The temperature for DLC (Diamond-Like Carbon) application varies depending on the coating method and substrate material. For PVD (Physical Vapor Deposition) coatings, which are commonly used for DLC, the substrate temperature typically ranges from 200-400°C (392-752°F). This is lower than CVD (Chemical Vapor Deposition) processes, which operate at much higher temperatures (600-1100°C or 1112-2012°F). For heat-sensitive materials, pre-tempering at 900-950°F (482-510°C) may be required to minimize distortion. The choice of temperature depends on the substrate material and desired coating properties, with lower temperatures generally preferred for materials like aluminum or plastics to avoid thermal damage.
Key Points Explained:
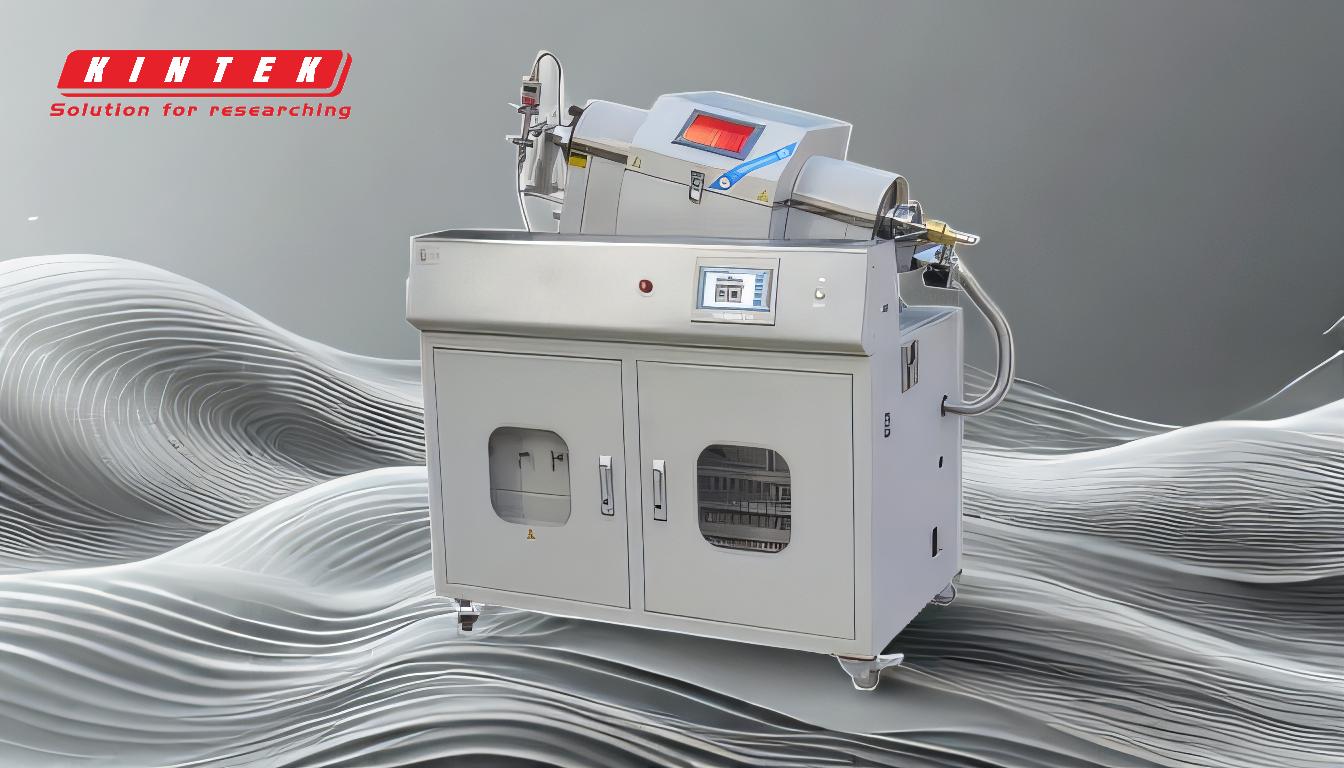
-
Temperature Range for DLC Application:
- PVD Coating: The substrate temperature during PVD coating, commonly used for DLC, typically ranges from 200-400°C (392-752°F). This is significantly lower than CVD processes, making PVD suitable for heat-sensitive materials.
- CVD Coating: CVD processes for diamond-like coatings operate at much higher temperatures, typically between 600-1100°C (1112-2012°F). These high temperatures can cause thermal effects like phase changes in steel substrates.
-
Substrate Material Considerations:
- Heat-Sensitive Materials: For materials like aluminum or plastics, lower temperatures (below 400°F or 204°C) are preferred to avoid melting or distortion. PVD is often chosen for these materials due to its lower operating temperature.
- Steel and Other Metals: For steel substrates, higher temperatures may be used, but pre-tempering at 900-950°F (482-510°C) is often required to minimize distortion during coating.
-
Thermal Effects and Post-Treatment:
- Thermal Distortion: High coating temperatures can alter the hardness of parts or cause distortion. This is particularly relevant for CVD processes, where temperatures can exceed 600°C.
- Post-Coating Heat Treatment: After high-temperature CVD coating, substrates like steel may require heat treatment to optimize properties, such as returning to the desired phase or relieving internal stresses.
-
Diamond Film Deposition:
- Diamond films, a related material to DLC, are typically deposited at temperatures between 600-1100°C (1112-2012°F). Temperatures exceeding 1200°C (2192°F) can cause graphitization, degrading the coating quality.
-
Process Temperature Control:
- The process temperature can be controlled based on the substrate material, ranging from 50°F to 400°F (10°C to 204°C) for materials like zinc, brass, steel, or plastic. This flexibility allows for tailored coating processes to suit specific material properties and application requirements.
By understanding these key points, equipment and consumable purchasers can make informed decisions about the appropriate coating process and temperature for their specific application, ensuring optimal performance and longevity of the coated parts.
Summary Table:
Aspect | PVD Coating | CVD Coating |
---|---|---|
Temperature Range | 200-400°C (392-752°F) | 600-1100°C (1112-2012°F) |
Suitable Materials | Heat-sensitive (e.g., aluminum, plastics) | Steel and metals (with pre-tempering) |
Thermal Effects | Minimal distortion | Potential phase changes in steel |
Post-Treatment | Not typically required | Heat treatment often needed |
Need help selecting the right DLC coating process for your materials? Contact our experts today for tailored solutions!