Diffusion bonding is a solid-state joining process that occurs at high temperatures, typically within the range of 50% to 75% of the melting point of the materials being bonded. This process relies on atomic diffusion across the interface of the materials, which is facilitated by elevated temperatures. The exact temperature depends on the specific materials involved, but it generally falls within the range of 900 to 1400 ℃, as seen in processes like CVD (Chemical Vapor Deposition) where diffusion control is achieved at high temperatures.
Key Points Explained:
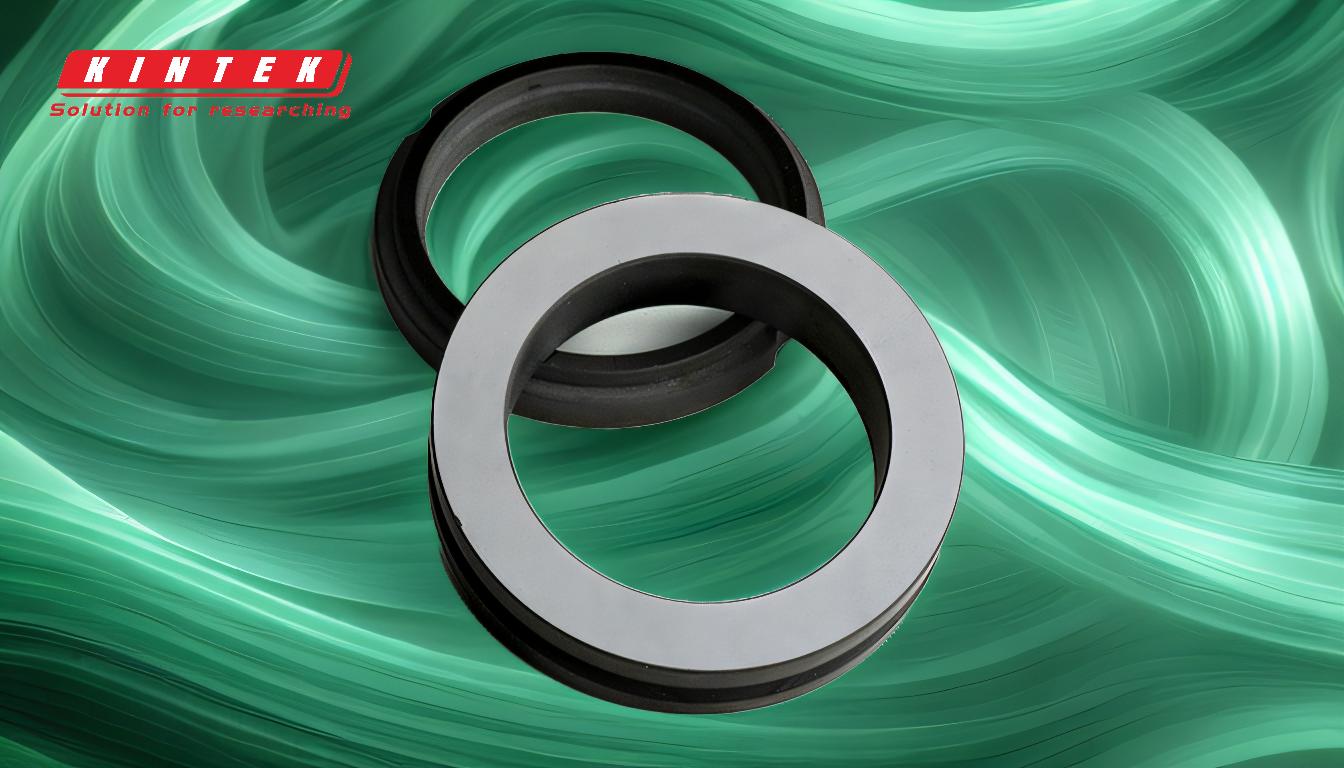
-
Temperature Range for Diffusion Bonding:
- Diffusion bonding typically occurs at high temperatures, often between 50% and 75% of the melting point of the materials being bonded. For many metals, this translates to a range of approximately 900 to 1400 ℃.
- This temperature range ensures that atomic diffusion is sufficiently active to allow the materials to bond without reaching their melting points.
-
Role of Temperature in Diffusion Control:
- At high temperatures, atomic mobility increases, which is essential for diffusion bonding. The process relies on the movement of atoms across the interface of the materials to create a strong bond.
- In CVD technology, for example, diffusion control is achieved at high temperatures (900 to 1400 ℃), which aligns with the conditions required for effective diffusion bonding.
-
Material-Specific Considerations:
- The exact temperature for diffusion bonding varies depending on the materials involved. For instance, titanium alloys may require temperatures around 900 to 1000 ℃, while nickel-based superalloys might need temperatures closer to 1200 to 1400 ℃.
- Understanding the melting points and diffusion characteristics of the materials is crucial for determining the optimal bonding temperature.
-
Kinetic vs. Diffusion Control:
- Kinetic control, which is typically carried out at lower temperatures, focuses on the rate of chemical reactions. In contrast, diffusion control, which occurs at higher temperatures, emphasizes the movement of atoms across material interfaces.
- For diffusion bonding, the high-temperature regime (900 to 1400 ℃) is necessary to ensure that diffusion processes dominate, leading to a strong and durable bond.
-
Practical Implications for Equipment and Consumables Purchasers:
- When selecting equipment for diffusion bonding, it is essential to choose systems capable of maintaining consistent high temperatures within the required range (900 to 1400 ℃).
- Consumables, such as protective atmospheres or filler materials, should also be selected based on their compatibility with the high-temperature environment required for diffusion bonding.
By understanding these key points, purchasers can make informed decisions about the equipment and materials needed for successful diffusion bonding processes.
Summary Table:
Aspect | Details |
---|---|
Temperature Range | 900 to 1400 ℃ (50%-75% of material melting point) |
Role of High Temperature | Enhances atomic diffusion for strong bonding |
Material-Specific Examples | Titanium alloys: 900-1000 ℃, Nickel-based superalloys: 1200-1400 ℃ |
Kinetic vs. Diffusion | Diffusion control requires high temperatures for atomic movement |
Equipment Considerations | Systems must maintain consistent high temperatures (900-1400 ℃) |
Need help selecting the right equipment for diffusion bonding? Contact our experts today!