |
Quality Control | Perform hardness tests, microstructure analysis, and NDT; document parameters. |
Emergency Preparedness | Develop emergency response plans; conduct regular drills. |
Ensure your heat treatment processes are safe and efficient—contact our experts today for tailored solutions!