Thin film formation in thermal evaporation is a complex process influenced by several key parameters. These parameters include the properties of the substrate, the thickness of the film, the deposition techniques, and the energy level of the coating particles. Understanding these factors is crucial for achieving the desired film characteristics. The substrate's properties, such as surface roughness and chemical composition, can significantly affect the adhesion and uniformity of the thin film. The thickness of the film, which is influenced by the duration of the deposition process, plays a critical role in determining the film's mechanical and optical properties. Additionally, the energy level of the coating particles, which can vary widely, affects the film's density and microstructure. By carefully controlling these parameters, one can tailor the thin film's properties to meet specific application requirements.
Key Points Explained:
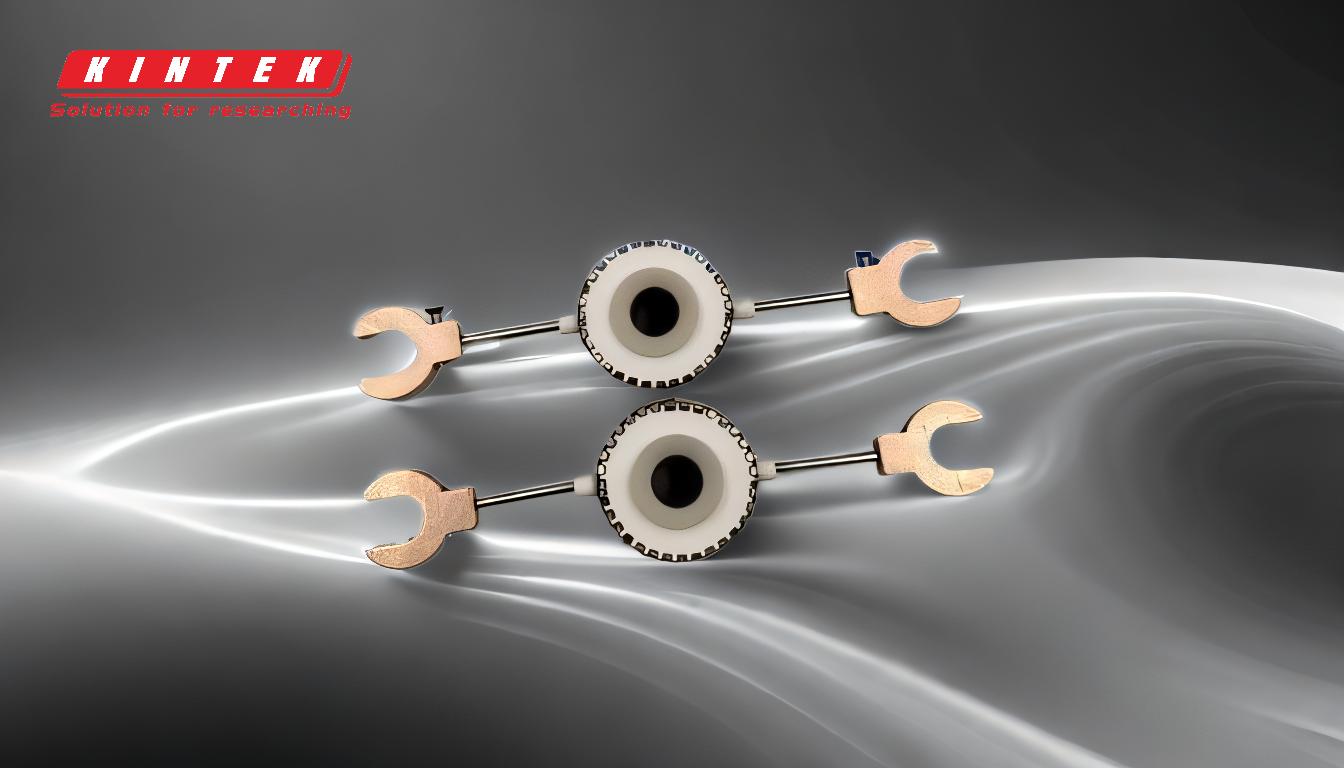
-
Substrate Properties:
- The underlying properties of the substrate, such as surface roughness and chemical composition, play a crucial role in thin film formation. A smooth and chemically compatible substrate ensures better adhesion and uniformity of the thin film. Surface roughness can lead to defects and irregularities in the film, while chemical incompatibility can result in poor adhesion and delamination.
-
Film Thickness:
- The thickness of the thin film is a critical parameter that influences its mechanical, optical, and electrical properties. Thicker films may offer better mechanical strength but could also introduce stress and defects. Conversely, thinner films might be more uniform but could lack the desired mechanical robustness. The duration of the thermal evaporation process directly affects the film thickness, making it essential to control the deposition time precisely.
-
Deposition Techniques:
- The choice of deposition technique, such as thermal evaporation, sputtering, or chemical vapor deposition, significantly impacts the film's characteristics. Thermal evaporation, for instance, is known for producing high-purity films with minimal contamination. However, it may not be suitable for all materials, especially those with high melting points. The deposition technique also affects the film's microstructure, density, and adhesion to the substrate.
-
Energy Level of Coating Particles:
- The energy level of the coating particles during deposition can range from tens to thousands of electron volts. Higher energy levels generally result in denser and more adherent films due to increased particle mobility and surface diffusion. However, excessively high energy levels can cause damage to the substrate or lead to undesirable phase transformations in the film. Therefore, optimizing the energy level is crucial for achieving the desired film properties.
-
Material Selection:
- The type of material used for the thin film is another critical factor. Different materials exhibit varying thermal, mechanical, and optical properties, which can influence the film's performance. For example, metals like aluminum and gold are commonly used for their excellent conductivity and reflectivity, while oxides like silicon dioxide are preferred for their insulating properties. The material's compatibility with the substrate and the deposition technique must also be considered to ensure optimal film formation.
-
Process Parameters:
- Various process parameters, such as temperature, pressure, and deposition rate, need to be carefully controlled during thermal evaporation. The temperature affects the vapor pressure of the material, while the pressure in the deposition chamber influences the mean free path of the evaporated particles. A higher deposition rate can lead to thicker films but may also introduce defects if not properly managed. Balancing these parameters is essential for achieving high-quality thin films.
By understanding and controlling these key parameters, one can effectively influence the formation and properties of thin films in thermal evaporation. This knowledge is invaluable for applications ranging from microelectronics to optical coatings, where precise control over film characteristics is essential.
Summary Table:
Parameter | Effect on Thin Film Formation |
---|---|
Substrate Properties | Influences adhesion, uniformity, and defect formation based on surface roughness and composition. |
Film Thickness | Affects mechanical, optical, and electrical properties; controlled by deposition duration. |
Deposition Techniques | Determines film purity, microstructure, and adhesion; thermal evaporation is a common method. |
Energy Level of Particles | Higher energy levels create denser, more adherent films but may damage the substrate. |
Material Selection | Different materials (e.g., metals, oxides) influence thermal, mechanical, and optical properties. |
Process Parameters | Temperature, pressure, and deposition rate must be balanced to achieve high-quality films. |
Need help optimizing thin film formation for your application? Contact our experts today for tailored solutions!