Vacuum casting is a specialized process used in manufacturing and materials science to create high-quality, precise components under controlled conditions. The temperature at which vacuum casting is performed depends on the material being cast and the specific requirements of the process. Generally, the temperature must be high enough to melt the material but controlled to prevent oxidation or contamination. The vacuum environment ensures that the material is free from impurities, leading to superior mechanical properties and surface finishes. Below, we explore the key aspects of vacuum casting temperature and its implications.
Key Points Explained:
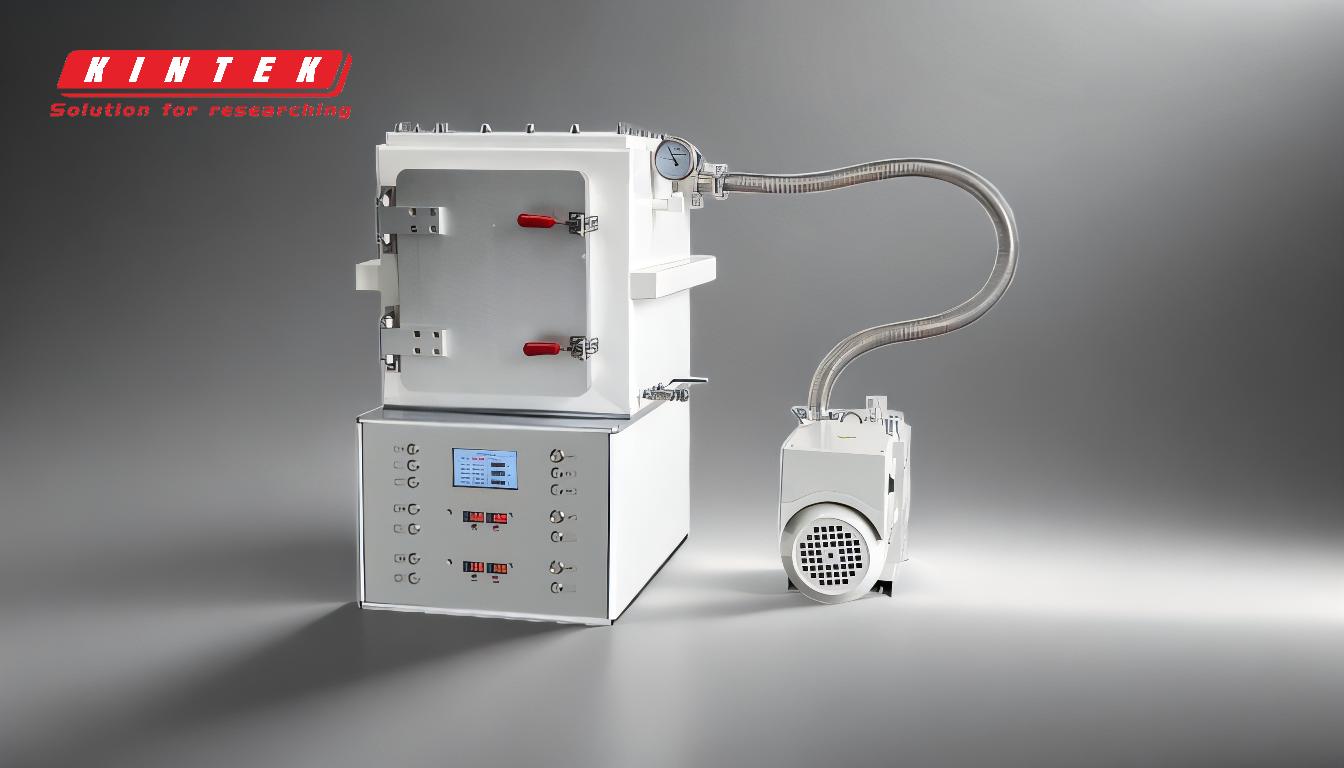
-
Understanding Vacuum Casting:
- Vacuum casting involves melting a material in a vacuum environment to eliminate impurities and oxidation. The process is commonly used for metals, alloys, and high-performance polymers.
- The vacuum furnace is the primary equipment used, which allows precise control over temperature, pressure, and cooling rates.
-
Temperature Range for Vacuum Casting:
- The temperature for vacuum casting varies depending on the material:
- Metals and Alloys: For metals like aluminum, the casting temperature typically ranges between 660°C to 800°C. For higher-melting-point metals like titanium, temperatures can exceed 1600°C.
- Polymers and Composites: For materials like polyurethane or epoxy, the temperature is much lower, usually between 60°C to 120°C.
- The exact temperature is determined by the material's melting point, thermal stability, and desired properties.
- The temperature for vacuum casting varies depending on the material:
-
Importance of Vacuum Environment:
- A vacuum environment prevents oxidation and contamination, which is critical for achieving high-quality castings. This is especially important for reactive metals like titanium or magnesium.
- The vacuum also helps in degassing the molten material, removing trapped gases that could weaken the final product.
-
Heating and Cooling Process:
- The furnace heats the material to the required temperature using precise controls. Once the material is molten, it is poured into a mold under vacuum conditions.
- Cooling is often done using inert gases like argon to prevent chemical reactions and ensure uniform solidification.
-
Factors Influencing Casting Temperature:
- Material Properties: The melting point, thermal conductivity, and reactivity of the material dictate the required temperature.
- Component Complexity: Complex geometries may require precise temperature control to ensure proper flow and filling of the mold.
- Desired Mechanical Properties: Higher temperatures may be needed for materials requiring superior strength or specific microstructures.
-
Applications of Vacuum Casting:
- Vacuum casting is widely used in industries such as aerospace, automotive, and medical devices, where high precision and material integrity are critical.
- Common applications include turbine blades, surgical instruments, and high-performance polymer components.
-
Equipment Considerations:
- A vacuum furnace is essential for this process, equipped with temperature controls, vacuum pumps, and inert gas systems.
- The furnace must be capable of reaching and maintaining the required temperature consistently.
In summary, the temperature for vacuum casting depends on the material and application, ranging from a few hundred degrees Celsius for polymers to over 1600°C for high-performance metals. The vacuum environment ensures high-quality results by eliminating impurities and oxidation. Understanding these factors is crucial for achieving optimal outcomes in vacuum casting processes.
Summary Table:
Material Type | Temperature Range |
---|---|
Metals & Alloys (e.g., Aluminum) | 660°C to 800°C |
High-Performance Metals (e.g., Titanium) | Above 1600°C |
Polymers & Composites (e.g., Polyurethane) | 60°C to 120°C |
Need help optimizing your vacuum casting process? Contact our experts today for tailored solutions!