The best heat source for brazing depends on the specific application, materials being joined, and desired outcomes. Common heat sources include induction heating, torch brazing, furnace brazing, and resistance heating. Each method has its advantages and limitations, such as precision, speed, energy efficiency, and suitability for different materials. Induction heating is often preferred for its localized heat application and energy efficiency, while furnace brazing is ideal for high-volume production. Torch brazing offers flexibility and portability, and resistance heating is suitable for smaller components. The choice of heat source should align with the project requirements, material properties, and production scale.
Key Points Explained:
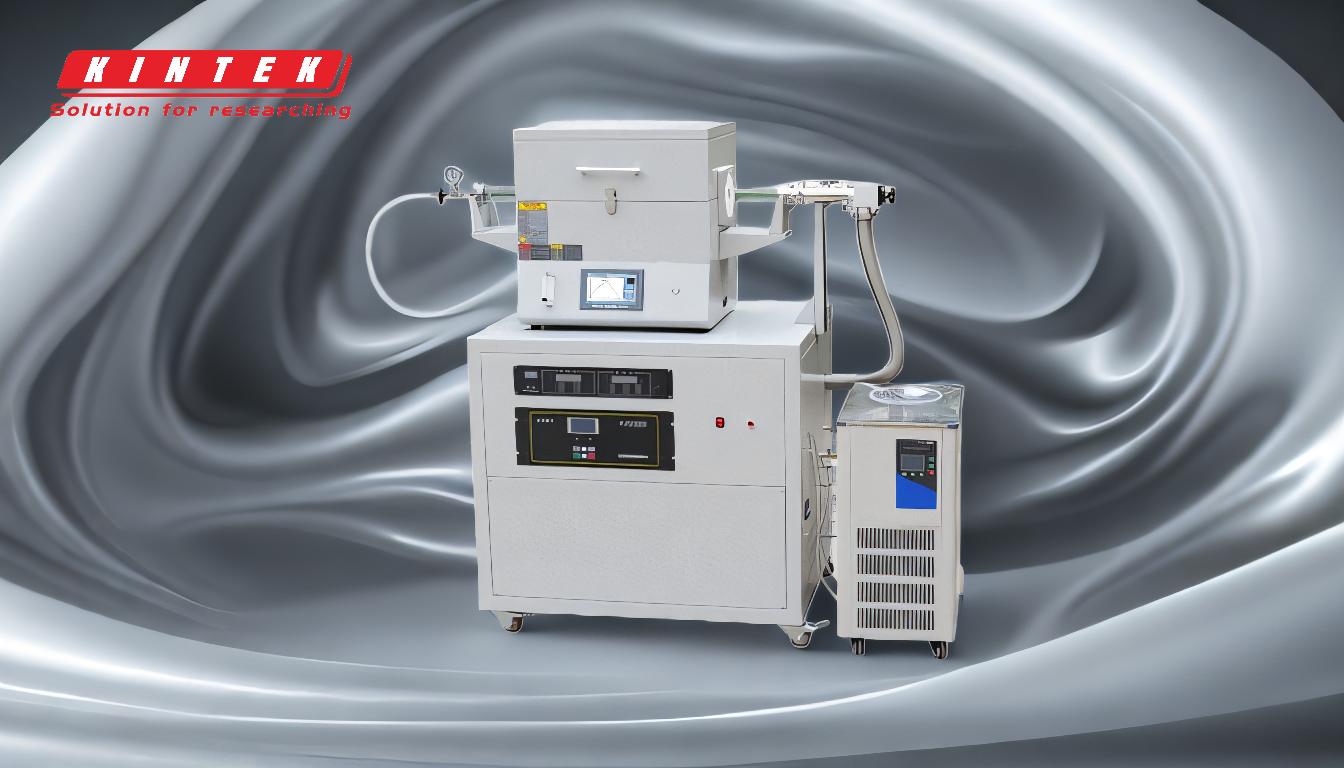
-
Induction Heating:
- Advantages: Induction heating is highly efficient and provides localized heat, minimizing thermal distortion and energy waste. It is ideal for precise applications and works well with conductive materials like metals.
- Applications: Commonly used in automotive, aerospace, and electronics industries where precision and repeatability are critical.
- Limitations: Requires specialized equipment and is less effective for non-conductive materials.
-
Torch Brazing:
- Advantages: Torch brazing is portable, flexible, and suitable for small-scale or on-site repairs. It allows for manual control of heat application.
- Applications: Often used in plumbing, HVAC, and jewelry making.
- Limitations: Requires skilled operators and can be less consistent compared to automated methods.
-
Furnace Brazing:
- Advantages: Furnace brazing is ideal for high-volume production, offering consistent and uniform heating. It can handle complex assemblies and multiple joints simultaneously.
- Applications: Widely used in manufacturing industries, such as automotive and aerospace, for mass production.
- Limitations: High initial setup costs and longer cycle times compared to other methods.
-
Resistance Heating:
- Advantages: Resistance heating is efficient for small components and provides rapid heating. It is suitable for materials with high electrical resistance.
- Applications: Commonly used in electronics and small-scale manufacturing.
- Limitations: Limited to smaller parts and requires precise control of electrical parameters.
-
Factors to Consider When Choosing a Heat Source:
- Material Properties: The thermal conductivity and melting point of the materials being joined influence the choice of heat source.
- Production Scale: High-volume production may favor furnace brazing, while small-scale or custom work may benefit from torch or induction heating.
- Precision Requirements: Applications requiring high precision, such as electronics, may prefer induction or resistance heating.
- Energy Efficiency: Induction heating is often the most energy-efficient option, while torch brazing may require more energy due to manual control.
By evaluating these factors, you can select the most appropriate heat source for your brazing application, ensuring optimal results and efficiency.
Summary Table:
Heat Source | Advantages | Applications | Limitations |
---|---|---|---|
Induction Heating | Highly efficient, localized heat, minimal thermal distortion | Automotive, aerospace, electronics | Requires specialized equipment, less effective for non-conductive materials |
Torch Brazing | Portable, flexible, manual control of heat | Plumbing, HVAC, jewelry making | Requires skilled operators, less consistent |
Furnace Brazing | Consistent, uniform heating, ideal for high-volume production | Automotive, aerospace, manufacturing | High setup costs, longer cycle times |
Resistance Heating | Efficient for small components, rapid heating | Electronics, small-scale manufacturing | Limited to smaller parts, requires precise control |
Need help choosing the best heat source for your brazing project? Contact our experts today for personalized advice!