Sintering is a critical process in powder metallurgy and ceramics, where powdered materials are compacted and heated to form a solid structure. The pressing force applied during the initial compaction stage plays a vital role in determining the final properties of the sintered product. It influences the density, strength, and uniformity of the material, as well as the efficiency of the sintering process. Understanding the importance of pressing force helps optimize the sintering process for desired outcomes, such as improved mechanical properties, reduced porosity, and enhanced dimensional accuracy.
Key Points Explained:
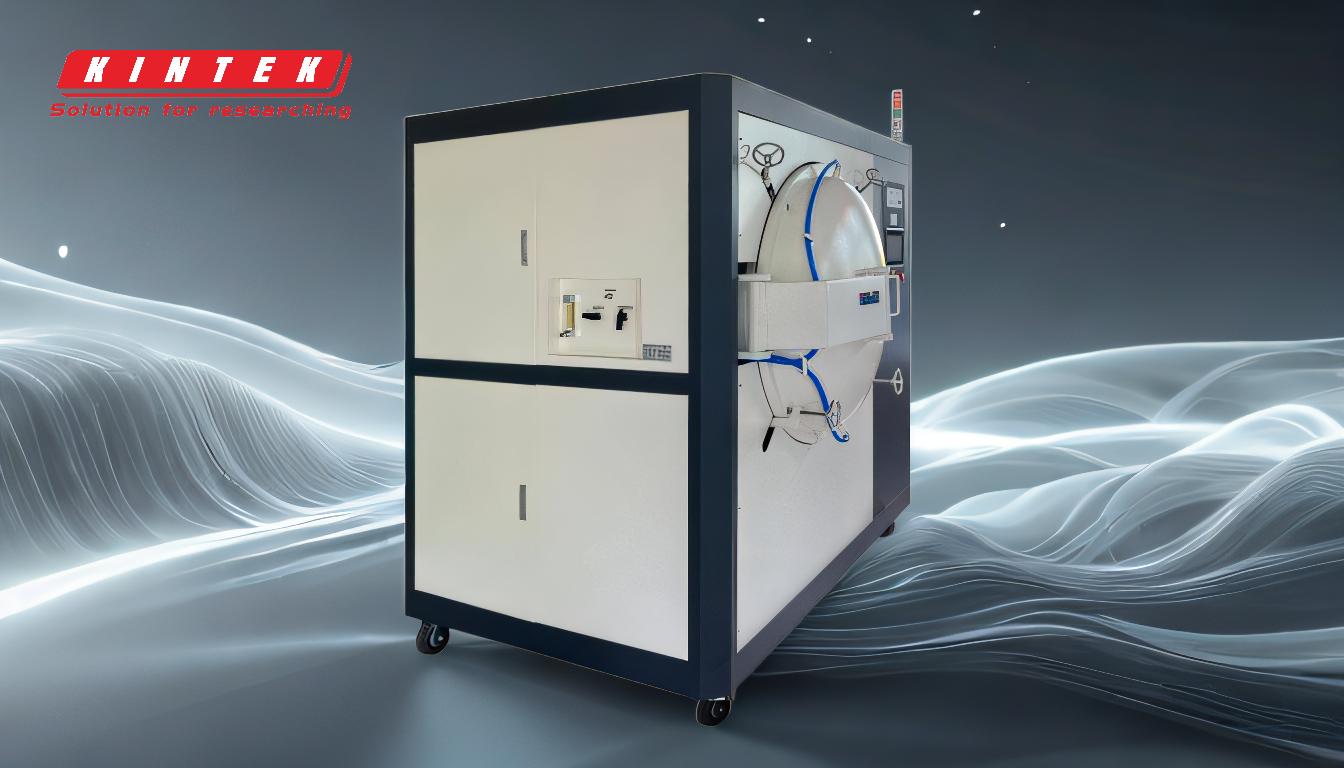
-
Influence on Green Density:
- The pressing force directly affects the green density of the compacted powder before sintering. Higher pressing forces result in a more densely packed powder, reducing the voids between particles.
- A higher green density leads to better particle-to-particle contact, which facilitates diffusion and bonding during the sintering process.
- Insufficient pressing force can result in a porous structure, leading to weak mechanical properties and uneven shrinkage during sintering.
-
Impact on Sintering Efficiency:
- Proper pressing force ensures uniform compaction, which is essential for consistent heat transfer and diffusion during sintering.
- Uneven compaction can cause localized overheating or underheating, leading to defects such as warping, cracking, or incomplete sintering.
- Optimized pressing force minimizes the energy required for sintering by reducing the need for excessive heating to achieve full densification.
-
Effect on Final Product Properties:
- The mechanical properties of the sintered product, such as hardness, tensile strength, and wear resistance, are heavily influenced by the initial pressing force.
- A well-compacted green body ensures a homogeneous microstructure after sintering, which enhances the overall performance of the material.
- Inadequate pressing force can result in residual porosity, which weakens the material and reduces its durability.
-
Dimensional Control:
- Pressing force affects the dimensional accuracy of the final product. Proper compaction minimizes shrinkage and distortion during sintering.
- Consistent pressing force ensures uniform shrinkage, which is critical for achieving tight tolerances in precision components.
- Variations in pressing force can lead to unpredictable dimensional changes, making it difficult to meet design specifications.
-
Material-Specific Considerations:
- Different materials require different pressing forces based on their particle size, shape, and flow characteristics.
- Harder materials, such as ceramics, often require higher pressing forces to achieve sufficient compaction, while softer materials may need lower forces to avoid cracking.
- Understanding the material properties is essential for selecting the appropriate pressing force to achieve optimal results.
-
Process Optimization:
- The pressing force must be carefully calibrated to balance compaction and avoid over-pressing, which can lead to stress concentrations and defects.
- Advanced techniques, such as isostatic pressing, can provide more uniform compaction compared to uniaxial pressing, especially for complex shapes.
- Continuous monitoring and adjustment of pressing force during production ensure consistent quality and reduce waste.
In summary, pressing force is a critical parameter in sintering that influences the green density, sintering efficiency, final product properties, dimensional control, and overall process optimization. By carefully selecting and controlling the pressing force, manufacturers can achieve high-quality sintered products with desirable mechanical and dimensional characteristics.
Summary Table:
Key Aspect | Impact of Pressing Force |
---|---|
Green Density | Higher force increases density, reduces voids, and improves particle bonding. |
Sintering Efficiency | Ensures uniform compaction, consistent heat transfer, and minimizes energy requirements. |
Final Product Properties | Enhances hardness, tensile strength, and wear resistance; reduces porosity and defects. |
Dimensional Control | Minimizes shrinkage, distortion, and ensures tight tolerances for precision components. |
Material-Specific Needs | Harder materials require higher force; softer materials need lower force to avoid cracking. |
Process Optimization | Balances compaction, avoids over-pressing, and ensures consistent quality with less waste. |
Optimize your sintering process with expert guidance—contact us today to learn more!