Induction furnaces are widely used in metallurgical processes for melting metals and alloys due to their efficiency, precision, and ability to generate high temperatures. The type of transformer used in an induction furnace is a medium-frequency transformer, which is a critical component of the furnace's power supply system. This transformer is designed to handle the specific requirements of induction heating, such as converting and supplying medium-frequency alternating current (AC) to the induction coil. The transformer ensures efficient energy transfer and precise control over the heating process, making it essential for the furnace's operation.
Key Points Explained:
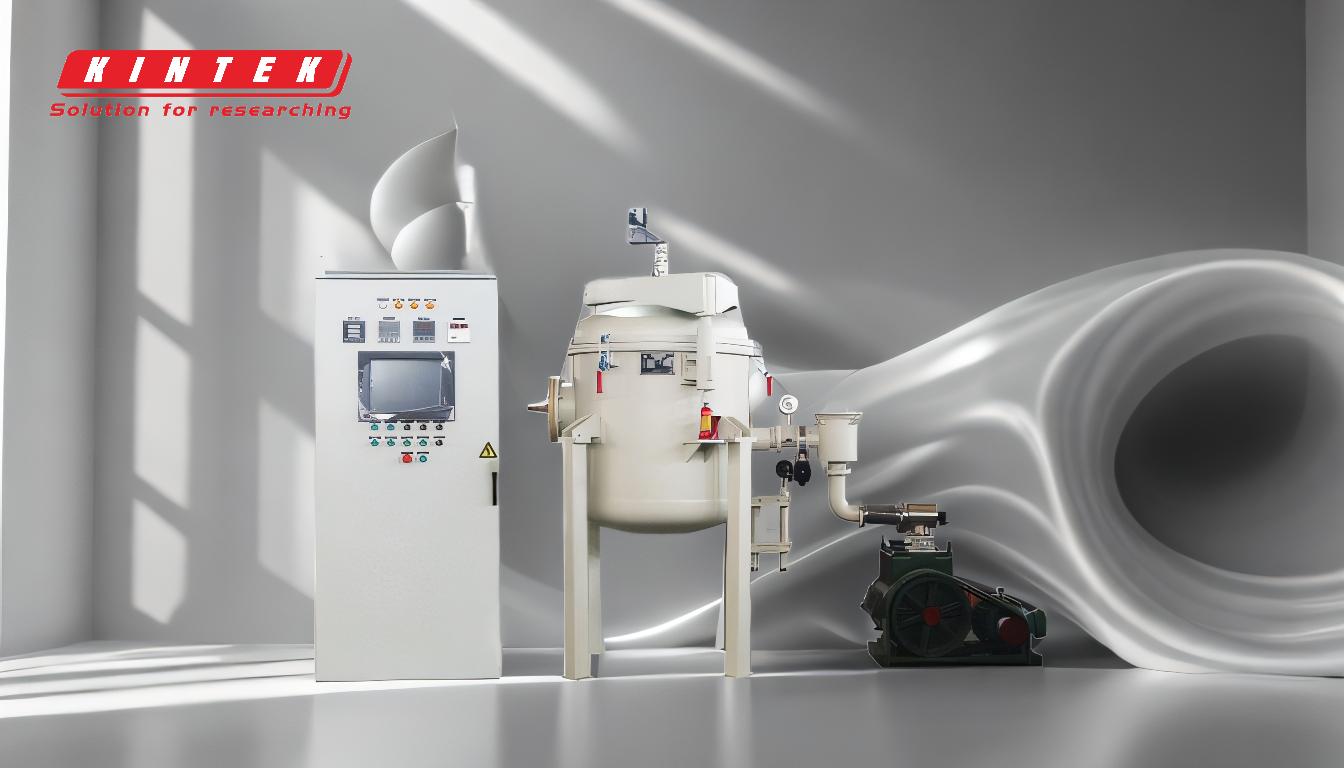
-
Role of the Transformer in an Induction Furnace:
- The transformer in an induction furnace is responsible for converting and supplying the appropriate electrical power to the induction coil.
- It ensures that the alternating current (AC) is adjusted to the required frequency and voltage levels for efficient induction heating.
- Without the transformer, the induction furnace would not be able to generate the electromagnetic field necessary for heating the metal charge.
-
Medium-Frequency Transformer:
- Induction furnaces typically use medium-frequency transformers, which operate at frequencies ranging from 150 Hz to 8000 Hz.
- This frequency range is ideal for generating the electromagnetic field needed to induce eddy currents in the metal charge.
- The transformer steps down the voltage and steps up the current to match the requirements of the induction coil, ensuring optimal energy transfer.
-
Power Supply System:
- The transformer is part of a larger power supply system that includes a rectifier, inverter, and induction coil.
- The rectifier converts three-phase 50 Hz AC into direct current (DC), which is then filtered and inverted into medium-frequency AC by the inverter.
- The transformer ensures that the medium-frequency AC is delivered to the induction coil at the correct voltage and current levels.
-
Efficiency and Precision:
- The transformer plays a crucial role in maintaining the efficiency and precision of the induction furnace.
- By providing the correct frequency and power levels, it ensures that the metal charge is heated uniformly and rapidly.
- This precision is essential for melting metals and creating alloys with exact compositions.
-
Design Considerations:
- Medium-frequency transformers are designed to handle high power levels and operate at elevated temperatures.
- They are typically constructed using high-quality materials, such as laminated silicon steel cores and copper windings, to minimize energy losses and ensure durability.
- The transformer must also be designed to withstand the electromagnetic forces generated during operation.
-
Applications of Induction Furnaces:
- Induction furnaces are used in various industries, including steelmaking, foundries, and metal casting.
- The medium-frequency transformer is a key component that enables these furnaces to achieve high temperatures and precise control over the melting process.
- This makes induction furnaces suitable for producing high-quality metals and alloys with minimal impurities.
-
Advantages of Using Medium-Frequency Transformers:
- Energy Efficiency: Medium-frequency transformers minimize energy losses, making the induction furnace more efficient.
- Compact Design: These transformers are smaller and lighter compared to low-frequency transformers, allowing for more compact furnace designs.
- Rapid Heating: The medium-frequency AC supplied by the transformer enables rapid heating of the metal charge, reducing processing times.
- Precision Control: The transformer allows for precise control over the heating process, ensuring consistent results.
-
Maintenance and Durability:
- Medium-frequency transformers are designed for long-term operation with minimal maintenance.
- However, regular inspections and maintenance are necessary to ensure optimal performance and prevent issues such as overheating or insulation failure.
- Proper cooling systems, such as air or liquid cooling, are often integrated into the transformer design to maintain safe operating temperatures.
In summary, the medium-frequency transformer is the type of transformer used in induction furnaces. It is a critical component that enables the furnace to generate the electromagnetic field required for induction heating. By converting and supplying medium-frequency AC to the induction coil, the transformer ensures efficient energy transfer, rapid heating, and precise control over the melting process. This makes it an essential part of the induction furnace's power supply system, supporting its applications in metallurgical processes and metal production.
Summary Table:
Aspect | Details |
---|---|
Transformer Type | Medium-frequency transformer |
Frequency Range | 150 Hz to 8000 Hz |
Key Function | Converts and supplies medium-frequency AC to the induction coil |
Efficiency | Minimizes energy losses, ensuring rapid and uniform heating |
Applications | Steelmaking, foundries, metal casting |
Advantages | Energy efficiency, compact design, rapid heating, and precision control |
Maintenance | Designed for durability with minimal maintenance requirements |
Ready to optimize your metal melting process? Contact us today to learn more about induction furnace transformers!