Plasma is used in Chemical Vapor Deposition (CVD) to enhance the process by providing the necessary energy to activate source gases or vapors. This activation generates electrons, ions, and neutral radicals, which dissociate the gas or vapor and allow it to condense on the substrate surface. The use of plasma enables deposition at lower temperatures, which is beneficial for a wider range of substrates and coating materials. Additionally, plasma-assisted CVD improves the quality and durability of the coatings, making it suitable for applications in electronics, semiconductors, and advanced materials like graphene-polymer composites. The process is highly versatile, allowing for precise and complex surface coatings that can withstand extreme conditions.
Key Points Explained:
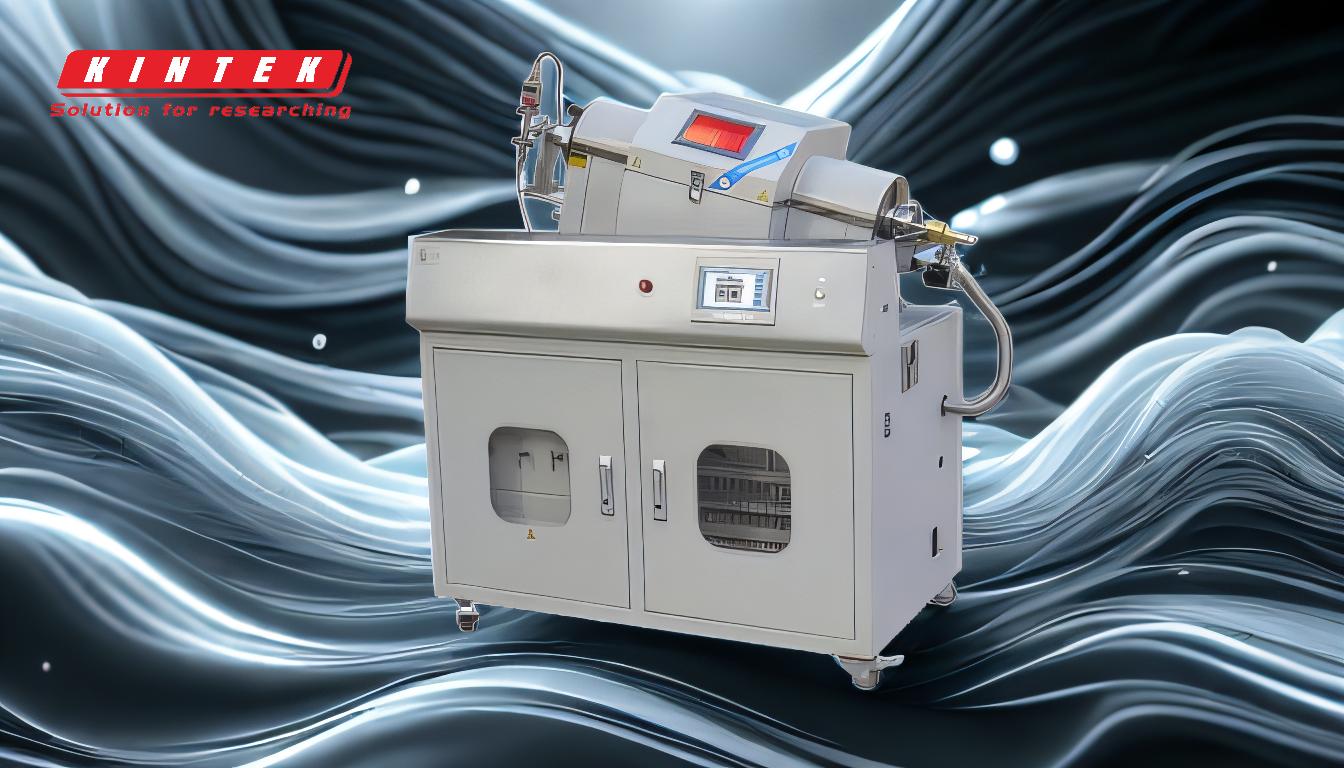
-
Activation of Source Gases or Vapors:
- Plasma provides the energy required to activate the source gases or vapors in the CVD process. This activation generates electrons, ions, and neutral radicals, which are essential for the dissociation of the gas or vapor. This step is crucial as it allows the gas or vapor to break down into reactive species that can then condense on the substrate surface.
-
Lower Temperature Deposition:
- One of the significant advantages of using plasma in CVD is the ability to deposit coatings at lower temperatures. Traditional CVD processes often require high temperatures, which can limit the types of substrates and materials that can be used. Plasma-assisted CVD reduces this temperature requirement, expanding the range of possible substrates and coating materials.
-
Enhanced Coating Quality:
- The use of plasma in CVD improves the quality of the deposited coatings. The reactive species generated by plasma are more uniform and adhere better to the substrate, resulting in coatings that are more durable and resistant to wear and corrosion. This is particularly important for applications in high-stress environments, such as electronics and semiconductors.
-
Versatility in Applications:
- Plasma-assisted CVD is highly versatile and can be used to coat a wide range of materials, including ceramics, metals, and glass. This versatility makes it suitable for various industrial applications, from electronic components to advanced materials like graphene-polymer composites. The ability to optimize gases for specific properties, such as corrosion resistance or high purity, further enhances its applicability.
-
Complex and Precision Coatings:
- The precision and complexity of the coatings that can be achieved with plasma-assisted CVD are unparalleled. The process allows for the deposition of thin films on intricate and complex surfaces, which is essential for manufacturing precision components in electronics and other high-tech industries. The coatings maintain their integrity even when exposed to extreme temperatures or temperature variations.
-
Improved Product Cycle in Electronics:
- The application of plasma-assisted CVD in the electronics industry leads to an enhanced product cycle. Components such as integrated circuits, semiconductors, capacitors, and resistors benefit from the durable and high-quality coatings provided by this process. This results in longer-lasting and more reliable electronic devices.
In summary, plasma is used in CVD to enhance the activation of source gases, enable lower temperature deposition, improve coating quality, and provide versatility and precision in coating applications. These benefits make plasma-assisted CVD a critical process in industries ranging from electronics to advanced materials.
Summary Table:
Key Benefit | Description |
---|---|
Activation of Source Gases | Plasma generates electrons, ions, and radicals to dissociate gases for deposition. |
Lower Temperature Deposition | Enables deposition at reduced temperatures, expanding substrate and material options. |
Enhanced Coating Quality | Produces uniform, durable coatings resistant to wear and corrosion. |
Versatility in Applications | Suitable for ceramics, metals, glass, and advanced materials like graphene-polymer composites. |
Precision Coatings | Allows thin film deposition on complex surfaces, ideal for electronics and high-tech industries. |
Improved Product Cycle | Enhances durability and reliability of electronic components like semiconductors and capacitors. |
Learn how plasma-assisted CVD can optimize your processes—contact our experts today!