Sintering furnaces are essential for producing advanced ceramics, as they facilitate the bonding and densification of ceramic particles at high temperatures. This process enhances the material's properties and influences the efficiency and environmental impact of manufacturing. When selecting a furnace, factors such as firing cycles, material properties, throughput, fuel type, and ancillary equipment must be considered. Modern sintering furnaces are programmable, offering flexibility in temperature control and profile settings, which is crucial for achieving consistent results. The most common types of furnaces used in laboratories and industrial settings include tube furnaces, box furnaces, and muffle furnaces, each suited to specific applications.
Key Points Explained:
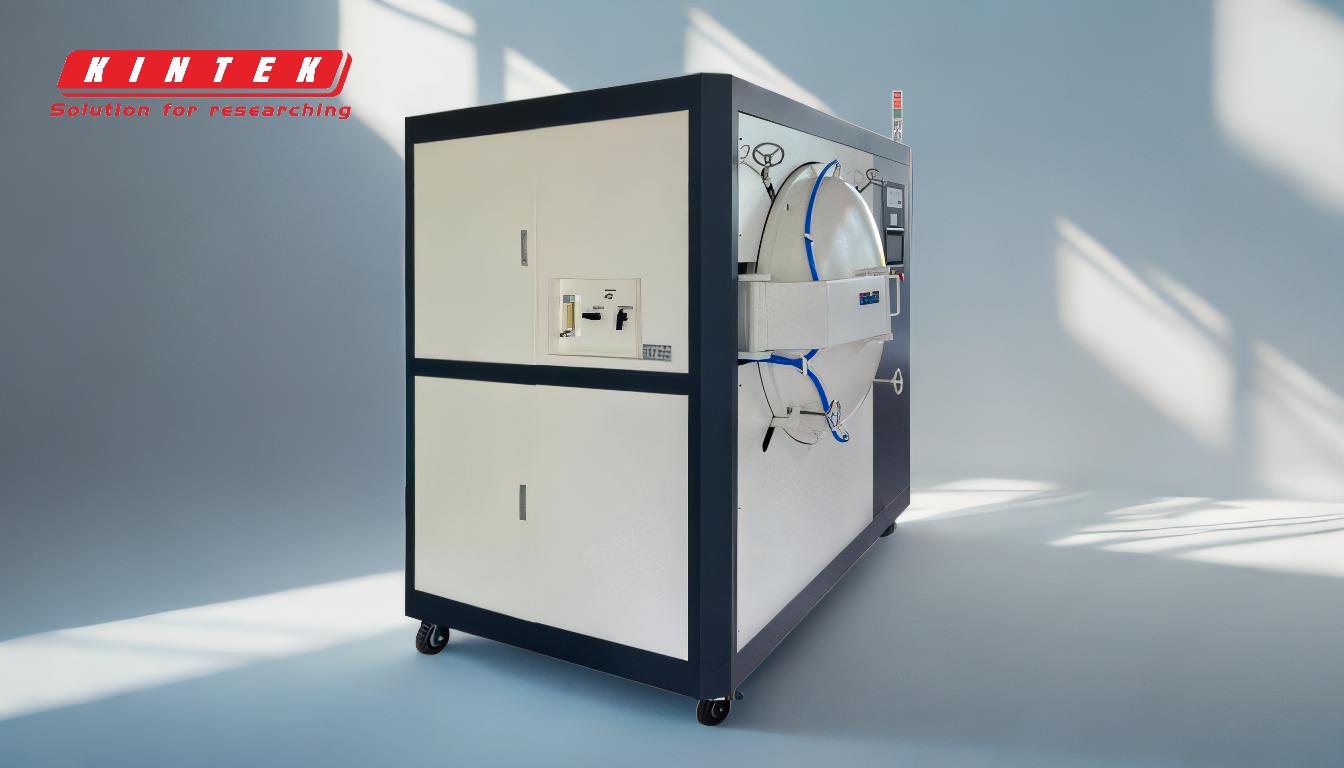
-
Role of Sintering Furnaces in Ceramics Production
- Sintering furnaces are critical for transforming ceramic green bodies into dense, high-performance materials.
- They operate at high temperatures, promoting particle bonding and densification without melting the material.
- This process directly impacts the structural integrity, performance, and environmental sustainability of the final product.
-
Factors Influencing Furnace Selection
- Firing Cycle: The heating and cooling rates must align with the ceramic material's requirements.
- Material Properties: The mass and specific heat of the ceramic determine the energy needed for sintering.
- Throughput: The desired production volume influences the furnace size and capacity.
- Fuel Type: The choice of fuel (electric, gas, etc.) affects operational costs and environmental impact.
- Ancillary Equipment: Features like process gas systems and automated loading doors enhance efficiency and precision.
-
Types of Sintering Furnaces
- Tube Furnaces: Ideal for small-scale or laboratory applications, offering uniform heating in a cylindrical chamber.
- Box Furnaces: Suitable for larger batches, providing consistent temperature distribution in a rectangular chamber.
- Muffle Furnaces: Designed to isolate materials from combustion gases, ensuring a clean sintering environment.
-
Modern Furnace Capabilities
- Programmable settings allow precise control over ramp rates, final temperatures, hold times, and cooling rates.
- Built-in memory stores multiple sintering profiles, enabling quick setup for specific production runs.
- Advanced features like real-time monitoring and automation improve process reliability and repeatability.
-
Applications Beyond Ceramics
- Sintering furnaces are also used in chemical vapor deposition and infiltration processes, expanding their utility in scientific research and industrial production.
- While the focus here is on ceramics, the principles of sintering apply to other materials, such as metals and composites.
By understanding these key points, equipment and consumable purchasers can make informed decisions when selecting sintering furnaces for ceramic production, ensuring optimal performance and cost-effectiveness.
Summary Table:
Furnace Type | Key Features | Applications |
---|---|---|
Tube Furnace | Uniform heating, cylindrical chamber | Small-scale or lab use |
Box Furnace | Consistent temperature, rectangular chamber | Larger batches |
Muffle Furnace | Isolates materials from combustion gases | Clean sintering environment |
Ready to find the perfect sintering furnace for your ceramics production? Contact our experts today for personalized advice!