Casting furnaces are specialized equipment designed to melt metals for casting processes. The type of furnace used depends on the metal being cast, the scale of production, and specific operational requirements. Common furnaces include crucible furnaces, induction furnaces, cupola furnaces, and reverberatory furnaces, each suited for different applications. For aluminum casting, stationary bale-out or hydraulic tilting crucible furnaces are widely used due to their flexibility and compact design. Larger operations may employ gas-fired or electric resistance wet bath reverberatory melters. In high-pressure die casting, crucible furnaces and low-energy electric or gas-fired holding furnaces are common. For permanent mould casting, gas-fired dry hearth furnaces and electric resistance heated crucible furnaces are preferred, especially for applications requiring high metal quality.
Key Points Explained:
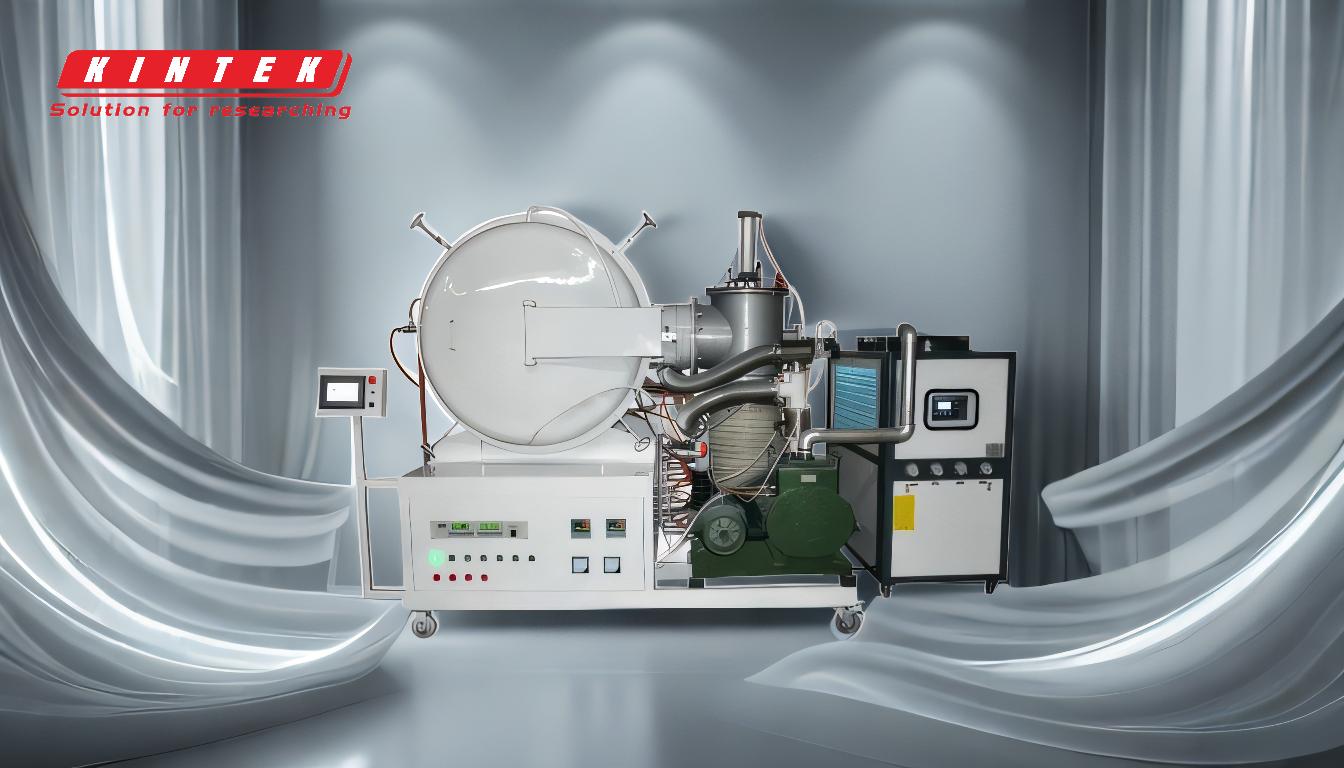
-
Types of Furnaces for Casting:
- Crucible Furnaces: Used for small to medium-sized operations, especially in jobbing shops where frequent alloy changes are required. They are flexible and have a relatively small footprint. Heat sources include natural gas, oil, electric resistance, or electric induction.
- Induction Furnaces: Commonly used in foundries for melting metals. They are efficient and provide precise temperature control, making them suitable for high-quality casting.
- Cupola Furnaces: Traditionally used for iron casting, these furnaces are robust and capable of handling large volumes of metal.
- Reverberatory Furnaces: Used in larger capacity operations, these furnaces are efficient for melting large quantities of metal and are often gas-fired or electric resistance heated.
-
Furnaces for Aluminum Casting:
- Stationary Bale-Out or Hydraulic Tilting Crucible Furnaces: Preferred for their flexibility, necessary for frequent alloy changes and extended shutdowns. They are compact and can be heated by natural gas, oil, electric resistance, or electric induction.
- Gas-Fired or Electric Resistance Wet Bath Reverberatory Melters: Used in larger operations for their efficiency and capacity to handle large volumes of metal.
- Gas-Fired Dry Hearth Furnaces: Suitable for applications requiring high metal quality, such as in permanent mould casting.
- Gas-Fired Stack Melters: Another option for larger capacity operations, providing efficient melting with minimal melt losses.
-
Furnaces for High-Pressure Die Casting:
- Crucible Furnaces: Commonly used in small to medium-sized operations or captive shops. They are versatile and can handle frequent alloy changes.
- Central Reverberatory Melting Furnaces: Used for larger scale operations, providing efficient melting with consistent quality.
- Low-Energy Electric or Gas-Fired Holding Furnaces: Designed to maintain metal at the required temperature with minimal energy consumption.
- Automatic Dosing Furnaces: Provide precise control over the amount of metal being poured, ensuring consistency in casting.
- Electrically Heated Distribution (Launder) Systems: Used to transport molten metal from the furnace to the casting machine, maintaining temperature and quality.
-
Furnaces for Permanent Mould Casting:
- Gas-Fired Dry Hearth Furnaces: Preferred for their efficiency and ability to produce high-quality metal, essential for applications like electric motor rotor casting.
- Electric Resistance Heated Crucible Furnaces: Known for their high energy efficiency (60-65%), superior metal quality, and low melt losses (less than 3%). These are particularly suitable for applications where metal quality is critical.
-
Heat Sources for Casting Furnaces:
- Natural Gas: Commonly used for its efficiency and cost-effectiveness in gas-fired furnaces.
- Oil: An alternative to natural gas, used in some crucible and reverberatory furnaces.
- Electric Resistance: Provides precise temperature control and is used in crucible, reverberatory, and dry hearth furnaces.
- Electric Induction: Offers efficient and rapid heating, suitable for induction furnaces and some crucible furnaces.
-
Operational Considerations:
- Flexibility: Furnaces like crucible and induction furnaces are preferred in jobbing shops due to their ability to handle frequent alloy changes.
- Energy Efficiency: Electric resistance heated furnaces, such as 'globar' aluminum wet bath reverberatory furnaces, are known for their high energy efficiency and low melt losses.
- Metal Quality: Furnaces designed for high metal quality, such as gas-fired dry hearth and electric resistance heated crucible furnaces, are essential for critical applications like electric motor rotor casting.
By understanding the specific requirements of the casting process and the characteristics of different furnaces, manufacturers can select the most appropriate furnace type to ensure efficient, high-quality production.
Summary Table:
Furnace Type | Applications | Key Features |
---|---|---|
Crucible Furnaces | Small to medium operations, frequent alloy changes | Flexible, compact, heated by gas, oil, or electric resistance/induction |
Induction Furnaces | Foundries, high-quality casting | Efficient, precise temperature control |
Cupola Furnaces | Iron casting, large volumes | Robust, high capacity |
Reverberatory Furnaces | Large capacity operations | Efficient for melting large quantities, gas-fired or electric resistance heated |
Aluminum Casting | Stationary bale-out, hydraulic tilting crucible, wet bath reverberatory melters | Flexible, compact, high metal quality |
High-Pressure Die Casting | Crucible, low-energy holding, automatic dosing furnaces | Versatile, energy-efficient, precise metal control |
Permanent Mould Casting | Gas-fired dry hearth, electric resistance heated crucible furnaces | High energy efficiency, superior metal quality |
Need help selecting the right casting furnace for your operations? Contact our experts today for personalized advice!