Hydrogen gas is used in the annealing process due to its unique properties, such as high thermal conductivity, strong deoxidizing capabilities, and its ability to create a reducing atmosphere. These properties make hydrogen an ideal choice for annealing low carbon steels, stainless steels, and other metals. It efficiently transfers heat, prevents oxidation, and promotes surface cleaning by reducing oxides on the material. However, hydrogen must be used carefully, as it can cause decarburization in high carbon steels and hydrogen embrittlement in certain materials. Despite these challenges, hydrogen annealing is widely used for its benefits in achieving high-quality, stress-relieved, and oxidation-free metal components.
Key Points Explained:
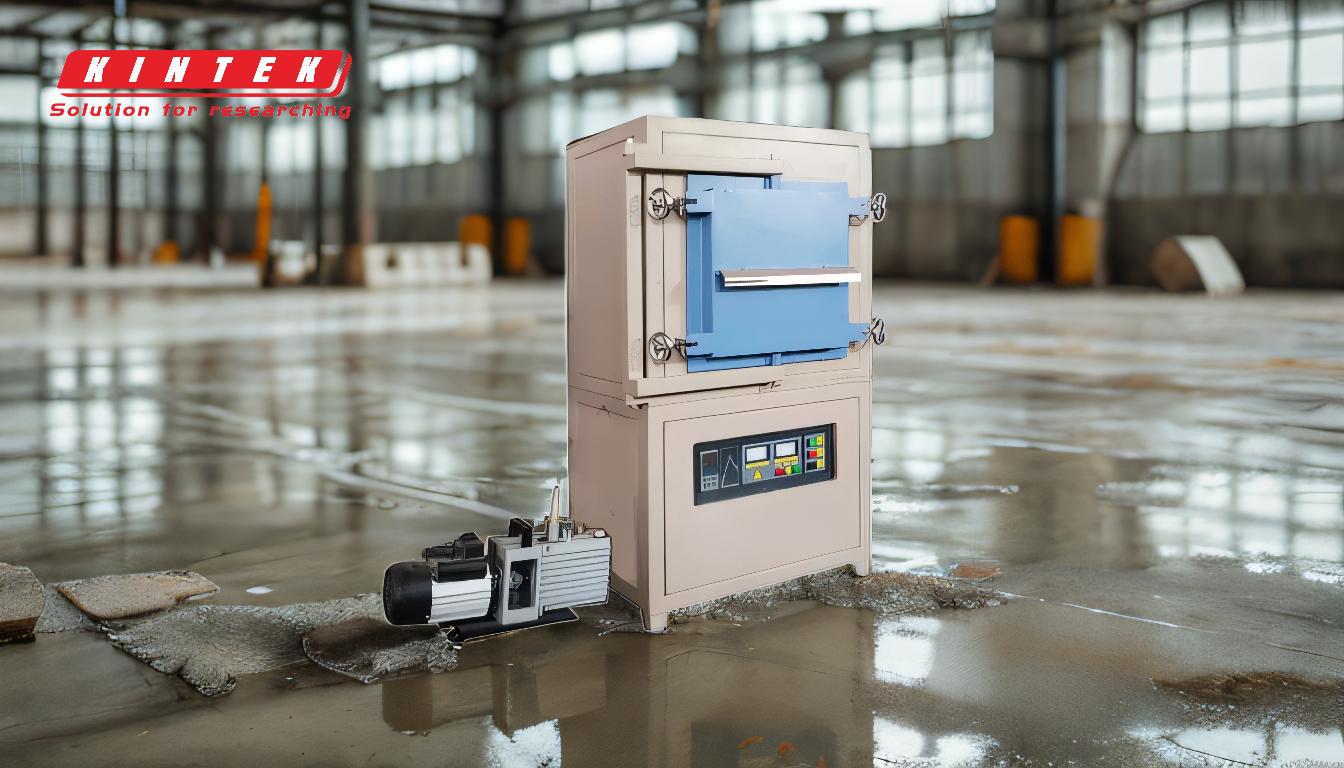
-
High Thermal Conductivity:
- Hydrogen has a heat transfer coefficient seven times higher than air, making it highly efficient for heat transfer during annealing.
- This property ensures uniform heating and cooling of the material, which is critical for achieving consistent mechanical properties and reducing internal stresses.
- For example, in heat treating cast and welded components, hydrogen's thermal conductivity ensures rapid and even heat distribution, improving process efficiency.
-
Deoxidizing and Reducing Properties:
- Hydrogen is a strong deoxidizer, which means it can remove oxygen from the material's surface, preventing oxidation and discoloration.
- It reduces oxides on the material's surface, a process often referred to as "bright annealing," resulting in a clean, shiny finish.
- This is particularly beneficial for stainless steel and magnetic steel alloys, where surface quality is critical.
-
Prevention of Oxidation:
- Using hydrogen in a controlled atmosphere prevents oxidation during the annealing process, ensuring the material retains its desired properties and appearance.
- Oxidation can degrade the material's surface and mechanical properties, making hydrogen's ability to create an oxygen-free environment invaluable.
-
Surface Cleaning and Bright Annealing:
- Hydrogen promotes surface cleaning by reducing oxides, which is essential for applications requiring high surface quality.
- This process is especially important in industries like aerospace and electronics, where surface integrity is paramount.
-
Challenges of Hydrogen Annealing:
- Decarburization: Hydrogen can decarburize high carbon steels at high temperatures, leading to a loss of carbon content and reduced material strength.
- Hydrogen Embrittlement: Hydrogen can diffuse into the material, causing brittleness and cracking, particularly in high-strength steels. Low hydrogen annealing, or "baking," is often used to mitigate this risk by removing hydrogen from the material.
- Cost: Pure hydrogen is more expensive than other annealing atmospheres, though nitrogen-hydrogen blends can be a cost-effective alternative.
-
Applications of Hydrogen Annealing:
- Low Carbon Steels and Stainless Steels: Hydrogen annealing is widely used for these materials due to its ability to prevent oxidation and improve surface quality.
- Magnetic Steel Alloys: Hydrogen annealing enhances the magnetic properties of these alloys by reducing surface oxides and relieving internal stresses.
- Sintering and Powder Metallurgy: Hydrogen is used in sintering tungsten carbide and metal powder components to achieve high-density, high-strength parts.
-
Controlled Atmosphere Requirements:
- Hydrogen annealing requires a controlled atmosphere to ensure the right balance of deoxidizing and reducing effects without causing decarburization or embrittlement.
- The purity of hydrogen (98-99.9%) and the absence of moisture are critical factors in achieving the desired results.
-
Cost-Effective Alternatives:
- While pure hydrogen is effective, it is also expensive. Nitrogen-hydrogen blends are often used as a cost-effective alternative, providing many of the same benefits at a lower cost.
In summary, hydrogen gas is used in annealing due to its superior heat transfer, deoxidizing, and reducing properties. It is particularly effective for low carbon steels, stainless steels, and magnetic alloys, where surface quality and oxidation prevention are critical. However, its use requires careful control to avoid decarburization and hydrogen embrittlement, and cost considerations often lead to the use of nitrogen-hydrogen blends as an alternative.
Summary Table:
Property | Benefits | Challenges |
---|---|---|
High Thermal Conductivity | Efficient heat transfer, uniform heating, and reduced internal stresses. | None |
Deoxidizing Properties | Prevents oxidation, reduces surface oxides, and ensures a clean finish. | None |
Reducing Atmosphere | Creates an oxygen-free environment, preserving material properties. | None |
Surface Cleaning | Promotes bright annealing, essential for high-quality surfaces. | None |
Decarburization | None | Loss of carbon content in high carbon steels, reducing strength. |
Hydrogen Embrittlement | None | Brittleness and cracking in high-strength steels. |
Cost | None | Pure hydrogen is expensive; nitrogen-hydrogen blends are a cost-effective alternative. |
Discover how hydrogen annealing can improve your metal processing—contact our experts today!