When selecting materials for use inside a vacuum chamber, it is crucial to avoid substances that can outgas, degrade, or contaminate the vacuum environment. Materials like rubber, certain plastics, and adhesives are generally unsuitable due to their tendency to release gases or particles under vacuum conditions. Instead, materials like stainless steel, ceramics, and silicone are preferred for their durability and minimal outgassing properties. The vacuum environment is essential for processes like sputtering, sintering, and heat treatment, as it ensures sterility, prevents oxidation, and maintains the quality of the final product. Proper sealing and material selection are critical to maintaining the vacuum integrity and achieving optimal results.
Key Points Explained:
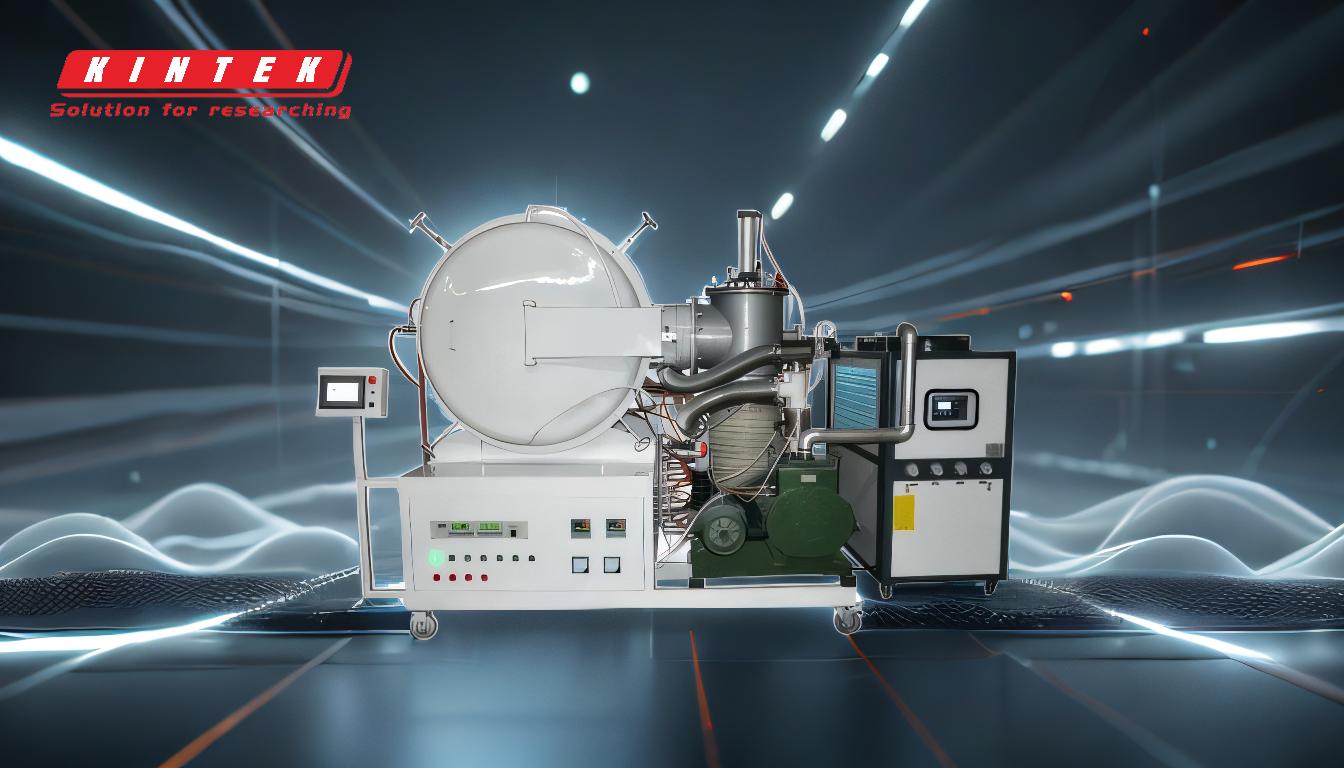
-
Importance of Vacuum Integrity:
- Maintaining a vacuum environment is critical for processes like sintering, sputtering, and heat treatment. A vacuum prevents oxidation, contamination, and ensures the quality of the final product.
- For example, in a vacuum hot press, the absence of atmospheric gases facilitates atomic diffusion, leading to high-density solid products.
-
Materials to Avoid:
- Rubber and Certain Plastics: These materials tend to outgas, releasing volatile organic compounds (VOCs) that can contaminate the vacuum environment and degrade the process.
- Adhesives and Sealants: Many adhesives contain solvents or compounds that can release gases under vacuum, compromising the chamber's integrity.
- Materials with High Vapor Pressure: Substances like lead or other volatile metals should be avoided, as they can evaporate and contaminate the chamber.
-
Preferred Materials:
- Stainless Steel: Known for its durability and low outgassing properties, stainless steel is widely used in vacuum chambers and components.
- Ceramics: Ceramics are ideal for high-temperature applications and have minimal outgassing, making them suitable for vacuum environments.
- Silicone: Silicone tubing is often used instead of rubber in vacuum systems because it ages more slowly and has better resistance to outgassing.
-
Sealing and Structural Considerations:
- Gas-tight welding and sealed structures are essential for maintaining vacuum integrity. Accessories like water-cooled electrodes and thermocouple export devices must be designed to minimize air leakage.
- High-efficiency fume extraction systems are also important for maintaining a clean vacuum environment, especially in processes like sputtering.
-
Vacuum Levels in Heat Treatment:
- Vacuum heat treatment furnaces typically operate at vacuum levels ranging from 1.33 to 1.33 x 10^-3 Pa. Understanding the required vacuum level is crucial for selecting appropriate materials and ensuring process efficiency.
-
Practical Implications:
- In sputtering, a vacuum ensures sterility and prevents contamination, which is essential for achieving high-quality thin film deposition.
- For sintering, a vacuum environment prevents oxidation and allows for better control of the process, improving the final product's physical and mechanical properties.
By carefully selecting materials and ensuring proper sealing, you can maintain the integrity of the vacuum chamber and achieve optimal results in various industrial processes.
Summary Table:
Category | Materials to Avoid | Preferred Materials |
---|---|---|
Outgassing Materials | Rubber, Certain Plastics, Adhesives | Stainless Steel, Ceramics |
High Vapor Pressure | Lead, Volatile Metals | Silicone |
Sealing Requirements | Solvent-Based Sealants | Gas-Tight Welding, Silicone |
Ensure your vacuum chamber operates at peak efficiency—contact our experts today for tailored solutions!