In high-power pulsed magnetron sputtering (HiPIMS), the voltage pulse plays a critical role in determining the plasma characteristics, which in turn influence the deposition process. The voltage pulse affects the ionization of the sputtered material, plasma density, and energy distribution of the ions, all of which are essential for achieving high-quality thin films. The optimal voltage pulse depends on factors such as the target material, desired film properties, and the specific application. Typically, the voltage pulse in HiPIMS ranges from hundreds of volts to several kilovolts, with pulse durations in the microsecond to millisecond range. Balancing these parameters ensures efficient sputtering and high ionization rates while avoiding excessive target heating or arcing.
Key Points Explained:
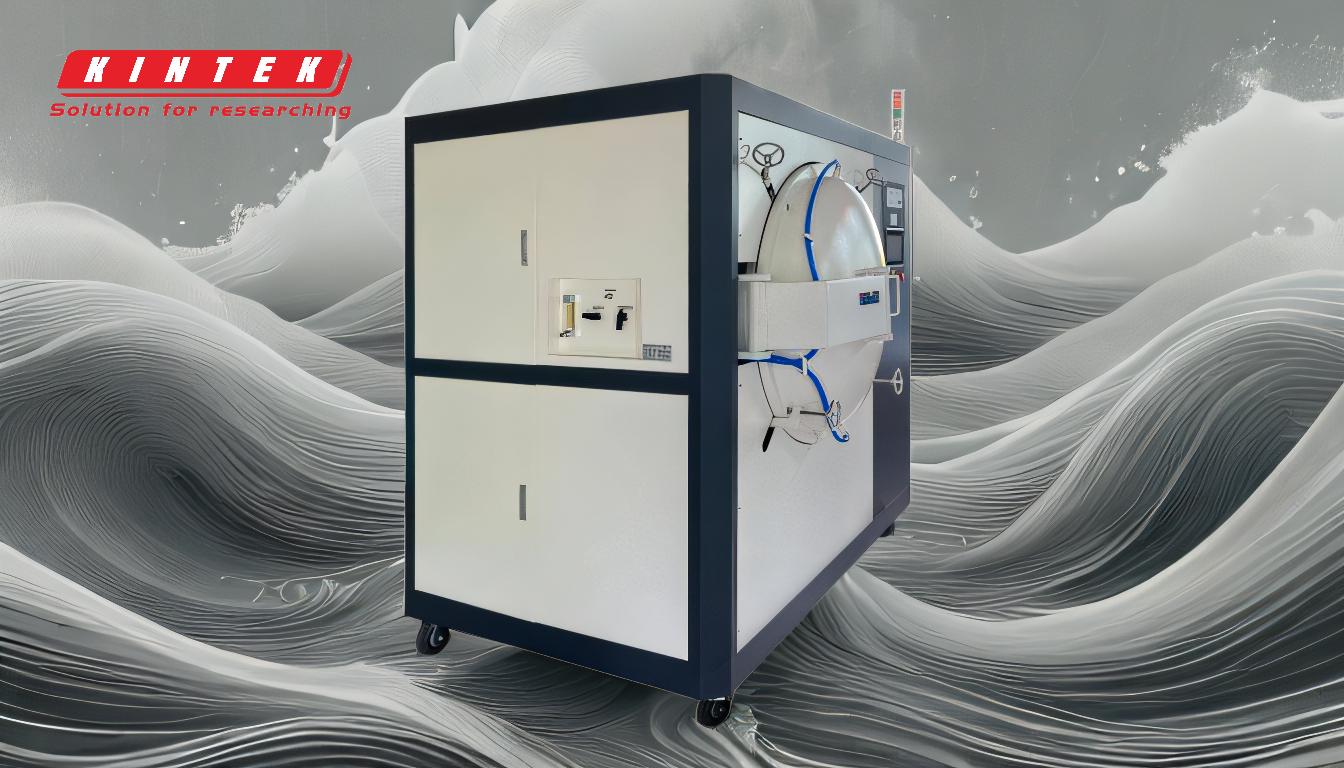
-
Role of Voltage Pulse in HiPIMS:
- The voltage pulse is a key parameter in HiPIMS, as it directly influences the ionization of the sputtered material and the plasma density.
- Higher voltage pulses result in increased ion energy and density, which can improve film quality by enhancing ion bombardment and adhesion.
- However, excessively high voltages can lead to target damage, arcing, or overheating, which may degrade the deposition process.
-
Typical Voltage Range:
- In HiPIMS, the voltage pulse typically ranges from 200 V to several kilovolts, depending on the target material and the desired film properties.
- For example, reactive sputtering of materials like titanium or aluminum often requires higher voltages (e.g., 500–1000 V) to achieve sufficient ionization and deposition rates.
-
Pulse Duration and Frequency:
- The pulse duration is another critical factor, usually ranging from 1 µs to several milliseconds.
- Shorter pulses (e.g., 1–10 µs) are often used to achieve high peak power densities, while longer pulses (e.g., 100 µs–1 ms) provide more stable plasma conditions.
- The pulse frequency, typically in the range of 100 Hz to several kHz, must be optimized to balance deposition rate and plasma stability.
-
Influence on Plasma Characteristics:
- The voltage pulse affects the plasma temperature, composition, and density, which are crucial for controlling the deposition process.
- Monitoring the elemental composition in the chamber ensures the desired material composition and checks for contamination, which can be influenced by the voltage pulse settings.
-
Optimization for Specific Applications:
- The optimal voltage pulse depends on the target material and the application. For example, hard coatings like TiN or DLC may require higher voltages and shorter pulses to achieve dense, high-adhesion films.
- For softer materials or applications requiring lower stress films, moderate voltages and longer pulses may be more suitable.
-
Challenges and Considerations:
- Maintaining stable plasma conditions is a challenge in HiPIMS, as high voltage pulses can lead to arcing or instabilities.
- Advanced power supplies with precise control over voltage, pulse duration, and frequency are essential for achieving consistent results.
- Real-time monitoring and feedback systems can help optimize the voltage pulse settings during the deposition process.
By carefully selecting and optimizing the voltage pulse parameters, HiPIMS can achieve superior film quality, high ionization rates, and precise control over the deposition process, making it a versatile technique for various applications in thin-film coating.
Summary Table:
Parameter | Typical Range | Key Influence |
---|---|---|
Voltage Pulse | 200 V to several kilovolts | Determines ionization, plasma density, and ion energy distribution. |
Pulse Duration | 1 µs to several milliseconds | Shorter pulses: high peak power; longer pulses: stable plasma conditions. |
Pulse Frequency | 100 Hz to several kHz | Balances deposition rate and plasma stability. |
Target Material | Depends on application | Hard coatings (e.g., TiN) require higher voltages; softer materials need moderate. |
Plasma Characteristics | Temperature, composition, density | Influenced by voltage pulse, critical for deposition control. |
Ready to optimize your HiPIMS process? Contact our experts today for tailored solutions!