Vacuum casting is a versatile manufacturing process widely used across various industries for producing high-quality, detailed, and functional prototypes or small-batch production parts. It is particularly valued for its ability to replicate intricate designs and produce parts with excellent surface finishes and material properties. The process is commonly used in industries such as automotive, aerospace, medical devices, consumer electronics, and jewelry, where precision and material fidelity are critical. Additionally, vacuum casting is employed in the creation of silicone molds for low-volume production, enabling cost-effective manufacturing of complex parts without the need for expensive tooling.
Key Points Explained:
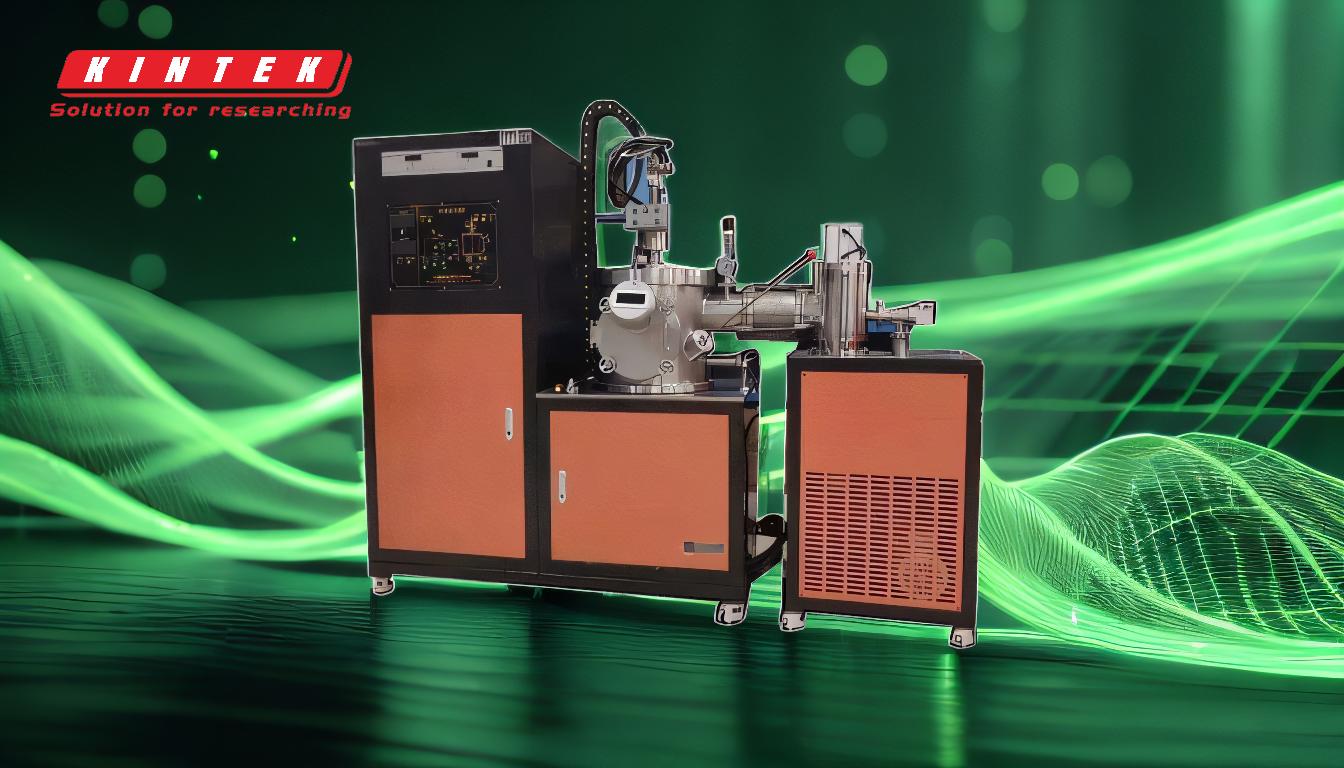
-
Automotive Industry
- Application: Vacuum casting is used to create prototypes of automotive components such as dashboards, interior trims, and functional parts like air ducts or housings.
- Why It’s Used: The process allows for the production of parts with high dimensional accuracy and material properties that closely mimic the final product. This is crucial for testing and validation before mass production.
- Example: Prototyping lightweight components for electric vehicles to test aerodynamics and durability.
-
Aerospace Industry
- Application: Vacuum casting is employed to produce prototypes of aerospace components, including housings, brackets, and interior panels.
- Why It’s Used: The aerospace industry demands high precision and material performance. Vacuum casting can replicate complex geometries and use advanced materials that meet stringent industry standards.
- Example: Creating prototypes of engine components to test thermal and mechanical performance.
-
Medical Devices
- Application: The process is used to manufacture prototypes and small batches of medical devices, such as surgical instruments, implants, and diagnostic equipment.
- Why It’s Used: Medical devices require biocompatible materials and precise replication of intricate designs. Vacuum casting ensures high fidelity and material compatibility.
- Example: Prototyping custom orthopedic implants for patient-specific applications.
-
Consumer Electronics
- Application: Vacuum casting is utilized to produce casings, buttons, and other components for consumer electronics like smartphones, wearables, and home appliances.
- Why It’s Used: The process allows for the creation of parts with excellent surface finishes and functional properties, which are essential for user experience and product testing.
- Example: Developing prototypes of ergonomic smartphone cases for usability testing.
-
Jewelry and Fashion
- Application: Vacuum casting is used to create intricate jewelry designs, accessories, and fashion components.
- Why It’s Used: The process excels at replicating fine details and producing high-quality finishes, making it ideal for custom or limited-edition pieces.
- Example: Crafting detailed pendants or rings with complex patterns.
-
Low-Volume Production
- Application: Vacuum casting is employed for small-batch production of parts when traditional methods like injection molding are not cost-effective.
- Why It’s Used: It eliminates the need for expensive tooling and allows for flexibility in material selection and design changes.
- Example: Producing limited runs of custom-designed products for niche markets.
-
Silicone Mold Creation
- Application: Vacuum casting is used to create silicone molds for replicating parts in low-volume production.
- Why It’s Used: Silicone molds are durable and can produce multiple copies of a part with consistent quality, making them ideal for prototyping and small-scale manufacturing.
- Example: Creating molds for producing decorative items or functional prototypes.
-
Material Versatility
- Application: Vacuum casting supports a wide range of materials, including polyurethanes, resins, and elastomers, which can mimic the properties of engineering plastics, rubber, and metals.
- Why It’s Used: This versatility allows manufacturers to test different materials for specific applications without committing to expensive tooling.
- Example: Testing polyurethane parts to simulate the performance of ABS plastic in automotive components.
-
Rapid Prototyping
- Application: Vacuum casting is a key technique in rapid prototyping, enabling quick turnaround times for functional prototypes.
- Why It’s Used: It bridges the gap between 3D printing and mass production, providing high-quality prototypes for design validation and testing.
- Example: Producing functional prototypes of a new product design within weeks for market testing.
-
Cost-Effectiveness for Small Batches
- Application: Vacuum casting is ideal for producing small batches of parts without the high upfront costs associated with traditional manufacturing methods.
- Why It’s Used: It reduces the financial risk for startups and small businesses by allowing them to test and refine designs before scaling up production.
- Example: Manufacturing limited-edition consumer products to gauge market interest.
By leveraging vacuum casting, industries can achieve a balance between cost, quality, and speed, making it an indispensable tool for prototyping and small-scale production across diverse applications.
Summary Table:
Industry | Applications | Key Benefits |
---|---|---|
Automotive | Prototypes of dashboards, interior trims, air ducts | High dimensional accuracy, material properties mimicking final products |
Aerospace | Housings, brackets, interior panels | Precision, advanced materials for complex geometries |
Medical Devices | Surgical instruments, implants, diagnostic equipment | Biocompatible materials, intricate design replication |
Consumer Electronics | Casings, buttons, smartphone components | Excellent surface finishes, functional properties for user experience |
Jewelry & Fashion | Intricate jewelry designs, accessories | Fine detail replication, high-quality finishes for custom pieces |
Low-Volume Production | Small-batch parts without expensive tooling | Cost-effective, flexible material selection |
Silicone Mold Creation | Durable molds for low-volume production | Consistent quality, ideal for prototyping and small-scale manufacturing |
Material Versatility | Polyurethanes, resins, elastomers | Mimics engineering plastics, rubber, and metals for testing |
Rapid Prototyping | Quick turnaround for functional prototypes | Bridges 3D printing and mass production, high-quality prototypes |
Cost-Effectiveness | Small batches for startups and niche markets | Reduces financial risk, allows design refinement before scaling |
Discover how vacuum casting can transform your prototyping and production process—contact us today to learn more!