Clay sintering is a critical process in ceramics, where clay particles bond together at high temperatures to form a dense, solid structure. The sintering temperature for clay typically ranges between 1000°C and 1800°C, depending on the type of clay, its composition, and the desired properties of the final product. For example, some experiments use sintering temperatures as high as 1800°C, while other kilns are designed to reach a maximum of 1288°C. The sintering process is influenced by factors such as the ramp rate, hold time, and cooling rate, particularly between 900°C and the peak temperature. Achieving optimal density and strength often requires sintering at 50% to 75% of the material's melting temperature, which is usually above 1000°C.
Key Points Explained:
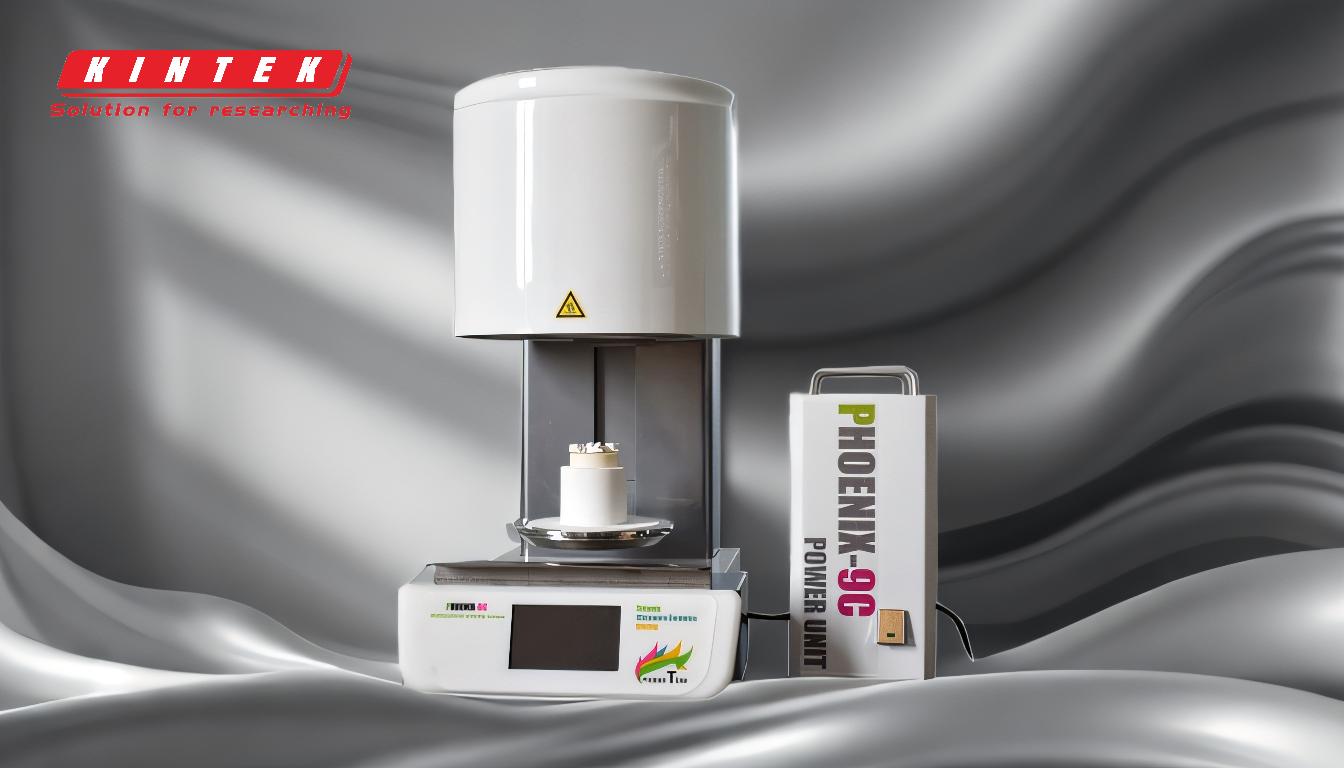
-
Sintering Temperature Range for Clay:
- Clay sintering typically occurs between 1000°C and 1800°C.
- The exact temperature depends on the type of clay, its mineral composition, and the desired properties of the final ceramic product.
- For example, some experiments use a sintering temperature of 1800°C, while other kilns are designed to reach a maximum of 1288°C.
-
Factors Influencing Sintering:
- Ramp Rate: The rate at which the temperature increases, especially from 900°C to the peak temperature, is critical. A controlled ramp rate ensures uniform heating and prevents defects.
- Hold Time: Maintaining a consistent temperature during the hold time is essential for achieving a dense and homogeneous structure.
- Cooling Rate: The rate at which the material cools back to about 900°C affects the final properties, such as strength and thermal shock resistance.
-
Relationship Between Sintering Temperature and Melting Point:
- To achieve more than 95% of their theoretical density, ceramic materials need to be sintered at 50% to 75% of their melting temperature.
- Since the melting temperature of most clays is typically greater than 1000°C, sintering temperatures are usually above this threshold.
-
Practical Considerations for Equipment and Consumables:
- Kiln Design: Ensure the kiln can reach and maintain the required sintering temperature. For example, some kilns are designed to reach a maximum of 1288°C, which may not be sufficient for all types of clay.
- Energy Efficiency: Higher sintering temperatures, such as 1800°C, require more energy, so consider the cost and efficiency of the equipment.
- Material Selection: Choose clays and additives that sinter effectively within the available temperature range of your equipment.
-
Impact of Temperature on Final Product:
- Density and Strength: Higher sintering temperatures generally result in denser and stronger ceramics.
- Color and Finish: The sintering temperature can also affect the color and surface finish of the final product, which may be important for aesthetic applications.
By understanding these key points, purchasers of equipment and consumables can make informed decisions about the materials and tools needed for successful clay sintering.
Summary Table:
Key Aspect | Details |
---|---|
Sintering Temperature Range | 1000°C–1800°C, depending on clay type and desired properties. |
Influencing Factors | Ramp rate, hold time, cooling rate (especially between 900°C and peak temp). |
Melting Point Relationship | Sinter at 50%–75% of melting temperature (typically >1000°C). |
Equipment Considerations | Kiln design, energy efficiency, and material selection. |
Final Product Impact | Higher temps yield denser, stronger ceramics and affect color/finish. |
Optimize your clay sintering process—contact our experts today for tailored solutions!