Melting and smelting are two distinct processes involving heat and materials, but they serve different purposes and operate under different conditions. Melting is a phase change process where a solid material is heated to its melting point, turning it into a liquid. This process is often used in metalworking, glassmaking, and other industries where a liquid state is required for further processing. Smelting, on the other hand, is a metallurgical process used to extract pure metal from its ore by heating it to high temperatures, often in the presence of a reducing agent like carbon. While both processes involve heating, their goals, methods, and outcomes differ significantly.
Key Points Explained:
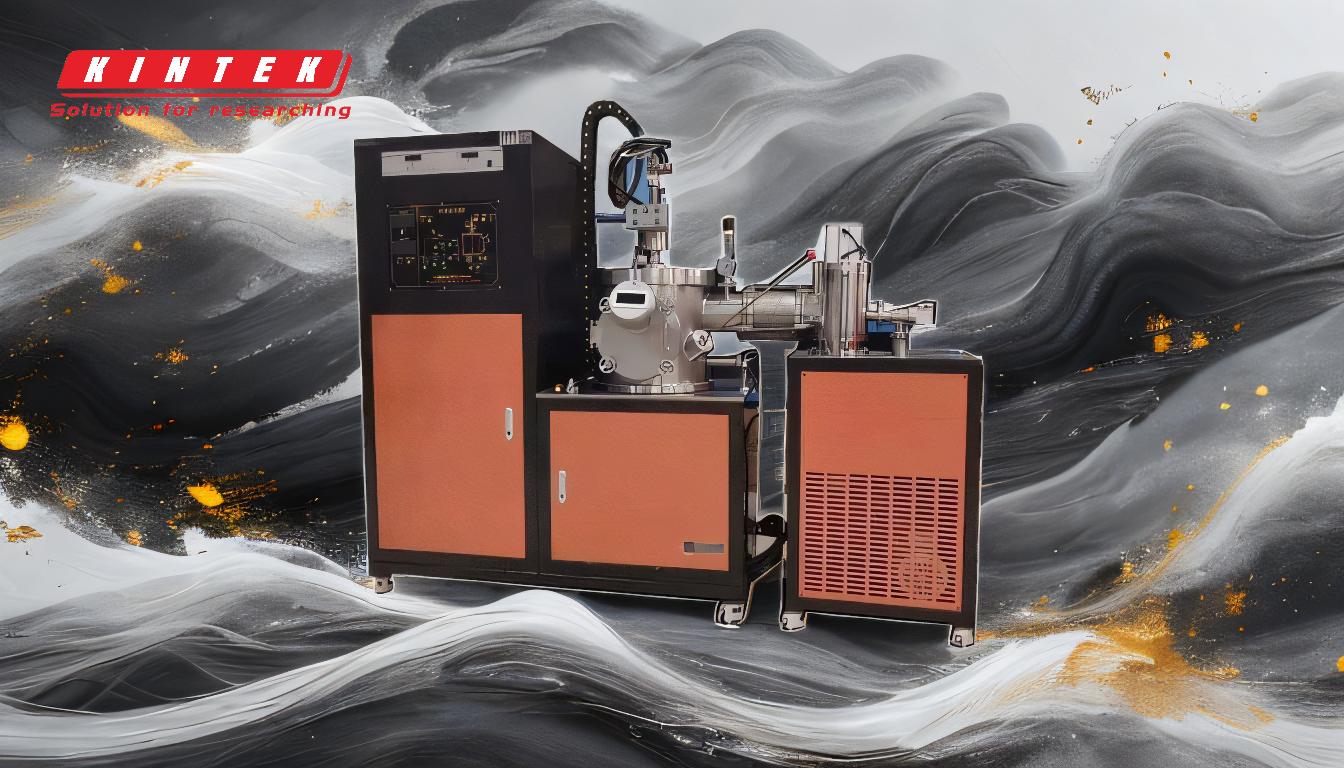
-
Definition and Purpose:
- Melting: This is a physical process where a solid material is heated to its melting point, causing it to transition from a solid to a liquid state. The primary purpose of melting is to change the physical state of a material for further processing, such as casting, molding, or alloying.
- Smelting: This is a chemical process used to extract pure metal from its ore. It involves heating the ore to high temperatures, often in the presence of a reducing agent, to separate the metal from impurities. The goal is to produce a pure metal that can be used in manufacturing or other applications.
-
Temperature Requirements:
- Melting: The temperature required for melting is specific to the material being melted. For example, aluminum melts at around 660°C, while iron melts at approximately 1538°C. The process relies solely on thermal energy to achieve the phase change.
- Smelting: Smelting typically requires much higher temperatures than melting, as it involves breaking down the chemical bonds in the ore to extract the metal. The exact temperature depends on the type of ore and the metal being extracted. For example, iron ore smelting can require temperatures up to 2000°C.
-
Process and Mechanism:
- Melting: This process is relatively straightforward, involving the application of heat to a solid material until it reaches its melting point and transitions to a liquid state. No chemical changes occur during melting; it is purely a physical transformation.
- Smelting: Smelting is more complex and involves chemical reactions. The ore is heated in the presence of a reducing agent (like coke or charcoal) to remove oxygen and other impurities, resulting in the production of pure metal. This process often involves multiple steps, including roasting, reduction, and refining.
-
Energy Consumption:
- Melting: While melting does require significant energy, especially for metals with high melting points, it is generally less energy-intensive than smelting. The energy is primarily used to overcome the intermolecular forces holding the solid together.
- Smelting: Smelting is highly energy-intensive due to the high temperatures required and the chemical reactions involved. The process often consumes large amounts of fuel and electricity, making it more costly and environmentally impactful than melting.
-
Applications:
- Melting: Melting is widely used in industries such as metalworking, glassmaking, and plastics manufacturing. It is essential for processes like casting, where molten metal is poured into molds to create specific shapes.
- Smelting: Smelting is primarily used in the metallurgical industry to extract metals from their ores. It is a critical step in the production of metals like iron, copper, and aluminum, which are used in construction, electronics, and transportation.
-
Outcomes:
- Melting: The outcome of melting is a liquid material that can be shaped, molded, or alloyed with other materials. The process does not alter the chemical composition of the material; it only changes its physical state.
- Smelting: The outcome of smelting is a pure metal, free from impurities and ready for further processing or use. The process involves significant chemical changes, resulting in a material with different properties than the original ore.
In summary, while both melting and smelting involve the application of heat to materials, they are fundamentally different processes with distinct goals, methods, and outcomes. Melting is a physical process used to change the state of a material, while smelting is a chemical process used to extract pure metal from its ore. Understanding these differences is crucial for selecting the appropriate process for a given application in industries ranging from manufacturing to metallurgy.
Summary Table:
Aspect | Melting | Smelting |
---|---|---|
Definition | Physical process of turning solid into liquid | Chemical process of extracting pure metal from ore |
Purpose | Change physical state for further processing (e.g., casting, molding) | Extract pure metal from ore for manufacturing |
Temperature | Specific to material (e.g., aluminum: 660°C, iron: 1538°C) | Higher temperatures (e.g., iron ore smelting: up to 2000°C) |
Process | Heat solid to melting point; no chemical changes | Heat ore with reducing agent; involves chemical reactions |
Energy Consumption | Less energy-intensive | Highly energy-intensive |
Applications | Metalworking, glassmaking, plastics manufacturing | Metallurgical industry (e.g., iron, copper, aluminum production) |
Outcome | Liquid material for shaping or alloying | Pure metal free from impurities |
Need help understanding which process suits your needs? Contact our experts today for personalized advice!