Hot forging is a manufacturing process that involves shaping metal using localized compressive forces at high temperatures. This method is widely used to produce a variety of components across industries due to its ability to enhance the mechanical properties of metals, such as strength and durability. Products made from hot forging are integral to industries like automotive, aerospace, construction, and heavy machinery. The process allows for the creation of complex shapes with high precision, making it ideal for critical components that require reliability and performance under stress.
Key Points Explained:
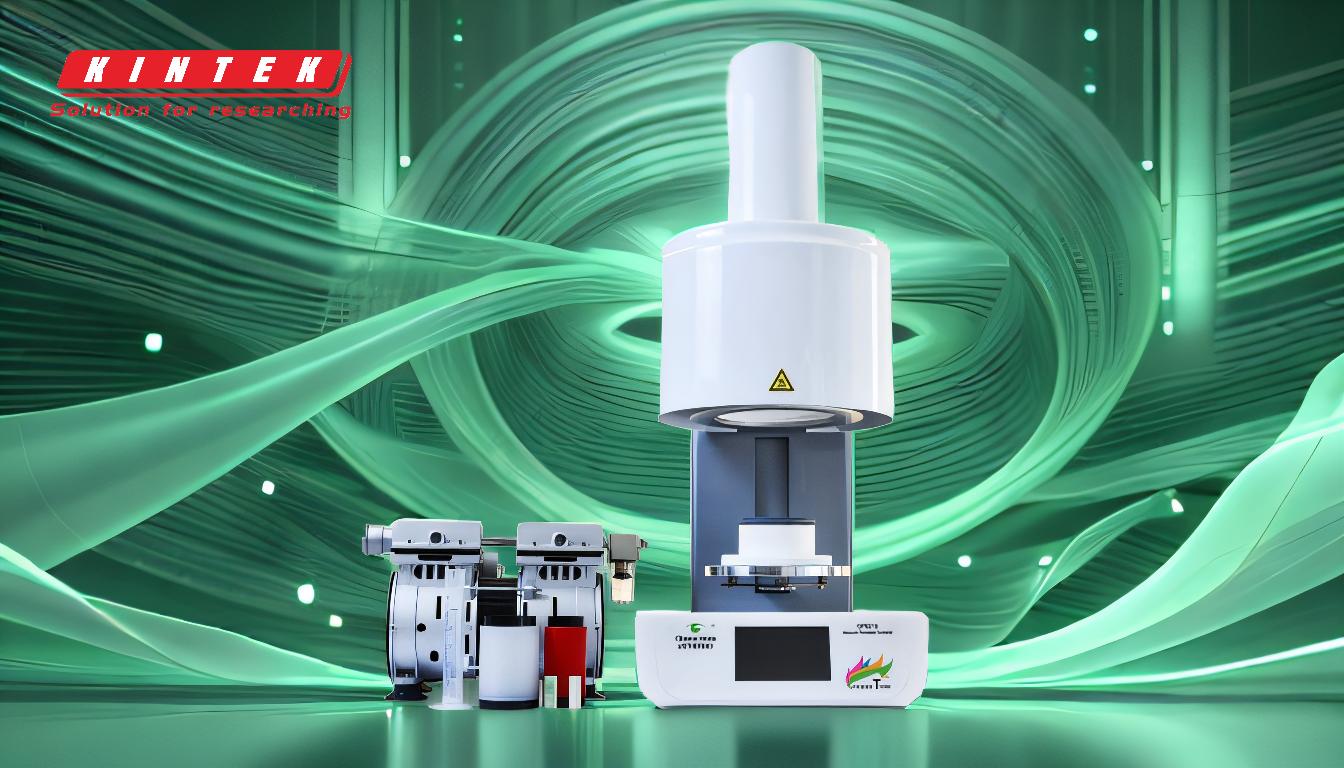
-
Automotive Components:
- Hot forging is extensively used in the automotive industry to produce high-strength parts such as crankshafts, connecting rods, and gears. These components must withstand extreme stress and wear, making hot forging an ideal manufacturing method due to its ability to improve the metal's grain structure and mechanical properties.
-
Aerospace Parts:
- The aerospace industry relies on hot forging for critical components like turbine blades, landing gear, and structural elements. These parts require exceptional strength-to-weight ratios and resistance to fatigue, which hot forging provides by refining the metal's microstructure.
-
Construction and Heavy Machinery:
- Hot-forged products are essential in construction and heavy machinery, including items like bolts, nuts, hydraulic cylinders, and excavator parts. These components need to endure heavy loads and harsh environmental conditions, making the durability and strength of hot-forged metals crucial.
-
Industrial Tools and Equipment:
- Tools such as wrenches, hammers, and pliers are often produced through hot forging. The process ensures these tools are robust and capable of withstanding repeated use without failure.
-
Oil and Gas Industry Components:
- Hot forging is used to create high-pressure valves, flanges, and fittings for the oil and gas sector. These parts must resist corrosion and maintain integrity under extreme pressures, which hot forging helps achieve.
-
Agricultural Machinery:
- Components like gears, shafts, and tiller blades in agricultural equipment are often hot-forged. The process ensures these parts can handle the demanding conditions of farming operations.
-
Consumer Goods:
- Everyday items such as kitchen utensils, hand tools, and hardware fittings are also produced using hot forging. The process provides the necessary strength and durability for these products.
-
Advantages of Hot Forging:
- Improved Mechanical Properties: Hot forging refines the grain structure of metals, enhancing their strength, toughness, and resistance to wear.
- Complex Shapes: The process allows for the creation of intricate geometries that are difficult to achieve with other manufacturing methods.
- Cost-Effectiveness: For high-volume production, hot forging is often more economical due to reduced material waste and lower machining requirements.
-
Materials Used in Hot Forging:
- Common materials include carbon steel, alloy steel, stainless steel, aluminum, and titanium. Each material is chosen based on the specific requirements of the final product, such as strength, weight, and corrosion resistance.
-
Future Trends in Hot Forging:
- Advancements in technology are leading to more precise and efficient hot forging processes. Innovations like computer-aided design (CAD) and simulation tools are enabling manufacturers to optimize designs and reduce production costs.
By leveraging the benefits of hot forging, manufacturers can produce high-quality, durable products that meet the demanding requirements of various industries. The process continues to evolve, offering new possibilities for innovation and efficiency in metalworking.
Summary Table:
Industry | Hot-Forged Products |
---|---|
Automotive | Crankshafts, connecting rods, gears |
Aerospace | Turbine blades, landing gear, structural elements |
Construction | Bolts, nuts, hydraulic cylinders, excavator parts |
Industrial Tools | Wrenches, hammers, pliers |
Oil and Gas | High-pressure valves, flanges, fittings |
Agricultural Machinery | Gears, shafts, tiller blades |
Consumer Goods | Kitchen utensils, hand tools, hardware fittings |
Interested in high-quality hot-forged products? Contact us today to learn more about our solutions!