Calcination and smelting are high-temperature processes that require specialized furnaces to achieve the desired chemical and physical transformations. Calcination involves heating materials to high temperatures in the absence or limited supply of air to induce thermal decomposition, while smelting involves melting ores to extract metals. The types of furnaces used for these processes include muffle furnaces, reverberatory furnaces, shaft furnaces, and rotary kilns. These furnaces are designed to provide uniform heating, precise temperature control, and the ability to handle large volumes of materials. Industrial applications often use fired or electric process furnaces, depending on cost and environmental considerations. Below, we explore the key types of furnaces used for calcination and smelting, their configurations, and their applications.
Key Points Explained:
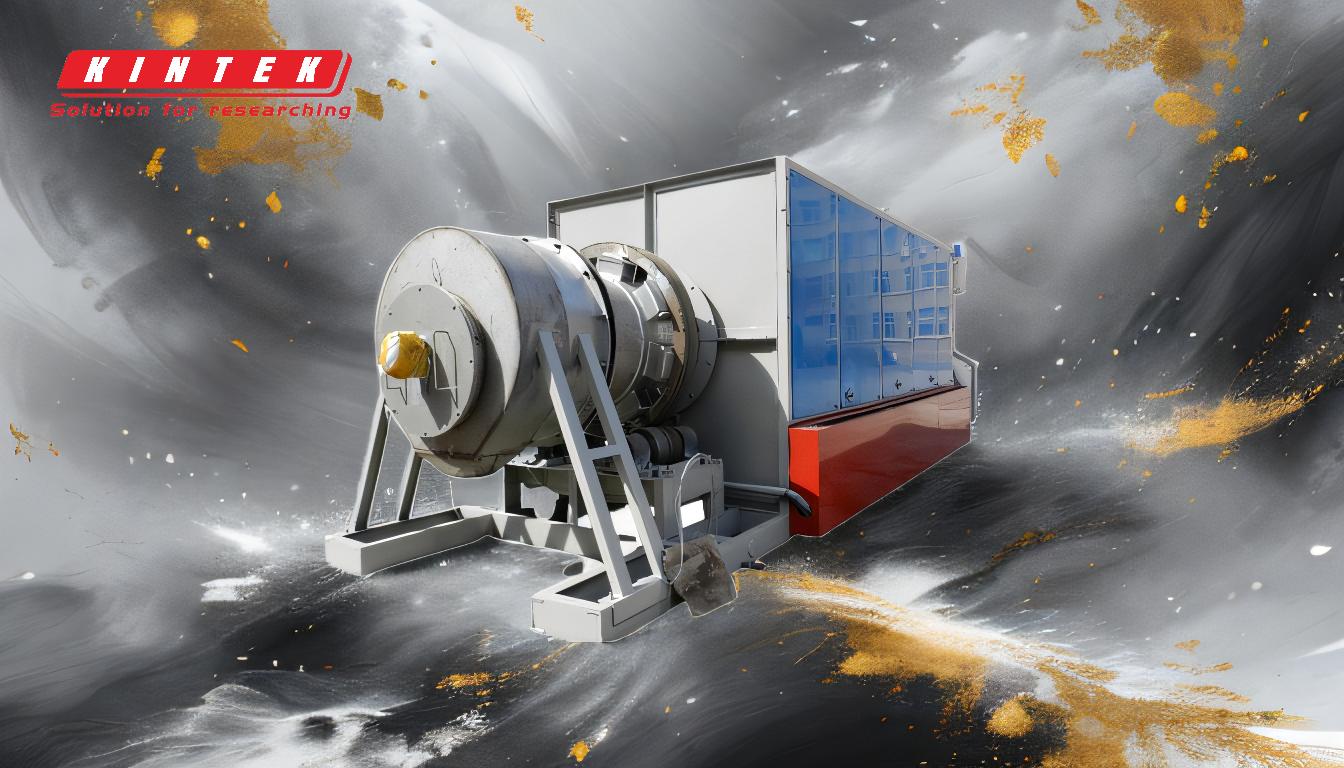
-
Muffle Furnaces:
- Muffle furnaces are widely used for calcination due to their ability to provide uniform heating and isolate the material from combustion gases. They are equipped with heating elements surrounding a chamber, ensuring precise temperature control.
- Applications: Calcination of materials like limestone (to produce lime), ceramics, and catalysts.
- Advantages: High temperature uniformity, isolation from contaminants, and suitability for small-scale laboratory or industrial use.
-
Reverberatory Furnaces:
- Reverberatory furnaces are large, industrial-scale furnaces used for smelting and calcination. They feature a shallow hearth and a roof that reflects heat onto the material, ensuring efficient heat transfer.
- Applications: Smelting of metals like copper and lead, as well as calcination of ores.
- Advantages: High capacity, ability to handle large volumes, and suitability for continuous operation.
-
Shaft Furnaces:
- Shaft furnaces are vertical furnaces used for calcination and smelting. They operate by feeding materials from the top and allowing them to descend through a heated chamber, where they undergo thermal treatment.
- Applications: Calcination of limestone and dolomite, as well as smelting of iron ores in blast furnaces.
- Advantages: Efficient heat utilization, continuous operation, and high throughput.
-
Rotary Kilns:
- Rotary kilns are cylindrical furnaces that rotate to ensure uniform heating of materials. They are commonly used for both calcination and smelting processes.
- Applications: Calcination of cement clinker, alumina, and other industrial minerals, as well as smelting of ores.
- Advantages: High thermal efficiency, ability to handle a wide range of materials, and continuous processing.
-
Electric vs. Fired Process Furnaces:
- Electric process furnaces are used for calcination and smelting in applications where pollution control is critical. They are more expensive but offer precise temperature control and do not produce emissions.
- Fired process furnaces use combusting fuels (e.g., gas or oil) to generate heat and are widely used in industrial settings due to their lower operational costs.
- Applications: Electric furnaces are preferred for high-purity materials, while fired furnaces are used in refineries, petrochemical plants, and metal smelting.
-
Specialized Furnaces for Industrial Applications:
- Rotary Drum Furnaces, Roller Hearth Kilns, Pusher Slab Kilns, and Lift Bottom Kilns are specialized furnaces used for sintering and smelting industrial products.
- Applications: Sintering of ceramics, metals, and other materials, as well as smelting of ores.
- Advantages: High throughput, precise temperature control, and suitability for large-scale industrial operations.
By understanding the specific requirements of calcination and smelting processes, such as temperature range, material volume, and environmental considerations, the appropriate furnace type can be selected to ensure optimal performance and efficiency.
Summary Table:
Furnace Type | Applications | Advantages |
---|---|---|
Muffle Furnaces | Calcination of limestone, ceramics, catalysts | High temperature uniformity, isolation from contaminants, small-scale use |
Reverberatory Furnaces | Smelting of copper, lead; calcination of ores | High capacity, handles large volumes, continuous operation |
Shaft Furnaces | Calcination of limestone, dolomite; smelting of iron ores | Efficient heat utilization, continuous operation, high throughput |
Rotary Kilns | Calcination of cement clinker, alumina; smelting of ores | High thermal efficiency, handles wide material range, continuous processing |
Electric Process Furnaces | High-purity materials, pollution-sensitive applications | Precise temperature control, no emissions |
Fired Process Furnaces | Refineries, petrochemical plants, metal smelting | Lower operational costs, widely used in industrial settings |
Specialized Furnaces | Sintering of ceramics, metals; smelting of ores | High throughput, precise temperature control, large-scale industrial operation |
Need help selecting the right furnace for your calcination or smelting process? Contact our experts today!