When comparing nichrome and tungsten, the choice largely depends on the specific application, particularly the temperature requirements and environmental conditions. Tungsten stands out for its extremely high melting point, making it ideal for applications involving very high temperatures and vacuum conditions. Nichrome, on the other hand, is more commonly used in lower-temperature applications due to its good resistance to oxidation and ease of fabrication.
Key Points Explained:
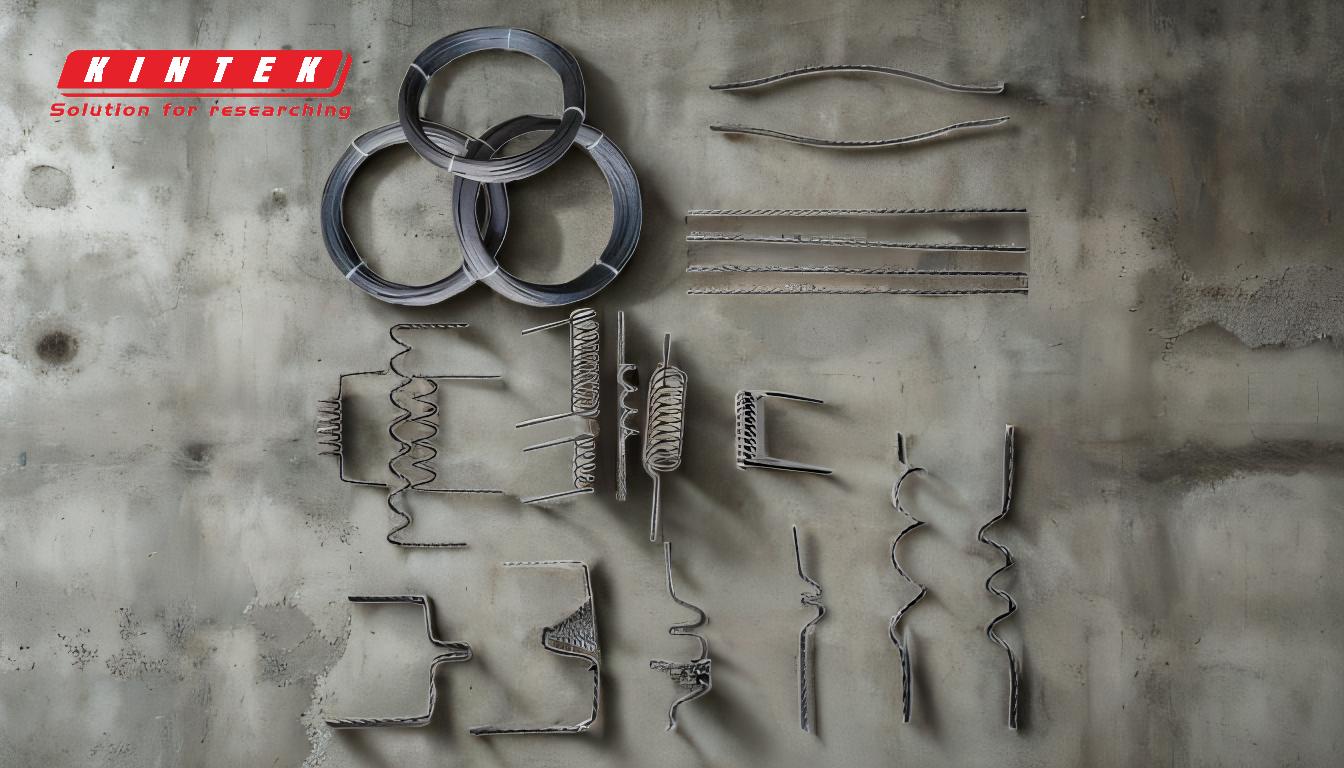
-
Temperature Tolerance:
- Tungsten: Tungsten has a melting point of about 3422°C, which makes it suitable for extreme high-temperature applications, such as in vacuum furnaces where temperatures can reach up to 2500°C.
- Nichrome: Nichrome typically operates effectively at temperatures up to about 1200°C, which is suitable for many industrial heating applications but not for the extreme conditions that tungsten can handle.
-
Vacuum and Environmental Conditions:
- Tungsten: It performs exceptionally well in high vacuum environments (less than 10^-4 Torr) and can maintain structural integrity at very high temperatures.
- Nichrome: While nichrome can be used in various environments, its performance in high vacuum or extremely high-temperature conditions is not comparable to tungsten.
-
Mechanical Properties:
- Tungsten: The mechanical properties of tungsten, such as ductility and fracture toughness, degrade as it undergoes recrystallization at high temperatures. However, the recrystallization temperature can be increased by adding certain oxides or silicates.
- Nichrome: Nichrome maintains good mechanical properties at its operational temperatures and is less prone to issues related to recrystallization.
-
Application Suitability:
- Tungsten: Best suited for specialized applications requiring high temperature and high vacuum, such as in aerospace and high-tech manufacturing industries.
- Nichrome: More versatile for general heating applications, including toasters, hairdryers, and industrial furnaces operating at lower temperatures.
-
Cost and Fabrication:
- Tungsten: Generally more expensive and harder to fabricate due to its high melting point and brittleness at room temperature.
- Nichrome: Less expensive and easier to work with, making it a preferred choice for a wide range of heating applications.
In summary, the choice between nichrome and tungsten should be guided by the specific requirements of the application, particularly the operating temperature and environmental conditions. Tungsten is superior for extreme conditions, while nichrome offers a cost-effective solution for less demanding environments.
Summary Table:
Feature | Tungsten | Nichrome |
---|---|---|
Temperature Tolerance | Extremely high (up to 3422°C), ideal for extreme high-temperature applications | Effective up to 1200°C, suitable for lower-temperature applications |
Vacuum Performance | Excellent in high vacuum environments (<10^-4 Torr) | Limited performance in high vacuum or extreme conditions |
Mechanical Properties | Degrades at high temperatures; recrystallization can be mitigated with additives | Maintains good properties at operational temperatures |
Application Suitability | Specialized applications (e.g., aerospace, high-tech manufacturing) | Versatile for general heating (e.g., toasters, hairdryers, furnaces) |
Cost and Fabrication | Expensive and difficult to fabricate | Cost-effective and easy to work with |
Still unsure which material is right for your application? Contact our experts today for personalized advice!