Magnetron sputtering was invented in 1974 by Chapin, marking a significant advancement in thin-film deposition technology. This innovation addressed the limitations of earlier diode sputtering, such as low deposition rates and high costs, by introducing a more efficient and cost-effective method. Magnetron sputtering quickly became a cornerstone in various industries due to its higher deposition rates and improved performance. The technology has since evolved, with advancements in reactive DC sputtering, pulsed sputtering, and high ionization techniques, solidifying its importance in modern manufacturing and research.
Key Points Explained:
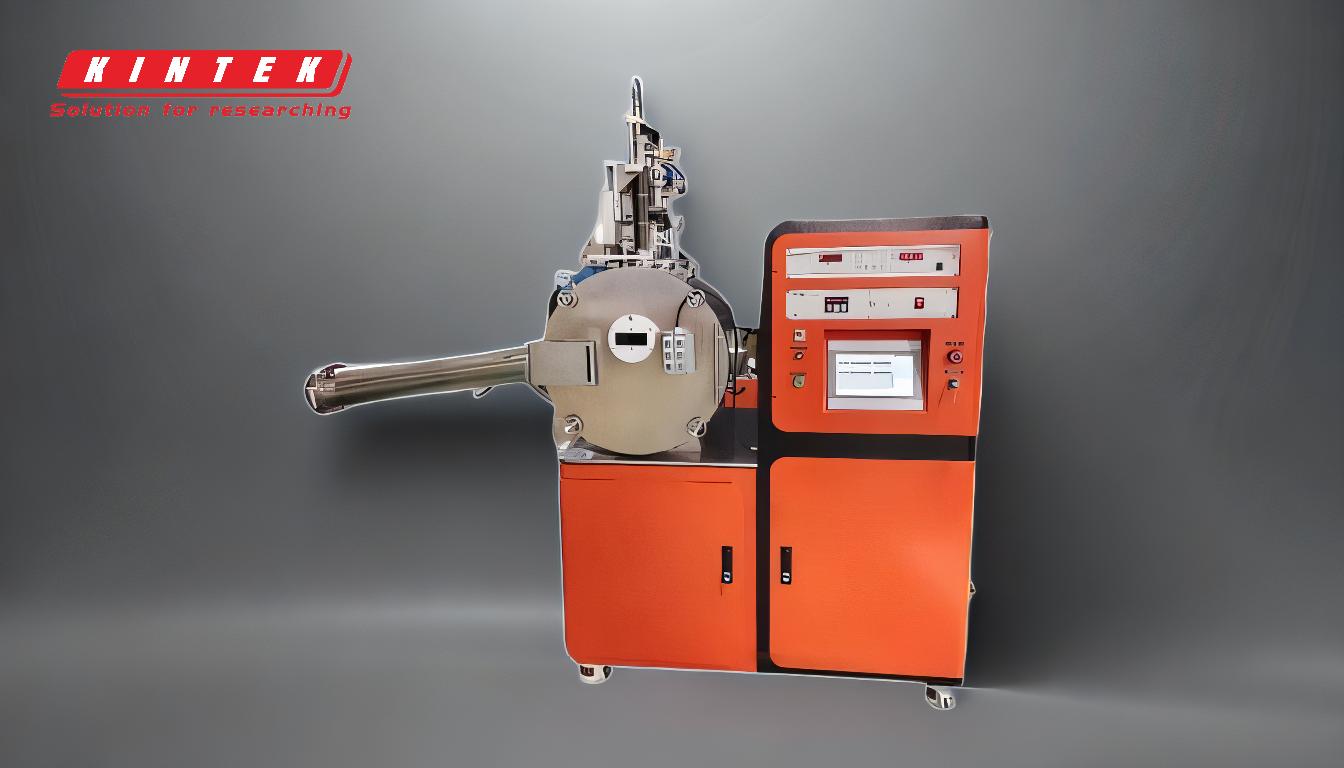
-
Invention of Magnetron Sputtering:
- Magnetron sputtering was invented in 1974 by Chapin.
- This invention was a direct response to the limitations of diode sputtering, which had been in commercial use since the 1940s but suffered from low deposition rates and high operational costs.
- The introduction of magnetron sputtering revolutionized thin-film deposition by providing a more efficient and cost-effective alternative.
-
Historical Context of Sputtering:
- The phenomenon of sputtering was first observed in the 1850s, but it remained a scientific curiosity until the 1940s when diode sputtering became commercially viable.
- Diode sputtering, while groundbreaking at the time, had significant drawbacks, including low deposition rates and high costs, which limited its widespread adoption.
-
Advantages of Magnetron Sputtering:
- Higher Deposition Rates: Magnetron sputtering significantly increased the rate at which thin films could be deposited, making it more suitable for industrial applications.
- Cost Efficiency: The technology reduced operational costs, making it more accessible for a wider range of applications.
- Improved Performance: Magnetron sputtering offered better control over the deposition process, resulting in higher-quality thin films.
-
Technological Evolution:
- 1980s: The decade saw the rise of reactive DC sputtering, which further enhanced the capabilities of magnetron sputtering.
- 1990s: Focus shifted to pulsed sputtering and improving target utilization, making the process even more efficient.
- 2000s: Advances in high ionization techniques pushed the boundaries of what could be achieved with magnetron sputtering, leading to new applications and improved performance.
-
Impact on Industry:
- The invention of magnetron sputtering had a profound impact on various industries, including electronics, optics, and materials science.
- Its ability to produce high-quality thin films at a lower cost and higher rate made it an essential tool in modern manufacturing and research.
In summary, magnetron sputtering was invented in 1974, addressing the limitations of earlier sputtering methods and revolutionizing thin-film deposition. Its advantages in terms of deposition rates, cost efficiency, and performance have made it a cornerstone technology in various industries, with continuous advancements further enhancing its capabilities.
Summary Table:
Key Aspect | Details |
---|---|
Invention Year | 1974 |
Inventor | Chapin |
Predecessor Technology | Diode Sputtering (1940s) |
Key Advantages | Higher deposition rates, cost efficiency, improved performance |
Technological Evolution | Reactive DC sputtering (1980s), pulsed sputtering (1990s), high ionization (2000s) |
Impact on Industries | Electronics, optics, materials science |
Learn how magnetron sputtering can enhance your manufacturing process—contact us today!