Calcination is a thermal treatment process that involves heating materials to high temperatures in the absence or limited supply of air or oxygen. The primary purpose is to drive off moisture, remove volatile substances, and induce thermal decomposition or phase transitions. The type of furnace used for calcination depends on the material being processed, the required temperature, and the specific application. Common furnace types include muffle furnaces, rotary kilns, and sintering furnaces. Below, we explore the key considerations and types of furnaces suitable for calcination.
Key Points Explained:
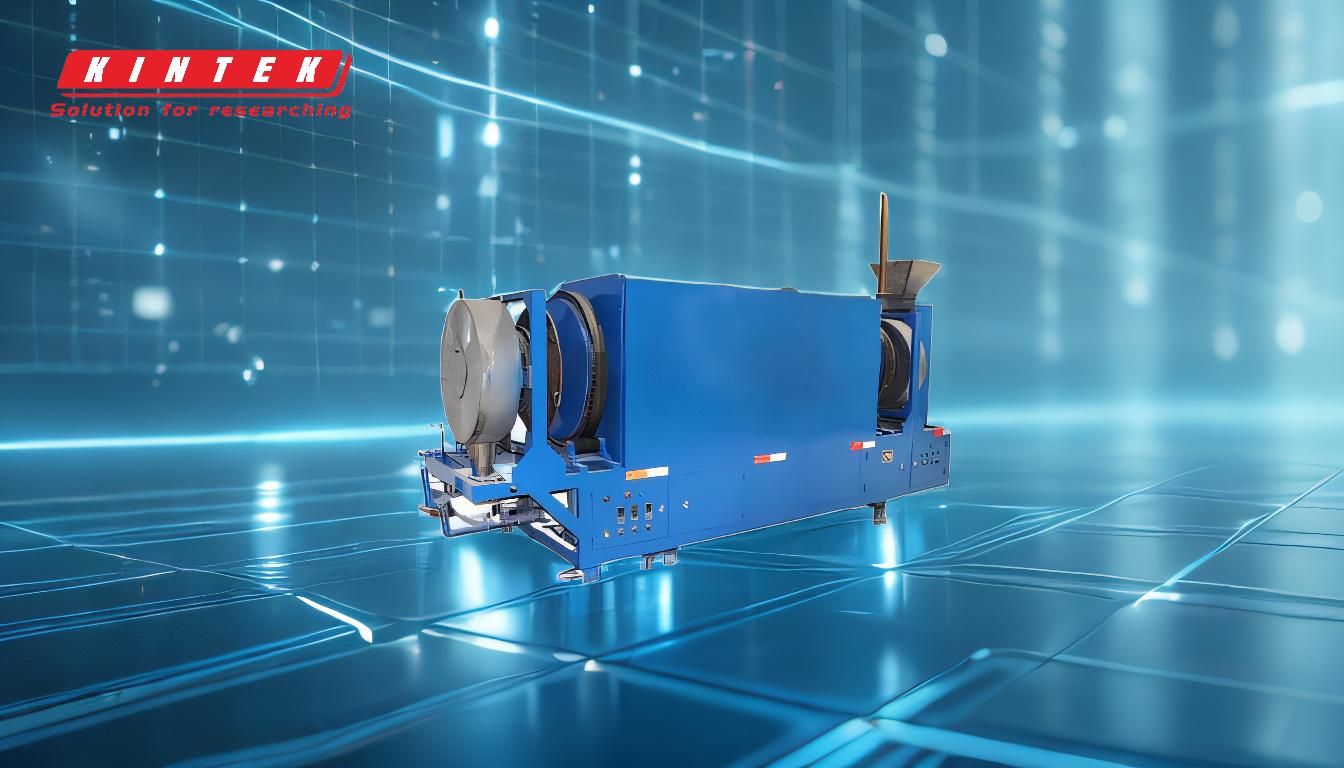
-
Purpose of Calcination:
- Calcination is used to remove moisture, volatile substances, and impurities from materials.
- It can also induce phase changes or chemical reactions, such as converting carbonates to oxides.
- The process is critical in industries like cement production, metallurgy, and ceramics.
-
Types of Furnaces for Calcination:
-
Muffle Furnace:
- A muffle furnace is a common choice for calcination in laboratory and small-scale industrial settings.
- It provides a controlled environment with uniform heating, making it ideal for precise thermal treatment.
- The absence of direct flame contact ensures that the material is not contaminated.
-
Rotary Kiln:
- Rotary kilns are widely used for large-scale calcination processes, such as in cement and lime production.
- They allow continuous processing of materials and can handle high throughput.
- The rotating drum ensures even heating and efficient heat transfer.
-
Sintering Furnace:
- Sintering furnaces are used for calcination processes that involve compacting and heating powdered materials.
- They are particularly useful in metallurgy and ceramics for creating dense, solid structures from powders.
- The controlled atmosphere in sintering furnaces prevents oxidation or contamination.
-
Muffle Furnace:
-
Key Features of Calcination Furnaces:
-
Temperature Control:
- Calcination often requires precise temperature control, as different materials have specific temperature thresholds for decomposition or phase changes.
- Furnaces must be capable of reaching and maintaining high temperatures (often above 1000°C).
-
Atmosphere Control:
- The absence or limited supply of oxygen is crucial for many calcination processes.
- Furnaces with sealed chambers or inert gas environments are preferred to prevent unwanted oxidation.
-
Heating Uniformity:
- Uniform heating ensures consistent results and prevents localized overheating or underheating.
- This is particularly important for materials that undergo phase transitions or chemical reactions.
-
Temperature Control:
-
Applications of Calcination Furnaces:
-
Cement Industry:
- Calcination is a critical step in producing clinker, the intermediate product in cement manufacturing.
- Rotary kilns are commonly used for this purpose due to their high capacity and efficiency.
-
Metallurgy:
- Calcination is used to convert metal carbonates or hydroxides into oxides, which are then reduced to pure metals.
- Sintering furnaces are often employed in this process.
-
Ceramics and Refractories:
- Calcination is used to remove impurities and improve the mechanical properties of ceramic materials.
- Muffle furnaces are suitable for small-scale or precision applications.
-
Cement Industry:
-
Considerations for Choosing a Calcination Furnace:
-
Material Properties:
- The type of material being calcined (e.g., carbonate, hydroxide, or organic compound) determines the required temperature and atmosphere.
-
Scale of Operation:
- Laboratory-scale processes may require smaller, more precise furnaces like muffle furnaces.
- Industrial-scale operations often use rotary kilns or sintering furnaces for high throughput.
-
Energy Efficiency:
- Furnaces with good insulation and heat recovery systems can reduce energy consumption and operational costs.
-
Maintenance and Durability:
- High-temperature furnaces must be constructed from durable materials to withstand thermal stress and corrosion.
-
Material Properties:
In summary, the choice of furnace for calcination depends on the specific requirements of the material and process. Muffle furnaces are ideal for laboratory and small-scale applications, while rotary kilns and sintering furnaces are better suited for industrial-scale operations. Each type of furnace offers unique advantages in terms of temperature control, atmosphere management, and heating uniformity, making them indispensable tools in various industries.
Summary Table:
Furnace Type | Key Features | Applications |
---|---|---|
Muffle Furnace | Controlled environment, uniform heating, no contamination | Laboratory and small-scale industrial calcination, ceramics, and refractories |
Rotary Kiln | Continuous processing, high throughput, even heating | Cement and lime production, large-scale industrial calcination |
Sintering Furnace | Compacting powdered materials, controlled atmosphere, prevents oxidation | Metallurgy, ceramics, creating dense solid structures from powders |
Need help choosing the right furnace for calcination? Contact our experts today for tailored solutions!