To deposit ZnO (Zinc Oxide) thin films, the most suitable type of sputtering system is magnetron sputtering. This method is widely used due to its ability to produce high-quality, uniform thin films with excellent adhesion and controlled stoichiometry. Magnetron sputtering is a type of Physical Vapor Deposition (PVD) technique that utilizes a magnetic field to confine electrons near the target surface, enhancing the ionization of the sputtering gas (typically argon) and improving deposition efficiency. This method is particularly effective for materials like ZnO, which require precise control over film properties such as thickness, crystallinity, and composition.
Key Points Explained:
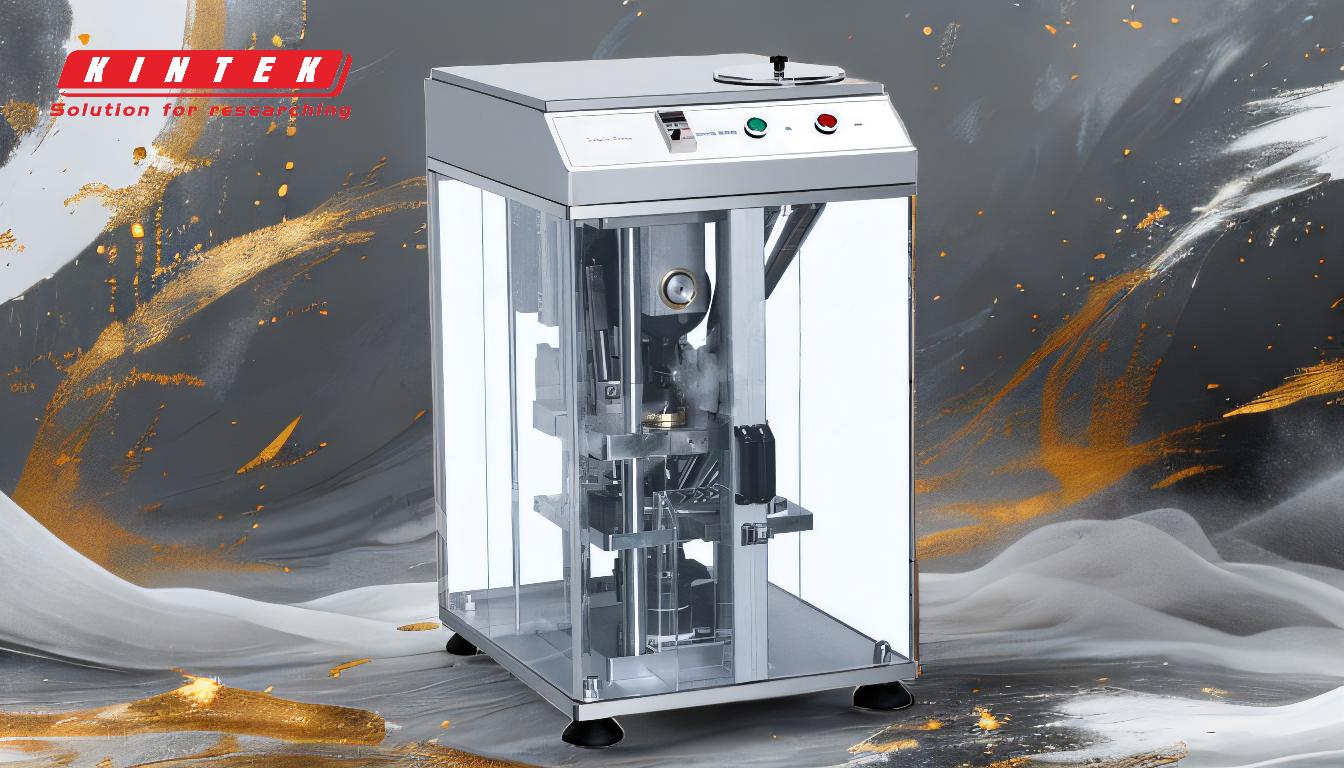
-
Magnetron Sputtering for ZnO Thin Films:
- Magnetron sputtering is the preferred method for depositing ZnO thin films due to its ability to produce films with high uniformity, excellent adhesion, and controlled properties.
- The process involves the use of a magnetic field to trap electrons near the target surface, increasing the ionization of the sputtering gas (argon) and enhancing the sputtering rate.
- This method is ideal for ZnO because it allows for precise control over the film's stoichiometry, crystallinity, and thickness, which are critical for applications such as transparent conductive oxides, sensors, and optoelectronic devices.
-
Advantages of Magnetron Sputtering:
- High Deposition Rates: The magnetic field increases the plasma density, leading to faster deposition rates compared to other sputtering methods.
- Low Substrate Heating: The process generates less heat, reducing the risk of damaging temperature-sensitive substrates.
- Scalability: Magnetron sputtering systems can be easily scaled up for industrial applications, making them suitable for large-area coatings.
- Versatility: It can be used with a wide range of target materials, including metals, alloys, and ceramics like ZnO.
-
System Configuration for ZnO Deposition:
- Target Material: A high-purity ZnO target is used to ensure the quality of the deposited film.
- Sputtering Gas: Argon is the most commonly used sputtering gas due to its inert nature and ability to generate a stable plasma.
- Substrate Preparation: Substrates are often pre-cleaned using in situ sputter etching or ion source capabilities to remove contaminants and improve film adhesion.
- Substrate Heating: Pre-heat stations can be used to control the substrate temperature, which influences the crystallinity and properties of the ZnO film.
- Multiple Cathodes: Systems with multiple cathodes allow for co-sputtering or sequential deposition of different materials, enabling the creation of multi-layer or doped ZnO films.
-
Process Parameters:
- Power Density: The power applied to the target affects the sputtering rate and film properties. Optimal power density ensures efficient sputtering without damaging the target.
- Gas Pressure: The pressure of the sputtering gas influences the mean free path of the sputtered atoms and the quality of the film. Lower pressures typically result in denser films.
- Substrate Bias: Applying a bias voltage to the substrate can improve film adhesion and modify the film's microstructure.
-
Applications of ZnO Thin Films:
- Transparent Conductive Oxides: ZnO films are widely used in solar cells, touchscreens, and displays due to their transparency and conductivity.
- Sensors: ZnO's piezoelectric properties make it suitable for gas sensors, biosensors, and pressure sensors.
- Optoelectronics: ZnO films are used in light-emitting diodes (LEDs), laser diodes, and photodetectors.
In summary, magnetron sputtering is the most effective and widely used method for depositing ZnO thin films. Its ability to produce high-quality, uniform films with precise control over properties makes it ideal for a variety of applications in electronics, optics, and sensing. The system's configurability, scalability, and versatility further enhance its suitability for both research and industrial use.
Summary Table:
Aspect | Details |
---|---|
Preferred Method | Magnetron Sputtering |
Key Advantages | High deposition rates, low substrate heating, scalability, versatility |
Target Material | High-purity ZnO |
Sputtering Gas | Argon |
Applications | Transparent conductive oxides, sensors, optoelectronics |
Ready to enhance your thin film deposition process? Contact our experts today to learn more about magnetron sputtering systems!