Vacuum deposition methods are essential for producing high-quality, high-performance solid materials, particularly in industries requiring precision, durability, and specific material properties. Among the various techniques, Physical Vapor Deposition (PVD) stands out as a leading method for achieving superior material quality. PVD involves depositing atoms or molecules one at a time, often using high-energy ions or plasma to modify film properties or activate reactive gases. This method is highly versatile, environmentally friendly, and capable of producing materials with exceptional wear resistance, corrosion resistance, and decorative finishes. Hybrid techniques, such as combining sputter deposition with plasma-enhanced chemical vapor deposition (PECVD), further enhance the capabilities of vacuum deposition, enabling the creation of advanced composite materials like metal carbides and carbonitrides.
Key Points Explained:
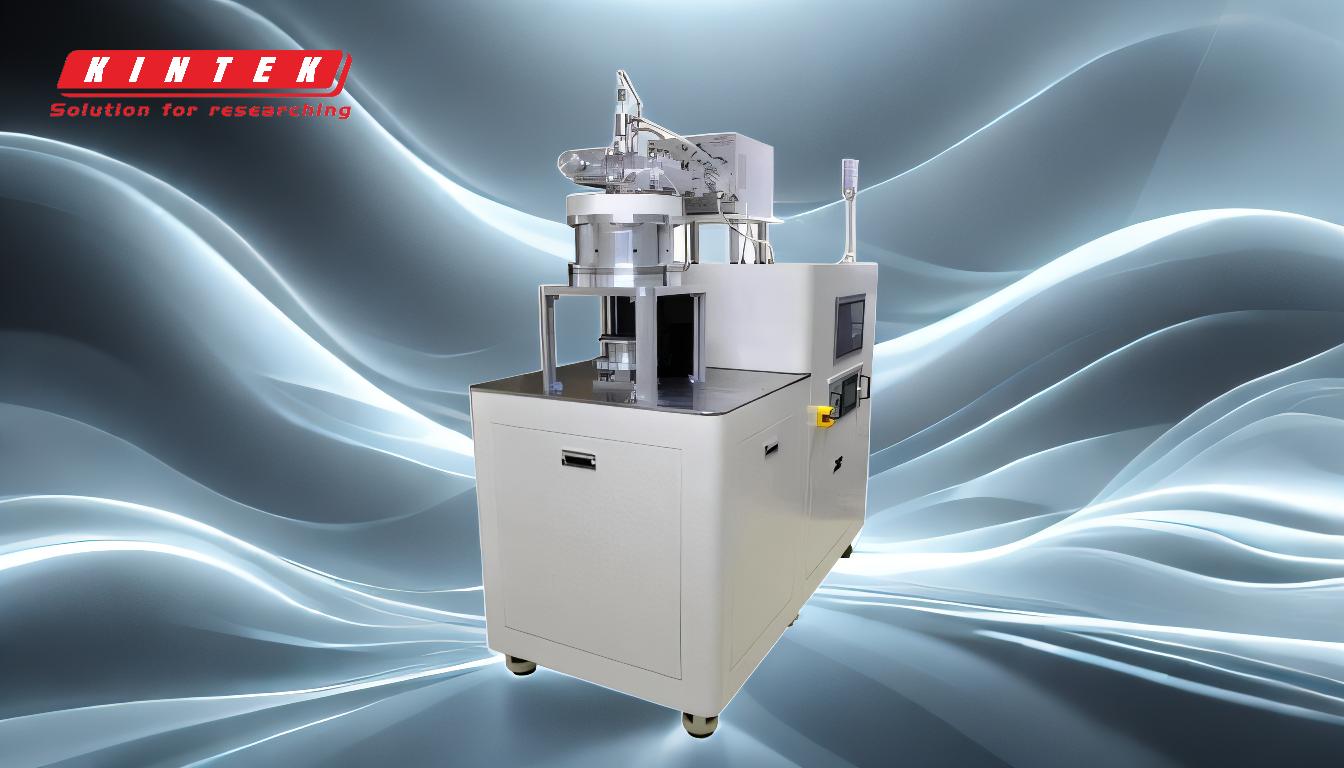
-
Physical Vapor Deposition (PVD):
- PVD is a widely used vacuum deposition method for producing high-quality solid materials. It involves the deposition of atoms or molecules in a vacuum environment, often using high-energy ions or plasma to enhance film properties.
- Advantages:
- Produces dense, uniform coatings with excellent adhesion.
- Enables the deposition of a wide range of materials, including metals, ceramics, and composites.
- Offers superior wear resistance, corrosion resistance, and decorative finishes.
- Applications:
- Used in industries such as aerospace, automotive, and electronics for coatings on cutting tools, medical devices, and optical components.
-
Hybrid Vacuum Deposition Techniques:
- Combining multiple deposition methods, such as sputter deposition with plasma-enhanced chemical vapor deposition (PECVD), allows for the creation of advanced materials with tailored properties.
- Example:
- Sputter deposition of a metal combined with PECVD of carbon from acetylene can produce wear-resistant metal carbide coatings.
- Introducing nitrogen during deposition can create carbonitrides, which are used for both decorative and functional applications.
- Advantages:
- Enables precise control over material composition and properties.
- Produces materials with unique characteristics, such as color variations in titanium carbonitride coatings.
-
Environmental and Operational Advantages of Vacuum Deposition:
- Vacuum deposition processes are environmentally friendly, with minimal waste and reduced emissions compared to traditional coating methods.
- Key benefits:
- Materials are protected from oxidation and contamination, ensuring high purity.
- The vacuum environment allows for longer mean free paths of vapor molecules, ensuring efficient and uniform deposition.
- Applications:
- Ideal for industries requiring high-precision coatings, such as semiconductor manufacturing and optical lens production.
-
Versatility and Ecological Cleanliness:
- Vacuum deposition is highly versatile, capable of depositing a wide range of materials, including metals, ceramics, and polymers.
- Ecological benefits:
- Reduces the need for hazardous chemicals and solvents.
- Minimizes waste generation and energy consumption.
- Applications:
- Used in the production of thin-film solar cells, decorative coatings, and advanced composites.
-
Future Trends and Innovations:
- Ongoing research focuses on developing hybrid and multi-layer deposition techniques to further enhance material performance.
- Innovations:
- Integration of nanotechnology for ultra-thin, high-performance coatings.
- Development of eco-friendly precursors and processes to reduce environmental impact.
- Applications:
- Emerging fields such as flexible electronics, energy storage, and biomedical devices.
By leveraging the precision and versatility of vacuum deposition methods like PVD and hybrid techniques, manufacturers can produce high-quality, high-performance solid materials tailored to specific industrial needs. These methods not only ensure superior material properties but also align with global sustainability goals by minimizing environmental impact.
Summary Table:
Aspect | Details |
---|---|
Key Method | Physical Vapor Deposition (PVD) |
Advantages | - Dense, uniform coatings |
- Superior wear and corrosion resistance
- Decorative finishes | | Applications | Aerospace, automotive, electronics, medical devices, optical components | | Hybrid Techniques | Combines sputter deposition with PECVD for advanced composites | | Environmental Benefits| Minimal waste, reduced emissions, and eco-friendly processes | | Future Trends | Nanotechnology integration and eco-friendly precursors for advanced coatings|
Ready to enhance your material production with vacuum deposition? Contact us today to learn more!