When it comes to melting non-ferrous metals, the most suitable furnace type is the induction furnace, specifically the coreless induction furnace. This type of furnace is highly efficient, versatile, and capable of melting a wide range of non-ferrous metals, including aluminum, copper, zinc, and their alloys. Induction furnaces are preferred due to their precise temperature control, energy efficiency, and ability to handle frequent alloy changes. They are widely used in foundries for applications requiring high-quality metal melting with minimal melt loss. For smaller operations, crucible furnaces (electric resistance or gas-fired) are also commonly used due to their flexibility and relatively small footprint.
Key Points Explained:
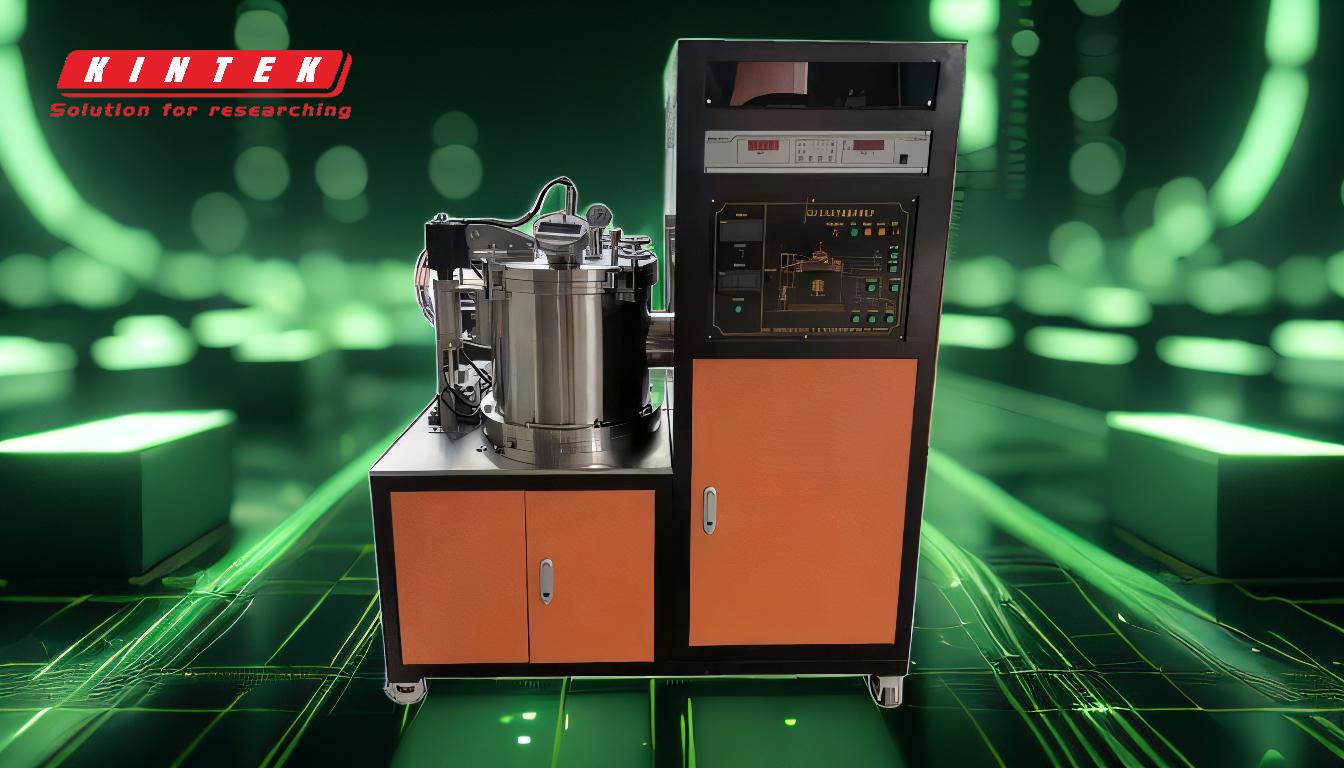
-
Induction Furnaces: The Best Choice for Non-Ferrous Metals
- Induction furnaces, particularly coreless induction furnaces, are the most commonly used for melting non-ferrous metals. They use electromagnetic induction to generate heat, which allows for precise temperature control and uniform heating.
- These furnaces are highly efficient, with energy efficiencies ranging from 60-65%, and are capable of producing high-quality metal with minimal melt losses (less than 3%).
- Induction furnaces are versatile and can handle frequent alloy changes, making them ideal for foundries that work with multiple non-ferrous metals.
-
Types of Induction Furnaces
- Coreless Induction Furnaces: These are the most widely used for non-ferrous metals. They are available in various sizes and capacities, making them suitable for both small and large-scale operations.
- Channel Induction Furnaces: These are typically used for holding and superheating molten metal rather than melting. They are less common for non-ferrous melting but are efficient for maintaining molten metal at a consistent temperature.
- Crucible Induction Furnaces: These are smaller and more flexible, often used in smaller foundries or for specialized applications.
-
Crucible Furnaces: A Flexible Alternative
- Crucible furnaces, whether electric resistance or gas-fired, are another popular choice for melting non-ferrous metals, especially in smaller operations.
- They are preferred for their flexibility, small footprint, and ease of use. These furnaces are ideal for foundries that require frequent alloy changes or extended shutdowns.
- Heat sources for crucible furnaces can include natural gas, oil, electric resistance, or electric induction.
-
Other Furnace Types for Non-Ferrous Metals
- Reverberatory Furnaces: These are used for larger capacity operations. They are typically gas-fired and can handle significant volumes of non-ferrous metals.
- Dry Hearth Furnaces: These are gas-fired and are commonly used in permanent mould casting for non-ferrous metals. They are efficient and provide high-quality metal output.
- Stack Melters: These are another option for large-scale operations, particularly for aluminum melting.
-
Advantages of Induction Furnaces for Non-Ferrous Metals
- Energy Efficiency: Induction furnaces are highly energy-efficient, with efficiencies often exceeding 60%.
- Precise Temperature Control: The electromagnetic induction process allows for precise control over the melting temperature, which is crucial for maintaining metal quality.
- Minimal Melt Loss: Induction furnaces typically have melt losses of less than 3%, making them cost-effective and environmentally friendly.
- Versatility: They can handle a wide range of non-ferrous metals and alloys, making them suitable for diverse applications.
-
Applications in Foundries
- Induction furnaces are widely used in foundries for melting aluminum, copper, zinc, and their alloys. They are particularly favored in industries where metal quality is critical, such as electric motor rotor casting.
- For smaller foundries or specialized applications, crucible furnaces are often used due to their flexibility and ease of operation.
-
Comparison with Other Furnace Types
- Electric Arc Furnaces: These are primarily used for melting ferrous metals like steel and are less suitable for non-ferrous metals due to their high operating temperatures and potential for contamination.
- Cupola Furnaces: These are traditionally used for melting iron and are not suitable for non-ferrous metals due to their design and operating characteristics.
In summary, induction furnaces, particularly coreless induction furnaces, are the best choice for melting most non-ferrous metals. They offer unmatched efficiency, precision, and versatility, making them the preferred option for foundries and industries that require high-quality metal melting. For smaller operations or specialized needs, crucible furnaces are also a viable alternative.
Summary Table:
Furnace Type | Key Features | Best For |
---|---|---|
Coreless Induction | Precise temperature control, energy efficiency (60-65%), minimal melt loss (<3%) | Large and small-scale operations, frequent alloy changes |
Crucible Furnaces | Flexible, small footprint, easy to use | Smaller operations, specialized applications |
Reverberatory Furnaces | High capacity, gas-fired | Large-scale operations |
Dry Hearth Furnaces | Efficient, high-quality output | Permanent mould casting |
Stack Melters | Large-scale, gas-fired | Aluminum melting |
Ready to optimize your metal melting process? Contact our experts today to find the perfect furnace for your needs!