Brazing is a metal-joining process that involves heating a filler metal above its melting point and distributing it between two or more close-fitting parts by capillary action. The temperature required for brazing typically ranges between 450°C (842°F) and 900°C (1652°F), depending on the materials being joined and the type of filler metal used. The process requires careful control of temperature to ensure proper flow of the filler metal without damaging the base materials. Below, we’ll explore the key factors influencing brazing temperature and how to determine the appropriate range for specific applications.
Key Points Explained:
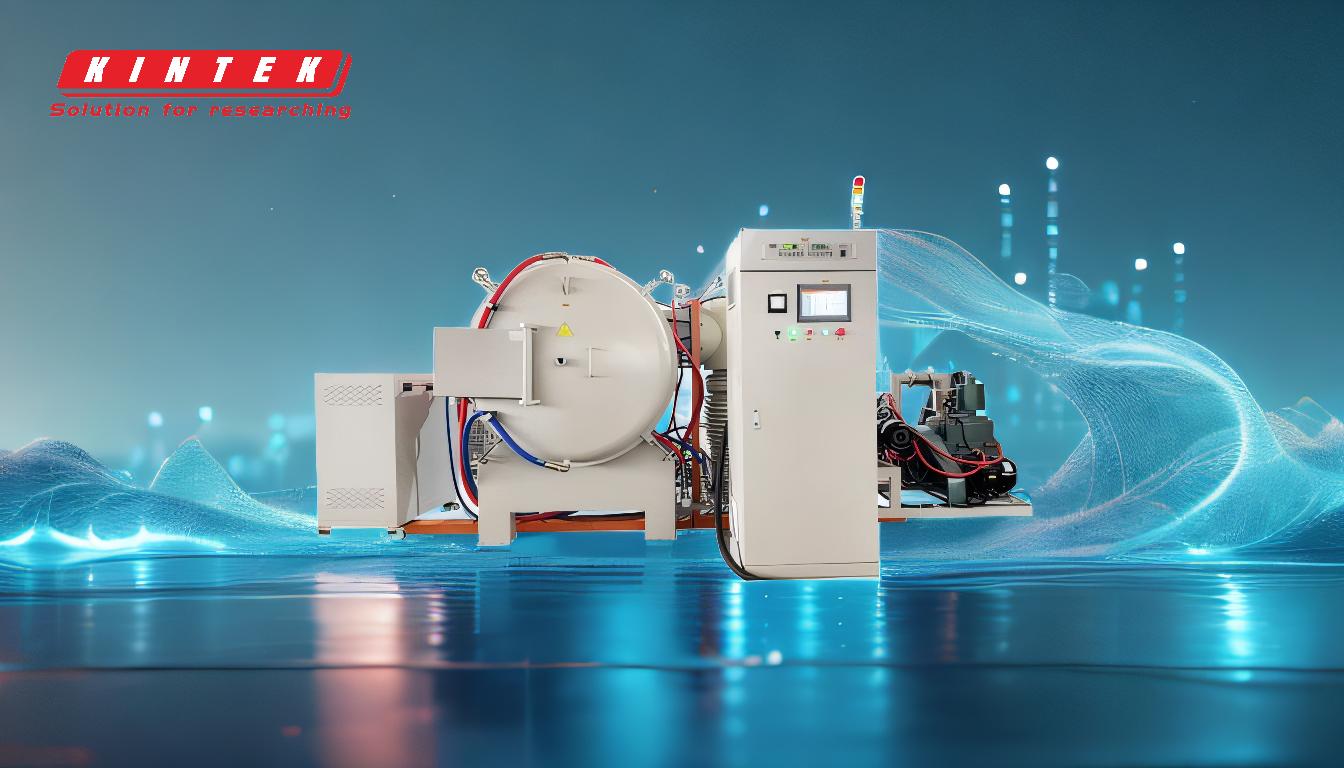
-
Definition of Brazing Temperature
- Brazing temperature refers to the range at which the filler metal melts and flows into the joint between the base metals.
- The temperature must be high enough to melt the filler metal but low enough to avoid melting the base materials.
-
Typical Temperature Range
- The general range for brazing is 450°C to 900°C (842°F to 1652°F).
- For example, silver-based filler metals typically melt between 600°C and 800°C (1112°F to 1472°F), while copper-based fillers require higher temperatures, often around 800°C to 900°C (1472°F to 1652°F).
-
Factors Influencing Brazing Temperature
- Base Material Properties: Different metals and alloys have varying melting points and thermal conductivities, which affect the required brazing temperature.
- Filler Metal Composition: The melting point of the filler metal determines the minimum brazing temperature. Common filler metals include silver, copper, aluminum, and nickel alloys.
- Joint Design: The gap between the parts being joined influences capillary action and heat distribution, impacting the optimal temperature.
- Atmosphere: The presence of a controlled atmosphere (e.g., inert gas or vacuum) can affect the brazing process and temperature requirements.
-
Importance of Temperature Control
- Avoiding Base Metal Damage: Excessive heat can warp or melt the base materials, compromising the joint’s integrity.
- Ensuring Proper Filler Metal Flow: Insufficient heat may prevent the filler metal from flowing adequately, leading to weak joints.
- Oxidation Prevention: Maintaining the correct temperature helps minimize oxidation, which can weaken the bond.
-
Determining the Right Temperature for Your Application
- Consult the filler metal manufacturer’s specifications for the recommended melting range.
- Consider the base materials’ melting points and thermal properties.
- Test the process on sample joints to fine-tune the temperature for optimal results.
-
Common Applications and Their Temperature Requirements
- Copper Tubing: Typically brazed at around 800°C (1472°F) using copper-phosphorus filler metals.
- Stainless Steel: Often brazed at 700°C to 900°C (1292°F to 1652°F) with silver-based or nickel-based fillers.
- Aluminum Components: Require lower temperatures, around 450°C to 600°C (842°F to 1112°F), using aluminum-silicon filler metals.
-
Equipment and Tools for Temperature Management
- Furnaces: Used for uniform heating in controlled environments.
- Torches: Provide localized heat for smaller or more intricate joints.
- Temperature Sensors: Ensure precise monitoring and control of the brazing process.
By understanding these key points, you can select the appropriate brazing temperature for your specific application, ensuring strong, durable, and reliable joints.
Summary Table:
Aspect | Details |
---|---|
Typical Temperature Range | 450°C to 900°C (842°F to 1652°F) |
Filler Metal Examples | Silver-based: 600°C–800°C, Copper-based: 800°C–900°C, Aluminum: 450°C–600°C |
Key Influencing Factors | Base material, filler metal, joint design, and atmosphere |
Applications | Copper tubing: ~800°C, Stainless steel: 700°C–900°C, Aluminum: 450°C–600°C |
Need help determining the right brazing temperature for your project? Contact our experts today!