Induction heating is expensive due to several factors, including the complexity of system design, the need for specialized components like high-capacity power supplies and custom inductor coils, and the advanced technology required to ensure precise and efficient heating. The cost is also influenced by the material properties, such as resistivity and specific heat, as well as the required temperature rise and heat loss considerations. Additionally, the development of advanced semiconductor technology and custom coil designs to improve efficiency further adds to the expense. Below, we break down the key reasons why induction heating systems are costly.
Key Points Explained:
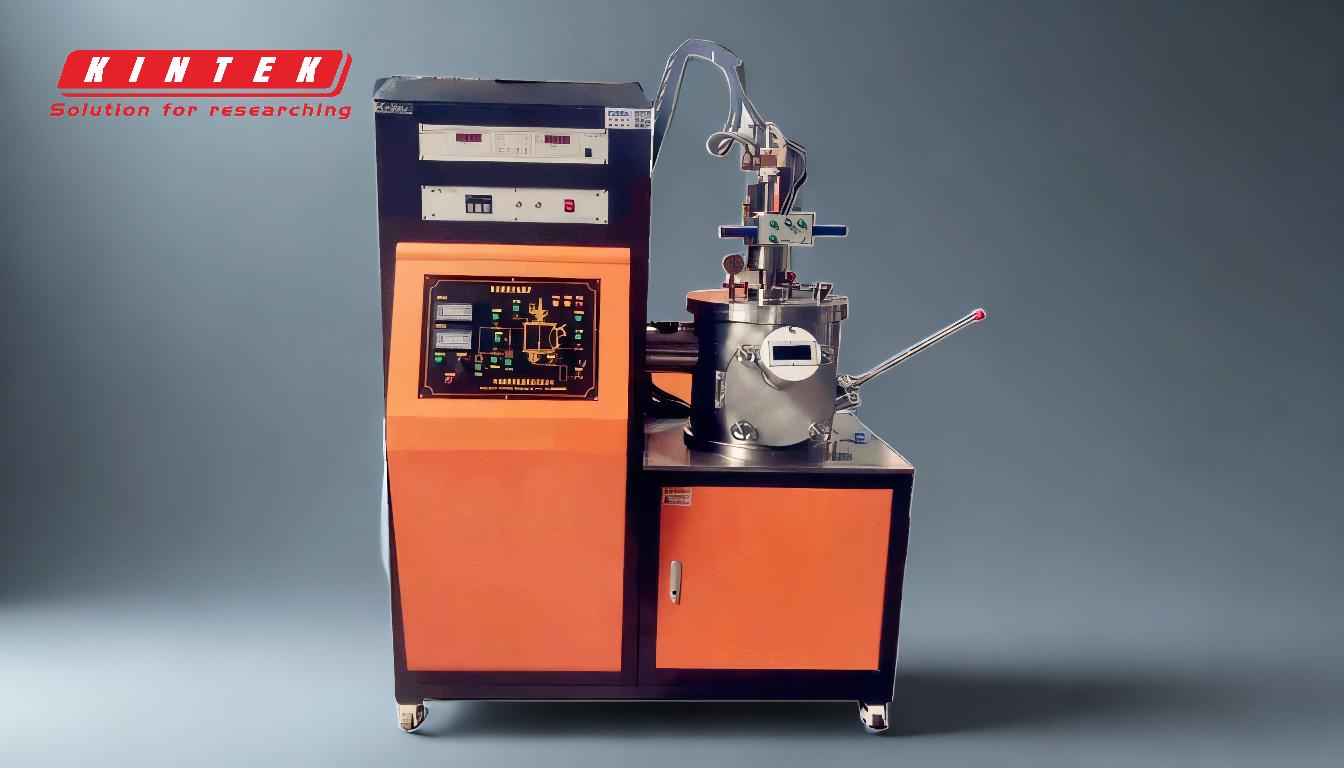
-
Complex System Design:
- Induction heating systems require careful design to match the specific application, including the type of material, size, and thickness of the workpiece. This customization increases costs.
- The design must account for factors like frequency selection, inductor coil geometry, and power supply capacity, which are tailored to the material's properties and heating requirements.
-
Specialized Components:
- High-Capacity Power Supplies: Induction heating systems rely on high-power inverters and transformers to generate the alternating current needed for heating. These components are expensive due to their advanced technology and high energy requirements.
- Custom Inductor Coils: The inductor coil must be designed to match the shape and size of the workpiece, often requiring custom fabrication, which adds to the cost.
-
Material-Specific Considerations:
- The efficiency of induction heating depends on the material's resistivity, specific heat, and thermal conductivity. Materials with higher resistivity heat faster but may require more precise control, increasing system complexity.
- The need to account for heat loss through conduction, convection, and radiation further complicates the design and increases costs.
-
Energy Efficiency and Power Requirements:
- Induction heating systems must deliver precise amounts of energy to achieve the desired temperature rise, which requires advanced control systems and high-efficiency power supplies.
- The power calculation must consider the material's mass, heating time, and productivity, adding to the system's complexity and cost.
-
Technological Advancements:
- Ongoing advancements in semiconductor technology and inductor coil designs aim to improve efficiency and reliability, but these innovations come at a higher cost.
- Specialized coil shapes and designs, such as those for specific heating depths or localized heating, further increase expenses.
-
Precision and Control:
- Induction heating allows for precise control over the heating process, enabling localized heating and specific depth penetration. This precision requires sophisticated control systems and sensors, which are costly.
- Unlike traditional heating methods (e.g., gas furnaces or salt baths), induction heating generates heat directly within the material, necessitating advanced technology to manage the process accurately.
-
Application-Specific Requirements:
- Each application may require unique system configurations, such as varying frequencies for different heating depths or custom inductor coils for complex geometries.
- The need to accommodate a wide range of temperature variations and heating rates adds to the system's complexity and cost.
-
Operational and Maintenance Costs:
- Induction heating systems often require regular maintenance to ensure optimal performance, including coil replacement and power supply servicing.
- The high energy consumption and need for cooling systems further contribute to operational expenses.
In summary, the high cost of induction heating systems stems from their complex design, specialized components, material-specific considerations, and the need for advanced technology to achieve precise and efficient heating. While these systems offer significant advantages in terms of control and efficiency, the associated costs reflect the sophistication and customization required to meet diverse industrial needs.
Summary Table:
Key Factors | Details |
---|---|
Complex System Design | Customization for material, size, and thickness; frequency and coil design. |
Specialized Components | High-capacity power supplies, custom inductor coils. |
Material-Specific Considerations | Resistivity, specific heat, and thermal conductivity impact efficiency. |
Energy Efficiency & Power Needs | Advanced control systems and precise energy delivery. |
Technological Advancements | Advanced semiconductors and custom coil designs. |
Precision & Control | Sophisticated systems for localized heating and depth penetration. |
Application-Specific Requirements | Unique configurations for varying heating depths and geometries. |
Operational & Maintenance Costs | Regular maintenance, high energy consumption, and cooling systems. |
Discover how induction heating can meet your industrial needs—contact our experts today for a tailored solution!