Increasing the temperature during forging is a critical aspect of the metalworking process, as it directly impacts the material's properties and the ease of shaping. Forging involves deforming metal into a desired shape using compressive forces, and temperature plays a pivotal role in determining the success of this process. Heating the metal to high temperatures makes it more malleable, reduces the force required for deformation, and minimizes the risk of cracking or failure. Additionally, elevated temperatures allow for better grain structure refinement, which enhances the mechanical properties of the final product. Understanding the reasons for increasing temperature during forging helps optimize the process for both efficiency and quality.
Key Points Explained:
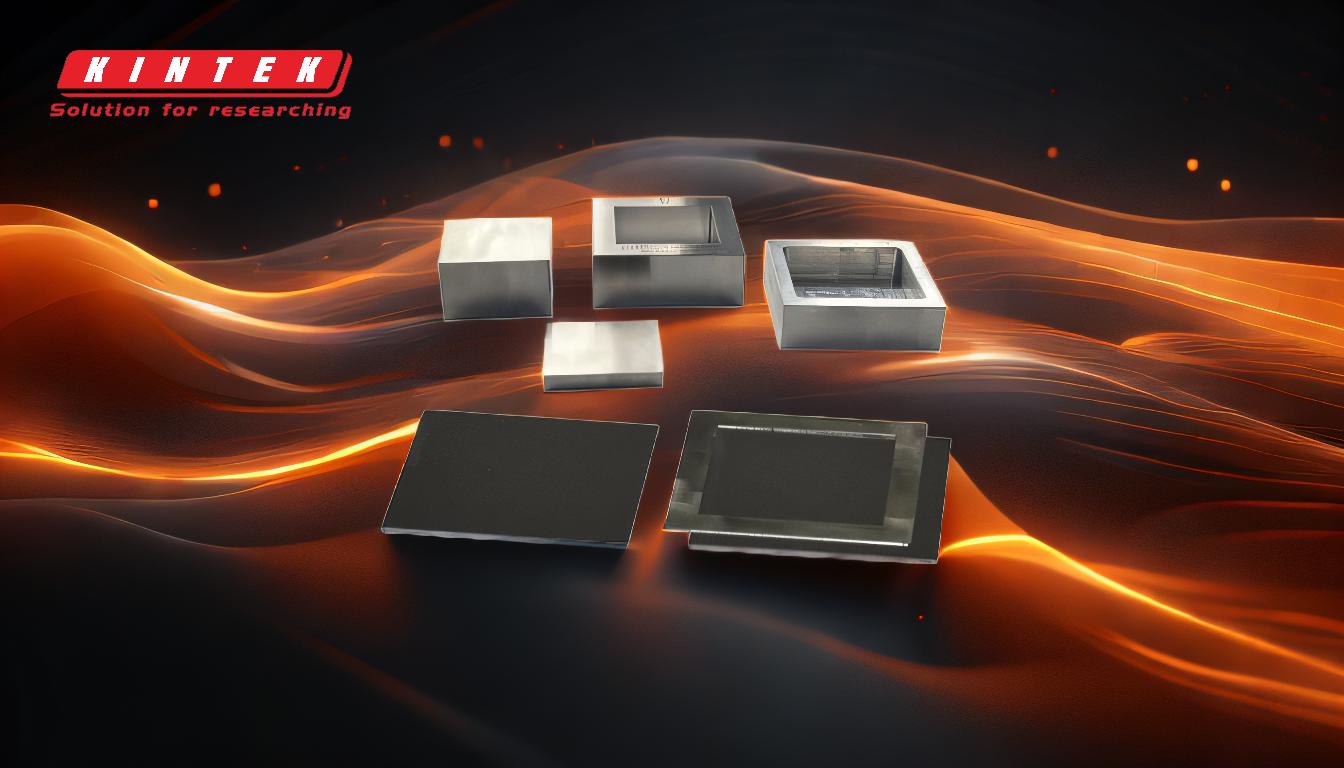
-
Enhanced Malleability and Reduced Force Requirements:
- Metals become more ductile and easier to shape when heated. This is because the thermal energy disrupts the atomic bonds, allowing the metal to deform more easily under pressure.
- At higher temperatures, the yield strength of the metal decreases, meaning less force is needed to achieve the desired deformation. This reduces wear on forging equipment and lowers energy consumption.
-
Prevention of Cracking and Failure:
- Cold forging (forging at or near room temperature) can lead to brittleness and cracking, especially in harder metals. Heating the metal reduces internal stresses and prevents fractures during deformation.
- Elevated temperatures ensure a more uniform distribution of stress throughout the material, minimizing the risk of localized failures.
-
Grain Structure Refinement:
- Heating the metal to its recrystallization temperature allows the grains within the material to reform into a finer, more uniform structure. This improves the mechanical properties of the forged part, such as strength, toughness, and fatigue resistance.
- Proper temperature control during forging ensures that the grain flow follows the contours of the final shape, enhancing the part's durability.
-
Improved Workability of Complex Shapes:
- Higher temperatures enable the metal to flow more easily into intricate molds or dies, making it possible to forge complex geometries with precision.
- This is particularly important for industries like aerospace and automotive, where components often require intricate designs and tight tolerances.
-
Energy Efficiency and Process Optimization:
- While heating requires energy, the overall process becomes more efficient because less mechanical force is needed to shape the metal. This balances the energy input and output, making the process more sustainable.
- Proper temperature management also reduces the number of forging steps required, saving time and resources.
-
Material-Specific Considerations:
- Different metals have varying forging temperature ranges. For example, steel is typically forged at temperatures between 950°C and 1250°C, while aluminum alloys are forged at lower temperatures (around 350°C to 500°C).
- Understanding the specific temperature requirements for each material ensures optimal results and prevents overheating, which can degrade the metal's properties.
-
Impact on Final Product Quality:
- The temperature during forging directly affects the microstructure and mechanical properties of the final product. Proper heating ensures a high-quality finish with minimal defects.
- Consistent temperature control throughout the process is essential to achieve uniformity in the forged part's properties.
In summary, increasing the temperature during forging is essential for improving the metal's workability, preventing defects, and enhancing the final product's mechanical properties. By carefully controlling the temperature, manufacturers can achieve efficient, high-quality forging processes tailored to the specific requirements of the material and the desired outcome.
Summary Table:
Key Benefit | Explanation |
---|---|
Enhanced Malleability | Heating metals makes them more ductile, reducing force needed for deformation. |
Prevents Cracking and Failure | Elevated temperatures reduce internal stresses and prevent fractures. |
Grain Structure Refinement | Improves strength, toughness, and fatigue resistance. |
Improved Workability of Complex Shapes | Enables precise forging of intricate designs. |
Energy Efficiency | Reduces mechanical force requirements, balancing energy input and output. |
Material-Specific Considerations | Different metals have optimal forging temperature ranges for best results. |
Impact on Final Product Quality | Ensures high-quality finish with minimal defects and uniform properties. |
Ready to optimize your forging process? Contact our experts today for tailored solutions!