Sintering is a manufacturing process that combines small particles into a solid mass without melting the materials, using heat and pressure. This process is widely used in industries such as powder metallurgy, ceramics, and plastics to create durable, high-strength components. By applying heat below the material's melting point, sintering allows atoms to diffuse across particle boundaries, fusing them into a cohesive structure. This method is particularly useful for materials with high melting points, such as tungsten and molybdenum, and is essential for producing complex shapes and high-performance parts.
Key Points Explained:
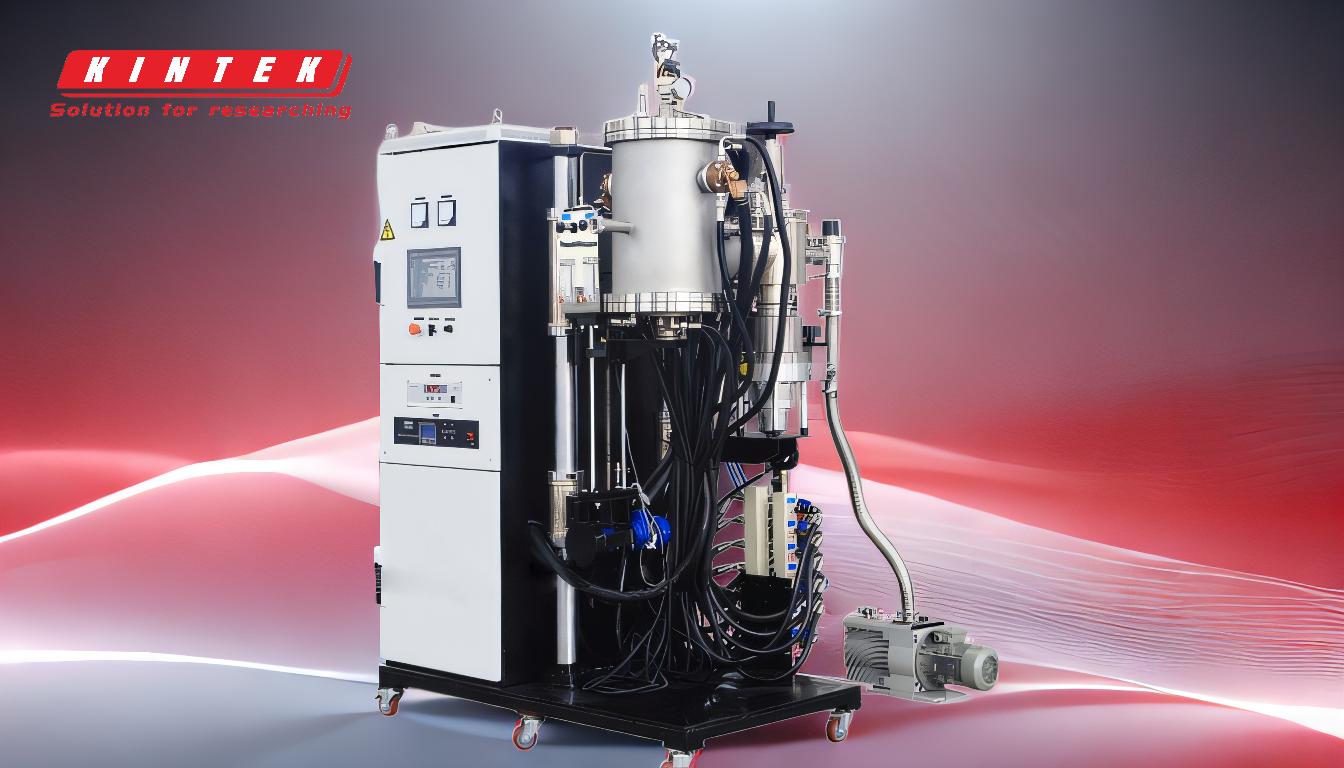
-
Definition of Sintering:
- Sintering is a process that transforms powdery materials into dense, solid bodies by applying heat and pressure without reaching the material's melting point. This allows particles to bond at the atomic level, creating a durable and cohesive structure.
-
Materials Suitable for Sintering:
- Sintering is applicable to a wide range of materials, including:
- Metals: Commonly used in powder metallurgy for metals like tungsten, molybdenum, and steel.
- Ceramics: Essential for creating pottery, tiles, and advanced ceramic components.
- Plastics: Used to produce high-strength plastic parts with complex geometries.
- Other Materials: Includes composites and advanced materials for specialized applications.
- Sintering is applicable to a wide range of materials, including:
-
Key Steps in the Sintering Process:
- The sintering process involves several critical steps:
- Powder Preparation: Raw materials are ground into fine powders.
- Compaction: Powders are pressed into a desired shape using molds and pressure.
- Heating: The compacted material is heated below its melting point, allowing atomic diffusion and particle bonding.
- Cooling: The sintered part is cooled slowly to ensure structural integrity.
- The sintering process involves several critical steps:
-
Advantages of Sintering:
- Sintering offers numerous benefits, including:
- High Strength and Durability: The process creates dense, strong materials with excellent mechanical properties.
- Complex Shapes: Sintering allows for the production of intricate and precise components.
- Cost-Effectiveness: It reduces material waste and energy consumption compared to melting processes.
- Versatility: Suitable for a wide range of materials and applications.
- Sintering offers numerous benefits, including:
-
Applications of Sintering:
- Sintering is widely used in various industries, such as:
- Powder Metallurgy: For manufacturing gears, bearings, and automotive components.
- Ceramics: In the production of tiles, pottery, and advanced ceramic tools.
- Plastics: For creating high-performance plastic parts in electronics and consumer goods.
- Advanced Materials: In aerospace, medical devices, and energy sectors for specialized components.
- Sintering is widely used in various industries, such as:
-
Types of Sintering:
- There are different types of sintering processes, including:
- Solid-State Sintering: Involves heating materials below their melting point, relying on atomic diffusion.
- Liquid-Phase Sintering: Uses a small amount of liquid to enhance particle bonding.
- Pressure-Assisted Sintering: Combines heat and pressure to achieve denser structures.
- Spark Plasma Sintering (SPS): A rapid sintering method using electrical current for faster results.
- There are different types of sintering processes, including:
-
Challenges and Considerations:
- While sintering is highly effective, it also presents some challenges:
- Material Selection: Not all materials are suitable for sintering due to their thermal properties.
- Process Control: Precise control of temperature, pressure, and time is crucial for consistent results.
- Porosity: Some sintered materials may retain porosity, affecting their mechanical properties.
- While sintering is highly effective, it also presents some challenges:
-
Future Trends in Sintering:
- Advancements in sintering technology focus on:
- Additive Manufacturing: Combining sintering with 3D printing for complex geometries.
- Nanomaterials: Using sintering to produce nano-structured materials with enhanced properties.
- Sustainability: Developing eco-friendly sintering processes with reduced energy consumption.
- Advancements in sintering technology focus on:
By understanding these key points, equipment and consumable purchasers can make informed decisions about the suitability of sintering for their specific applications and materials.
Summary Table:
Aspect | Details |
---|---|
Definition | Combines particles into a solid mass using heat and pressure without melting. |
Materials | Metals (tungsten, molybdenum), ceramics, plastics, composites. |
Key Steps | Powder preparation, compaction, heating, cooling. |
Advantages | High strength, complex shapes, cost-effectiveness, versatility. |
Applications | Powder metallurgy, ceramics, plastics, aerospace, medical devices. |
Types | Solid-state, liquid-phase, pressure-assisted, spark plasma sintering (SPS). |
Challenges | Material selection, process control, porosity. |
Future Trends | Additive manufacturing, nanomaterials, sustainability. |
Discover how sintering can enhance your manufacturing process—contact our experts today!