When comparing induction furnaces and electric arc furnaces, the choice depends on the specific requirements of the application, such as the type of material being melted, the desired quality of the final product, environmental considerations, and operational efficiency. Induction furnaces are generally preferred for their energy efficiency, cleanliness, and precise temperature control, making them ideal for melting ferrous and non-ferrous alloys with minimal contamination. They are also more environmentally friendly, producing less waste and emissions. On the other hand, electric arc furnaces are better suited for large-scale steel production and refining, offering superior metallurgical capabilities, especially for high-quality steel grades. However, they generate more waste, noise, and energy consumption.
Key Points Explained:
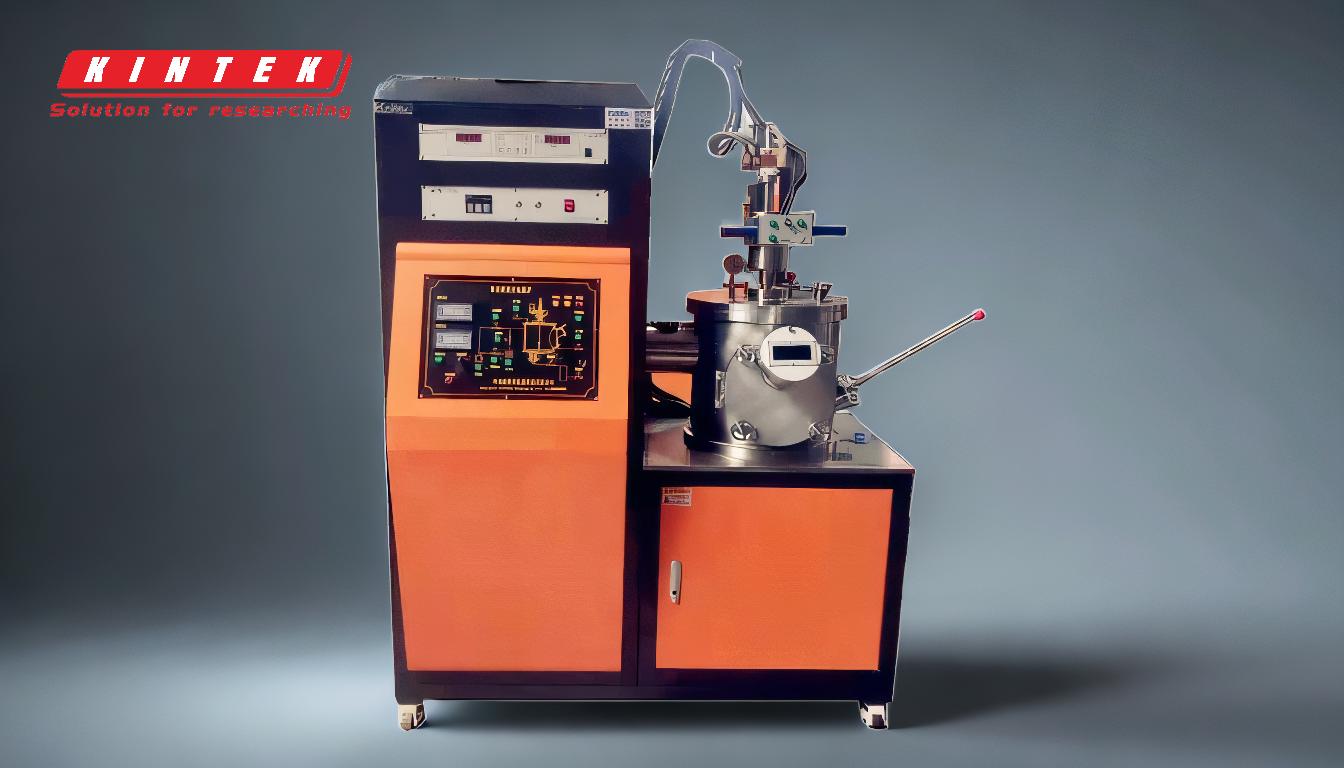
-
Energy Efficiency and Environmental Impact:
- Induction Furnace: Known for its energy efficiency, the induction furnace consumes less power and produces minimal waste and emissions. It does not require graphite electrodes, which eliminates carbon pick-up and reduces the carbon footprint. The process is clean and contained, making it environmentally friendly.
- Electric Arc Furnace: While effective for large-scale steel production, electric arc furnaces are less energy-efficient and generate significant waste residue, exhaust gas, and noise. They also consume more energy, making them less environmentally friendly compared to induction furnaces.
-
Melting and Heating Speed:
- Induction Furnace: Offers fast heating and melting speeds, which leads to high production efficiency. The heat is generated within the metal charge itself, allowing for rapid and uniform heating.
- Electric Arc Furnace: Although capable of melting large quantities of material, the heating process is generally slower compared to induction furnaces, especially for smaller batches.
-
Temperature Control and Metallurgical Quality:
- Induction Furnace: Provides precise temperature control, which is crucial for preserving valuable alloying elements and producing high-quality alloys. The small temperature difference between the core and surface of the material ensures uniform heating.
- Electric Arc Furnace: Offers superior metallurgical capabilities, making it suitable for refining high-quality steel grades. However, the temperature control is less precise compared to induction furnaces, which can affect the quality of certain alloys.
-
Operational Environment and Worker Conditions:
- Induction Furnace: Creates a superior working environment with less oxidation, decarburization, and pollution. The process is clean and safe, improving working conditions for operators.
- Electric Arc Furnace: Generates more noise, dust, and pollutants, which can create a less favorable working environment. The process is more labor-intensive and can be hazardous for workers.
-
Applications and Material Suitability:
- Induction Furnace: Ideal for melting both ferrous and non-ferrous alloys, especially in applications requiring minimal contamination and precise temperature control. It is commonly used in industrial settings for its efficiency and cleanliness.
- Electric Arc Furnace: Best suited for large-scale steel production and refining, particularly for high-quality steel grades. It is more versatile in handling a wide range of materials but is less efficient for small-scale or specialized applications.
-
Technological Advancements:
- Induction Furnace: Recent advancements in equipment and refractories have improved the metallurgical capabilities of induction furnaces, allowing for the production of high-quality low-alloy steels, high-alloy steels, and even super low-carbon stainless steels and superalloys.
- Electric Arc Furnace: While already well-established, continuous improvements in arc furnace technology have enhanced its efficiency and reduced its environmental impact, though it still lags behind induction furnaces in these areas.
In summary, the choice between an induction furnace and an electric arc furnace depends on the specific needs of the application. Induction furnaces are better for energy efficiency, environmental friendliness, and precise temperature control, making them ideal for smaller-scale, high-quality alloy production. Electric arc furnaces, while less efficient and more polluting, are better suited for large-scale steel production and refining, offering superior metallurgical capabilities.
Summary Table:
Feature | Induction Furnace | Electric Arc Furnace |
---|---|---|
Energy Efficiency | High energy efficiency, minimal waste and emissions | Less energy-efficient, generates more waste and emissions |
Heating Speed | Fast heating and melting speeds | Slower heating, especially for smaller batches |
Temperature Control | Precise temperature control, uniform heating | Superior metallurgical capabilities but less precise temperature control |
Environmental Impact | Clean and contained process, environmentally friendly | Generates more noise, dust, and pollutants |
Applications | Ideal for ferrous and non-ferrous alloys, minimal contamination | Best for large-scale steel production and refining |
Operational Environment | Superior working conditions, less oxidation and pollution | Less favorable working environment, more labor-intensive |
Still unsure which furnace is right for your application? Contact our experts today for personalized advice!