Thin film deposition is a critical process in various industries, including semiconductors, optics, and coatings. The methods used to deposit thin films can be broadly categorized into chemical and physical deposition techniques. Chemical methods involve chemical reactions or solutions to form thin films, while physical methods rely on physical processes like evaporation or sputtering. Common chemical methods include Chemical Vapor Deposition (CVD), Atomic Layer Deposition (ALD), and sol-gel, while physical methods include Physical Vapor Deposition (PVD), thermal evaporation, and sputtering. Each method has its advantages and is chosen based on the desired film properties, substrate material, and application requirements.
Key Points Explained:
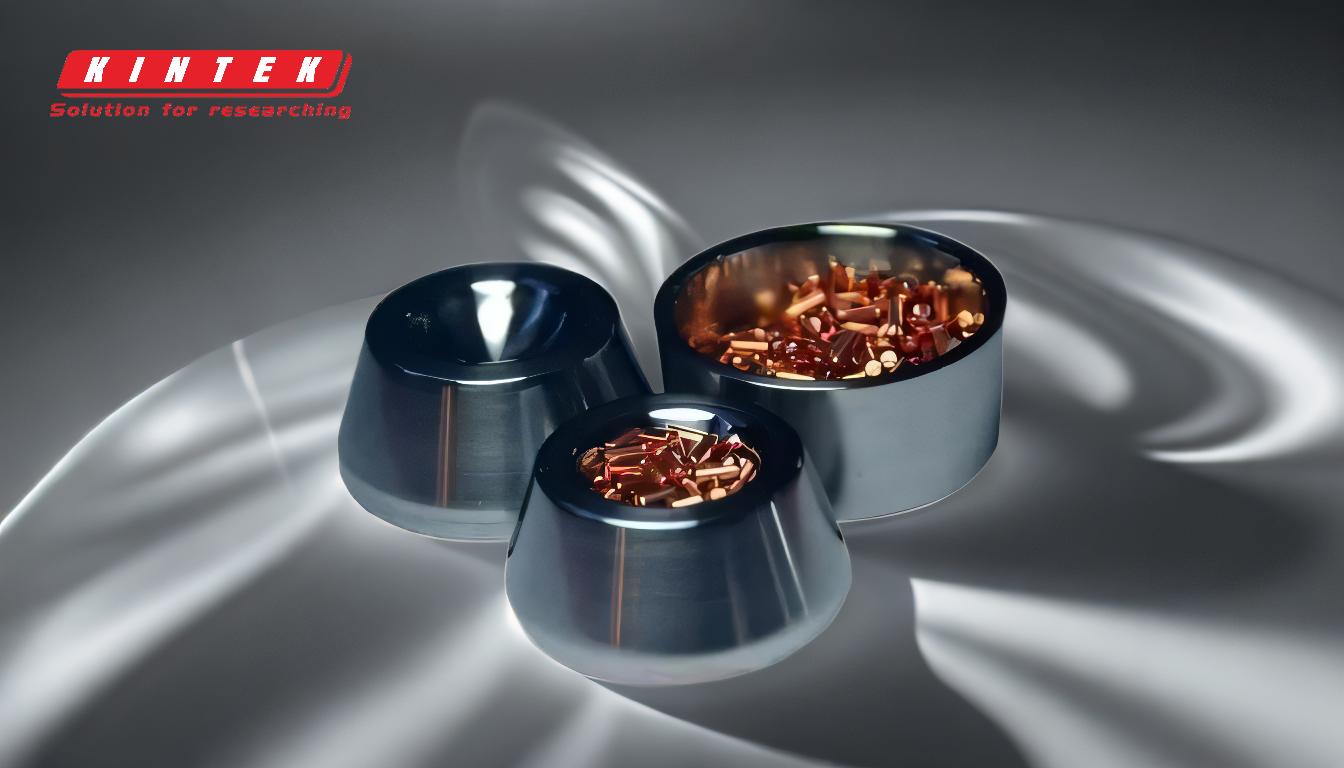
-
Chemical Deposition Methods
These methods rely on chemical reactions or solutions to deposit thin films. They are widely used for their precision and ability to produce uniform coatings.-
Chemical Vapor Deposition (CVD):
- Involves chemical reactions between gaseous precursors to form a solid thin film on the substrate.
- Commonly used in the semiconductor industry due to its high precision and ability to deposit complex materials.
-
Plasma-Enhanced CVD (PECVD):
- A variation of CVD that uses plasma to enhance the chemical reaction, allowing deposition at lower temperatures.
-
Atomic Layer Deposition (ALD):
- Deposits films one atomic layer at a time, offering exceptional control over film thickness and uniformity.
- Ideal for applications requiring ultra-thin, conformal coatings.
-
Sol-Gel, Dip Coating, and Spin Coating:
- These methods involve applying a liquid solution to the substrate and then solidifying it through drying or curing.
- Often used for optical coatings and low-cost applications.
-
Chemical Vapor Deposition (CVD):
-
Physical Deposition Methods
These methods use physical processes to deposit thin films, such as vaporization or sputtering. They are known for producing high-purity coatings.-
Physical Vapor Deposition (PVD):
- Includes techniques like sputtering, thermal evaporation, and electron beam evaporation.
- Sputtering involves bombarding a target material with ions to eject atoms, which then deposit onto the substrate.
- Thermal and electron beam evaporation involve heating the material until it vaporizes, then condensing it onto the substrate.
-
Pulsed Laser Deposition (PLD):
- Uses a high-energy laser to vaporize the target material, forming a thin film on the substrate.
- Suitable for depositing complex materials like oxides and superconductors.
-
Molecular Beam Epitaxy (MBE):
- A highly precise method for growing crystalline thin films, often used in semiconductor and optoelectronic applications.
-
Physical Vapor Deposition (PVD):
-
Comparison of Methods
-
Precision and Uniformity:
- Chemical methods like CVD and ALD offer superior precision and uniformity, making them ideal for semiconductor and nanotechnology applications.
- Physical methods like sputtering and evaporation are better suited for applications requiring high-purity coatings.
-
Temperature Requirements:
- CVD and ALD often require high temperatures, while PECVD and physical methods can operate at lower temperatures.
-
Cost and Scalability:
- Chemical methods like sol-gel and dip coating are cost-effective for large-scale applications, while physical methods like MBE and PLD are more expensive but offer higher precision.
-
Precision and Uniformity:
-
Applications of Thin Film Deposition
-
Semiconductors:
- CVD and ALD are widely used for depositing thin films in integrated circuits and microelectronics.
-
Optics:
- Sputtering and evaporation are used to create anti-reflective and reflective coatings for lenses and mirrors.
-
Energy:
- Thin films are used in solar cells, batteries, and fuel cells, with methods like spray pyrolysis and CVD being common.
-
Coatings:
- PVD methods like sputtering and carbon coating are used for wear-resistant and decorative coatings.
-
Semiconductors:
-
Selection Criteria for Deposition Methods
-
Material Compatibility:
- Some materials are better suited to specific methods (e.g., oxides for PLD, metals for sputtering).
-
Film Thickness and Uniformity:
- ALD and CVD are preferred for ultra-thin and uniform films.
-
Substrate Sensitivity:
- Low-temperature methods like PECVD are ideal for heat-sensitive substrates.
-
Cost and Throughput:
- For high-volume production, cost-effective methods like sol-gel and dip coating are preferred.
-
Material Compatibility:
By understanding the strengths and limitations of each deposition method, you can select the most appropriate technique for your specific application, ensuring optimal performance and cost-effectiveness.
Summary Table:
Category | Methods | Key Features | Applications |
---|---|---|---|
Chemical Deposition | CVD, PECVD, ALD, Sol-Gel, Dip Coating, Spin Coating | High precision, uniform coatings, low-temperature options (PECVD) | Semiconductors, optical coatings, low-cost large-scale applications |
Physical Deposition | PVD (sputtering, thermal evaporation, electron beam evaporation), PLD, MBE | High-purity coatings, precise control, suitable for complex materials | Optics, wear-resistant coatings, semiconductors, superconductors |
Need help selecting the right thin film deposition method for your project? Contact our experts today!