The application temperature for DLC (Diamond-Like Carbon) coatings varies depending on the deposition method used. For Chemical Vapor Deposition (CVD), temperatures typically range between 600°C to 1100°C, which can affect the substrate material's properties. In contrast, Physical Vapor Deposition (PVD) processes, which are more commonly used for DLC coatings, operate at much lower temperatures, typically between 200°C to 400°C. This lower temperature range is suitable for heat-sensitive materials and helps minimize thermal distortion or changes in substrate hardness. The choice of temperature is crucial to ensure the desired coating properties, such as hardness and low friction, while preserving the integrity of the substrate material.
Key Points Explained:
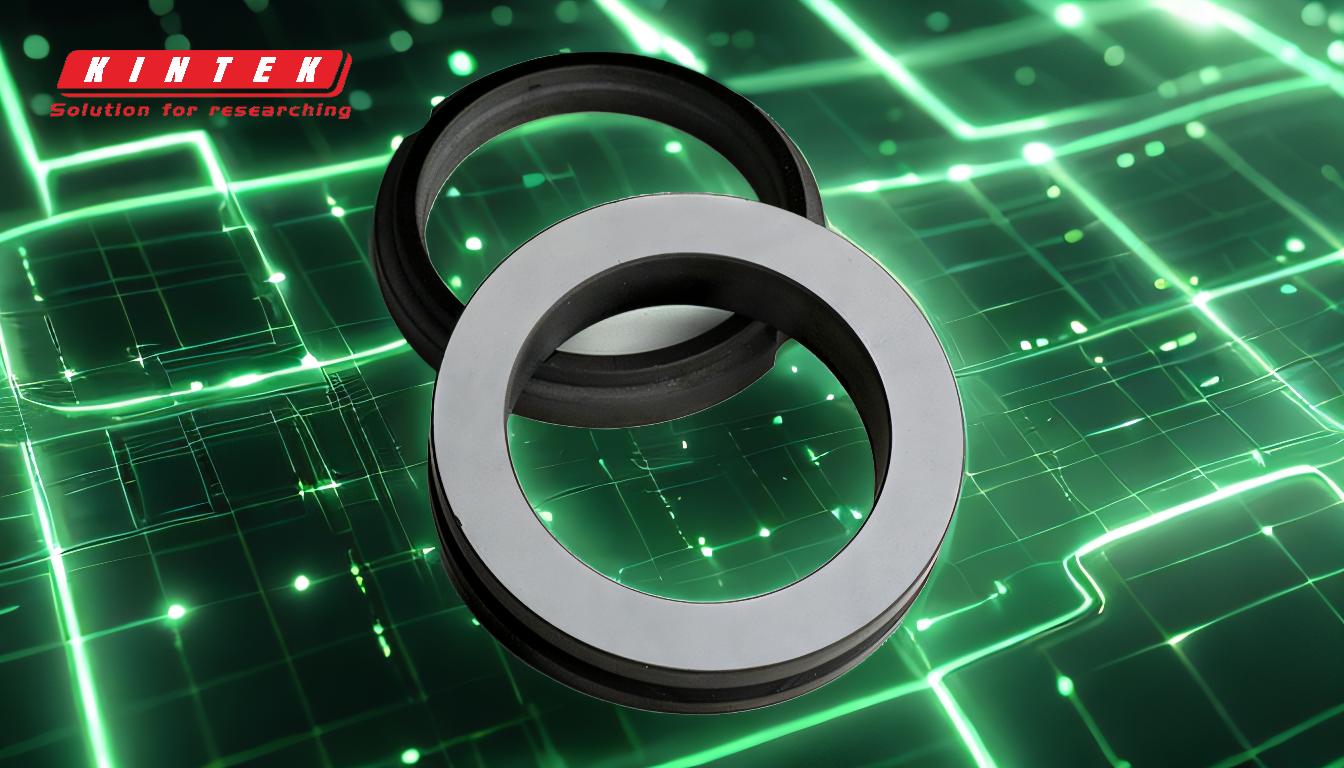
-
Temperature Ranges for DLC Coating Application:
- CVD Process: Operates at high temperatures, typically between 600°C to 1100°C. This high-temperature environment can lead to significant thermal effects on the substrate, such as phase changes in steels or distortion in heat-sensitive materials.
- PVD Process: Operates at lower temperatures, generally between 200°C to 400°C. This makes PVD more suitable for heat-sensitive substrates and helps maintain the structural integrity of the material.
-
Impact of Temperature on Substrate and Coating Properties:
- High Temperatures (CVD): Can alter the substrate's microstructure, such as heating steels into the austenite phase region. Post-coating heat treatment may be required to optimize substrate properties.
- Low Temperatures (PVD): Minimize thermal distortion and changes in substrate hardness, making it ideal for materials like aluminum or plastics that cannot withstand high temperatures.
-
Material Considerations:
- Heat-Sensitive Materials: For materials like aluminum or plastics, PVD is preferred due to its lower operating temperatures.
- Steel and Other Metals: CVD can be used, but care must be taken to manage thermal effects, and post-coating heat treatment may be necessary.
-
Coating Characteristics:
- DLC Coatings: Comprise Sp3 (diamond-like) and Sp2 (graphite-like) carbon bonds, providing high hardness, low friction, and excellent performance in corrosive environments.
- Temperature Influence: High temperatures (above 1200°C) can cause graphitization, reducing the coating's effectiveness.
-
Practical Implications for Equipment and Consumable Purchasers:
- Substrate Compatibility: Ensure the chosen coating process aligns with the substrate material's thermal tolerance.
- Post-Coating Treatments: For high-temperature processes like CVD, factor in additional heat treatment steps to optimize substrate properties.
- Coating Performance: Consider the intended application environment (e.g., corrosive or high-wear conditions) to select the appropriate coating method and temperature range.
By understanding these key points, purchasers can make informed decisions about the appropriate DLC coating process and temperature range for their specific application, ensuring optimal performance and substrate integrity.
Summary Table:
Deposition Method | Temperature Range | Suitable Materials | Key Considerations |
---|---|---|---|
CVD | 600°C to 1100°C | Steel, Metals | High thermal effects, post-treatment may be needed |
PVD | 200°C to 400°C | Aluminum, Plastics | Minimal thermal distortion, ideal for heat-sensitive materials |
Need help choosing the right DLC coating process for your application? Contact our experts today!