Sintering is a critical process in manufacturing that transforms powdered materials into dense, strong, and functional components without melting them. It involves heating the material at high temperatures below its melting point in a controlled atmosphere, which bonds the particles together, reduces porosity, and enhances mechanical properties. This process is cost-effective, versatile, and widely used across industries such as metallurgy, ceramics, and glass production. Sintering is essential for creating components like gears, bearings, and electrical contacts, as it ensures the final product has the desired strength, durability, and dimensional accuracy.
Key Points Explained:
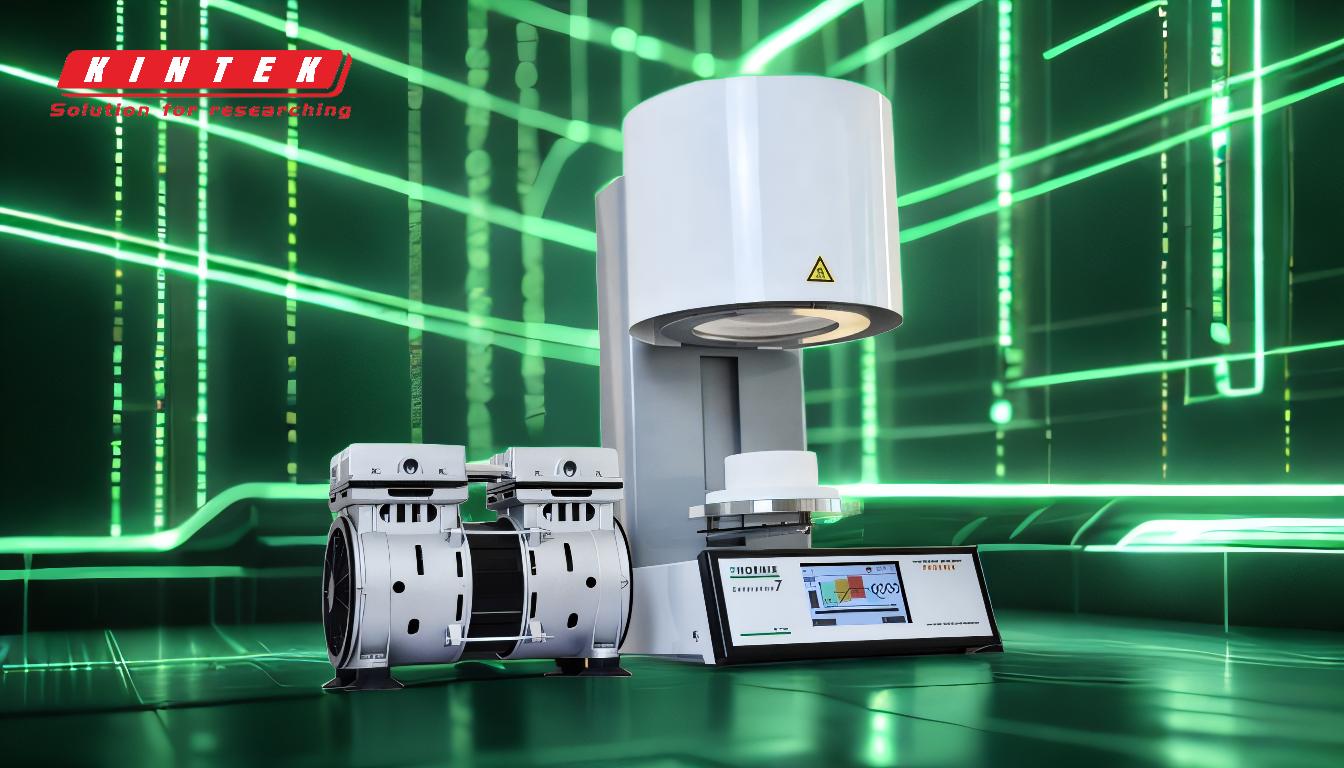
-
Transformation of Powdered Material into a Dense Body:
- Sintering converts loose powdered materials into a solid, dense structure. This is achieved by heating the material below its melting point, allowing the particles to bond through diffusion and atomic migration.
- The process eliminates pores and reduces volume shrinkage, resulting in a compact and uniform structure. This is crucial for achieving the desired mechanical properties and dimensional accuracy in the final product.
-
Bonding of Particles Without Melting:
- Unlike melting, sintering bonds particles together through solid-state diffusion. This ensures that the material retains its original composition and properties while achieving high strength and density.
- The controlled heating process prevents the material from liquefying, which is particularly important for materials with high melting points or those that are difficult to melt uniformly.
-
Enhancement of Mechanical Properties:
- Sintering significantly improves the mechanical properties of materials, such as tensile strength, hardness, and wear resistance. This is due to the elimination of porosity and the formation of strong interparticle bonds.
- The process also allows for minor shrinkage, which is accounted for during the initial compaction stage, ensuring the final product meets precise dimensional requirements.
-
Versatility Across Industries:
- Sintering is used in a wide range of industries, including metallurgy, ceramics, and glass production. It is essential for manufacturing components like gears, bearings, pulleys, and electrical contacts.
- The ability to produce complex shapes and fine-tune material properties makes sintering a preferred method for creating high-performance parts.
-
Cost-Effectiveness and Efficiency:
- Sintering is a cost-effective process because it requires less energy compared to melting and can be performed at lower temperatures. It also minimizes material waste, as the powdered form allows for precise control over the amount of material used.
- The process is highly efficient, enabling the production of large quantities of components with consistent quality.
-
Controlled Atmosphere and Temperature:
- Sintering is performed in a controlled atmosphere furnace to prevent oxidation and ensure proper bonding of particles. The temperature is carefully regulated to be just below the material’s melting point, optimizing the bonding process.
- The cooling rate can be adjusted to further refine the material’s properties, such as hardness and toughness, making sintering a highly customizable process.
-
Applications in Specific Industries:
- In metallurgy, sintering is used to produce iron ore sinter, which is then used in blast furnaces to make steel. This process improves the efficiency of steel production by creating a more uniform and reactive material.
- In ceramics and glass manufacturing, sintering is used to create durable and high-strength products, such as tiles, insulators, and optical components.
By understanding these key points, it becomes clear why sintering is indispensable in modern manufacturing. It not only enhances material properties but also offers a versatile, efficient, and cost-effective solution for producing high-quality components across various industries.
Summary Table:
Key Aspect | Description |
---|---|
Process Overview | Converts powdered materials into dense, durable components without melting. |
Bonding Mechanism | Uses solid-state diffusion to bond particles, retaining material properties. |
Mechanical Properties | Enhances tensile strength, hardness, and wear resistance. |
Industry Applications | Used in metallurgy, ceramics, and glass production for components like gears. |
Cost-Effectiveness | Energy-efficient, minimizes waste, and produces consistent quality. |
Controlled Environment | Performed in controlled atmosphere furnaces to optimize bonding and properties. |
Versatility | Produces complex shapes and fine-tunes material properties for high performance. |
Discover how sintering can enhance your manufacturing process—contact us today for expert guidance!