Sintering is a critical process in materials science, particularly for ceramics like zirconia, where it transforms a porous material into a dense, hard structure. The zirconia sintering furnace is specifically designed for this purpose, offering precision, efficiency, and advanced features to ensure optimal results. It is widely used in dental laboratories to process zirconia into crowns, bridges, and other restorations. Key features include fast sintering programs, high-purity heating elements, precise temperature control, and environmental-friendly insulation materials. These furnaces not only enhance the quality of the final product but also improve the overall workflow in dental labs.
Key Points Explained:
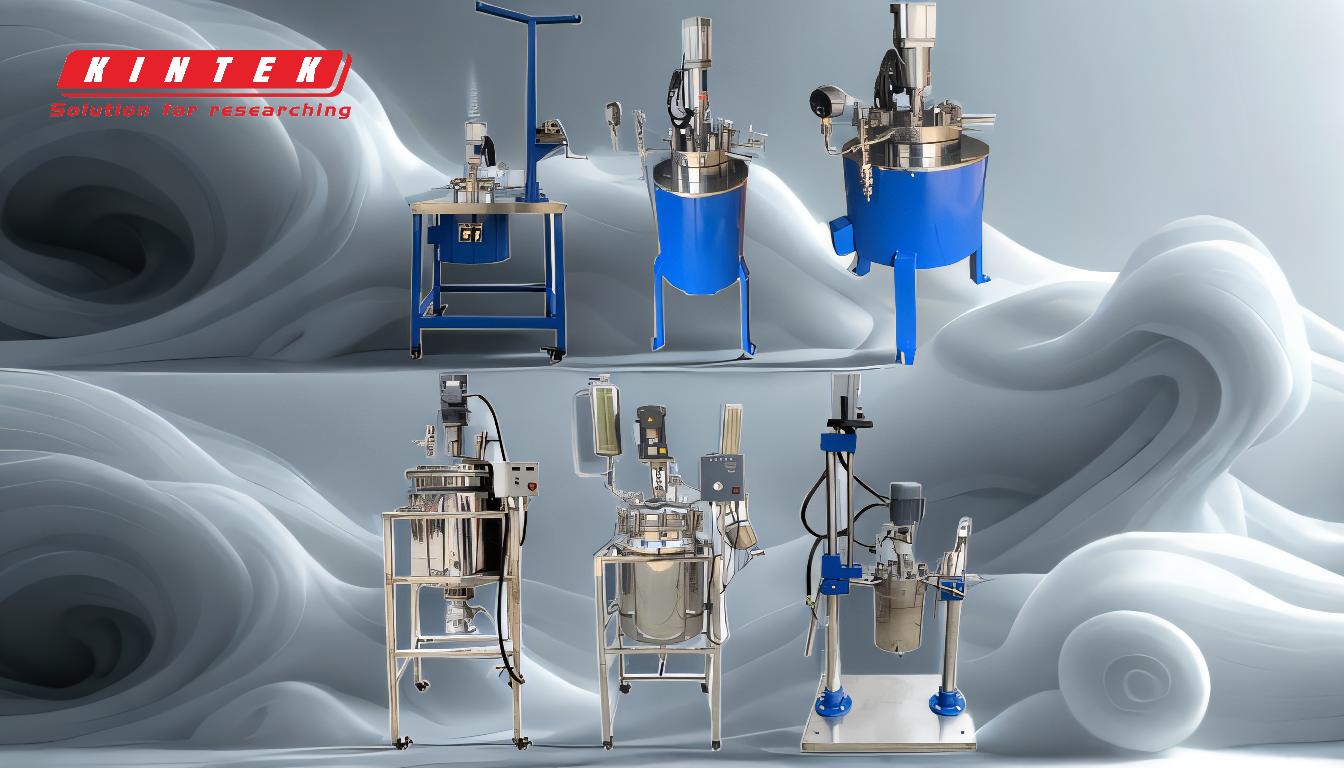
-
Purpose of Sintering Furnaces:
- Sintering is essential for reducing porosity and increasing the density of materials like zirconia, achieving its final hardness and strength.
- Dental sintering furnaces are specifically designed to process zirconia after it has been milled into crowns, bridges, or other dental restorations.
- The process ensures the material reaches its desired mechanical properties and aesthetic finish.
-
Key Features of Zirconia Sintering Furnaces:
- Fast Sintering Programs: Some furnaces, like the zirconia sintering furnace, offer rapid sintering cycles, completing the process in as little as 65 minutes, including heating, keeping warm, and cooling.
- High-Purity Heating Elements: These furnaces use dental silicon molybdenum rods, which are pollution-free and ensure even heat distribution.
- Precise Temperature Control: Equipped with PID intelligent temperature control systems, they maintain an accuracy of ±1℃, critical for consistent results.
- User-Friendly Interface: A 7-inch color touch screen allows easy monitoring and modification of parameters, and the furnace can store up to 40 programs.
- Environmental-Friendly Insulation: Green thermal insulation materials ensure stable temperatures and energy efficiency.
- Power Interruption Recovery: A memory function enables the furnace to resume operations from the point of interruption, ensuring no loss of progress.
-
Applications in Dental Laboratories:
- Zirconia sintering furnaces are indispensable in dental labs for processing zirconia restorations. They ensure precision and efficiency, enhancing the quality of crowns, bridges, and frameworks.
- By maintaining optimal oxygen levels and achieving the desired color and surface finish, these furnaces improve the aesthetic and functional properties of dental restorations.
-
Advantages of Using Zirconia Sintering Furnaces:
- Improved Quality: The precise temperature control and advanced heating elements ensure uniform sintering, resulting in high-quality restorations.
- Efficiency: Fast sintering programs and the ability to stack multiple crucibles (up to 150 units in some models) increase productivity.
- Reliability: Features like power interruption recovery and durable construction make these furnaces a long-term investment for dental labs.
-
Comparison of Sintering Behavior:
- Evaluating the sintering behavior of presintered zirconia blocks helps determine their suitability for clinical use. This involves assessing linear sintering shrinkage and mechanical properties to ensure compatibility with accepted materials.
In summary, the zirconia sintering furnace is a specialized tool designed to meet the demanding requirements of sintering zirconia. Its advanced features, precision, and efficiency make it an essential piece of equipment in dental laboratories, ensuring high-quality restorations and streamlined workflows.
Summary Table:
Feature | Description |
---|---|
Fast Sintering Programs | Completes sintering in as little as 65 minutes, including heating and cooling. |
High-Purity Heating Elements | Dental silicon molybdenum rods ensure pollution-free, even heat distribution. |
Precise Temperature Control | PID systems maintain accuracy within ±1℃ for consistent results. |
User-Friendly Interface | 7-inch color touch screen for easy monitoring and program storage (up to 40). |
Environmental-Friendly Insulation | Green thermal materials ensure energy efficiency and stable temperatures. |
Power Interruption Recovery | Memory function resumes operations from the point of interruption. |
Upgrade your dental lab with a zirconia sintering furnace—contact us today to learn more!