Aluminum vacuum brazing is a specialized process used to join aluminum components without the need for flux. The temperature range for aluminum vacuum brazing typically falls between 570°C and 620°C (1058°F to 1148°F). This temperature range is critical because it ensures the brazing filler metal melts and flows properly, creating strong, leak-tight joints. The process requires precise temperature control and uniformity to avoid overheating or underheating, which can compromise the integrity of the brazed joints. A vacuum brazing furnace is essential for this process, as it provides the controlled environment needed to achieve optimal results.
Key Points Explained:
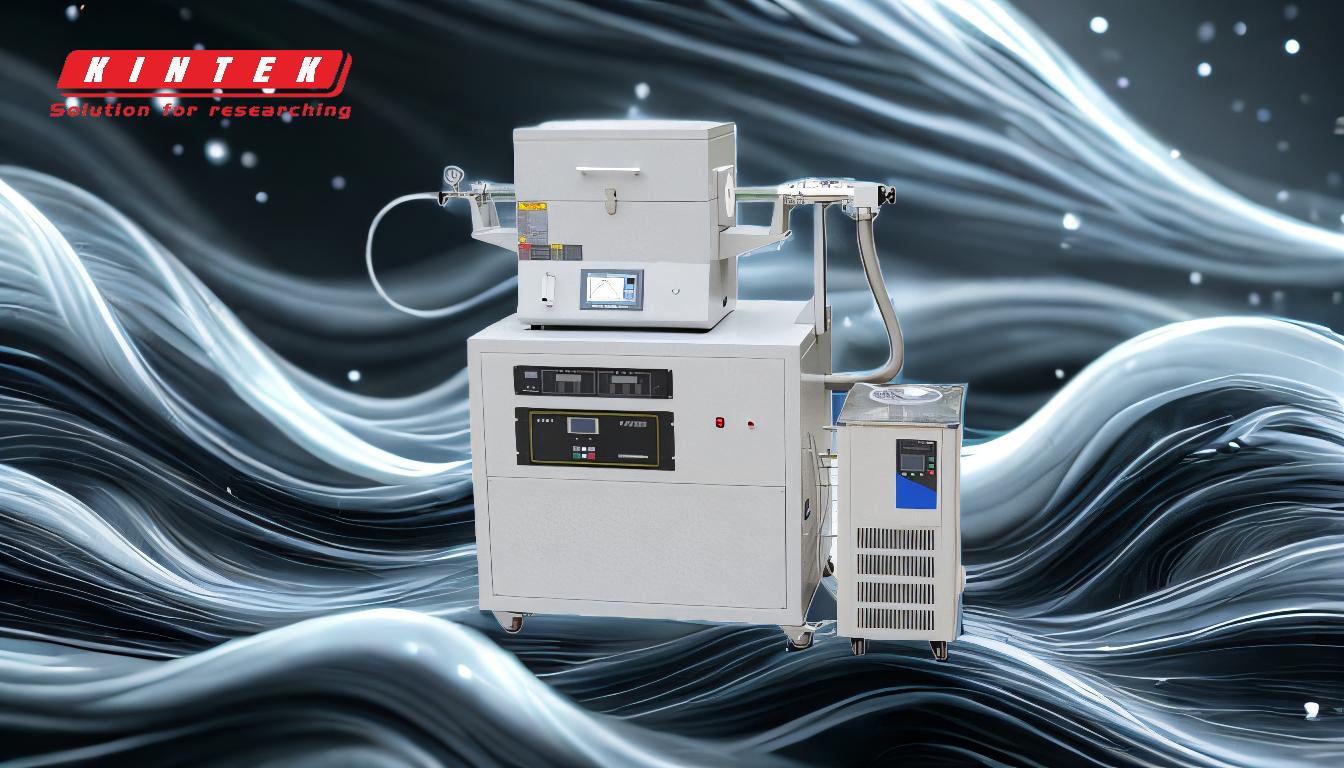
-
Temperature Range for Aluminum Vacuum Brazing:
- The optimal temperature range for aluminum vacuum brazing is 570°C to 620°C (1058°F to 1148°F). This range ensures the brazing filler metal melts and flows properly, creating strong, leak-tight joints.
- Temperatures below this range may result in incomplete melting of the filler metal, leading to weak joints, while temperatures above this range can cause overheating, leading to distortion or damage to the aluminum parts.
-
Importance of Temperature Control and Uniformity:
- Temperature control is critical in aluminum vacuum brazing to ensure consistent results. The process relies on maintaining a uniform temperature across the entire workpiece to achieve proper filler metal flow and joint formation.
- Inconsistent temperatures can lead to defects such as voids, incomplete joints, or overheating of specific areas, which can compromise the structural integrity of the brazed assembly.
-
Role of Heating Control Zones and Heating Element Design:
- A vacuum brazing furnace typically uses multiple heating control zones to achieve precise temperature control and uniformity. These zones allow for adjustments to be made in different areas of the furnace to compensate for variations in heat distribution.
- The design of the heating elements is also crucial. They must maintain their surface temperature as close as possible to the required part temperature to avoid overheating the parts' surface. This ensures that the parts are heated evenly and prevents localized overheating or underheating.
-
Preventing Overheating:
- Overheating can cause the aluminum parts to warp, melt, or develop surface defects. To prevent this, the furnace must maintain a consistent temperature and avoid sudden fluctuations.
- The heating elements' surface temperature should be carefully monitored and controlled to ensure it matches the required part temperature. This minimizes the risk of overheating the parts' surface while ensuring the filler metal reaches its melting point.
-
Advantages of Vacuum Brazing for Aluminum:
- Vacuum brazing eliminates the need for flux, which can leave residues or cause contamination. This results in clean, high-quality joints with excellent corrosion resistance.
- The controlled environment of a vacuum brazing furnace also prevents oxidation, ensuring the aluminum surfaces remain clean and free from oxides that could interfere with the brazing process.
-
Applications of Aluminum Vacuum Brazing:
- This process is widely used in industries such as aerospace, automotive, and electronics, where strong, lightweight, and corrosion-resistant joints are required.
- Common applications include heat exchangers, evaporators, condensers, and other components that require precise and reliable joining of aluminum parts.
By understanding the temperature requirements and the importance of precise control in aluminum vacuum brazing, manufacturers can achieve high-quality, durable joints that meet the demands of modern engineering applications.
Summary Table:
Key Aspect | Details |
---|---|
Optimal Temperature Range | 570°C to 620°C (1058°F to 1148°F) |
Purpose | Ensures filler metal melts and flows properly for strong, leak-tight joints |
Temperature Control | Critical to avoid overheating or underheating |
Heating Control Zones | Multiple zones for uniform temperature distribution |
Advantages | No flux required, clean joints, excellent corrosion resistance |
Applications | Aerospace, automotive, electronics, heat exchangers, and more |
Need expert advice on aluminum vacuum brazing? Contact us today to achieve optimal results!