The atmosphere in a furnace is crucial because it directly influences the chemical and physical properties of the materials being treated. It can either protect materials from unwanted surface reactions or facilitate specific chemical changes, such as hardening or carburizing. Proper control of the furnace atmosphere ensures uniform temperature distribution, prevents contamination, and achieves the desired material properties. Additionally, the atmosphere can act as a thermal conductor, transferring heat efficiently to the workpiece. Monitoring and controlling the furnace atmosphere are essential for ensuring the quality and specifications of the treated materials, making it a critical factor in industrial processes like heat treatment.
Key Points Explained:
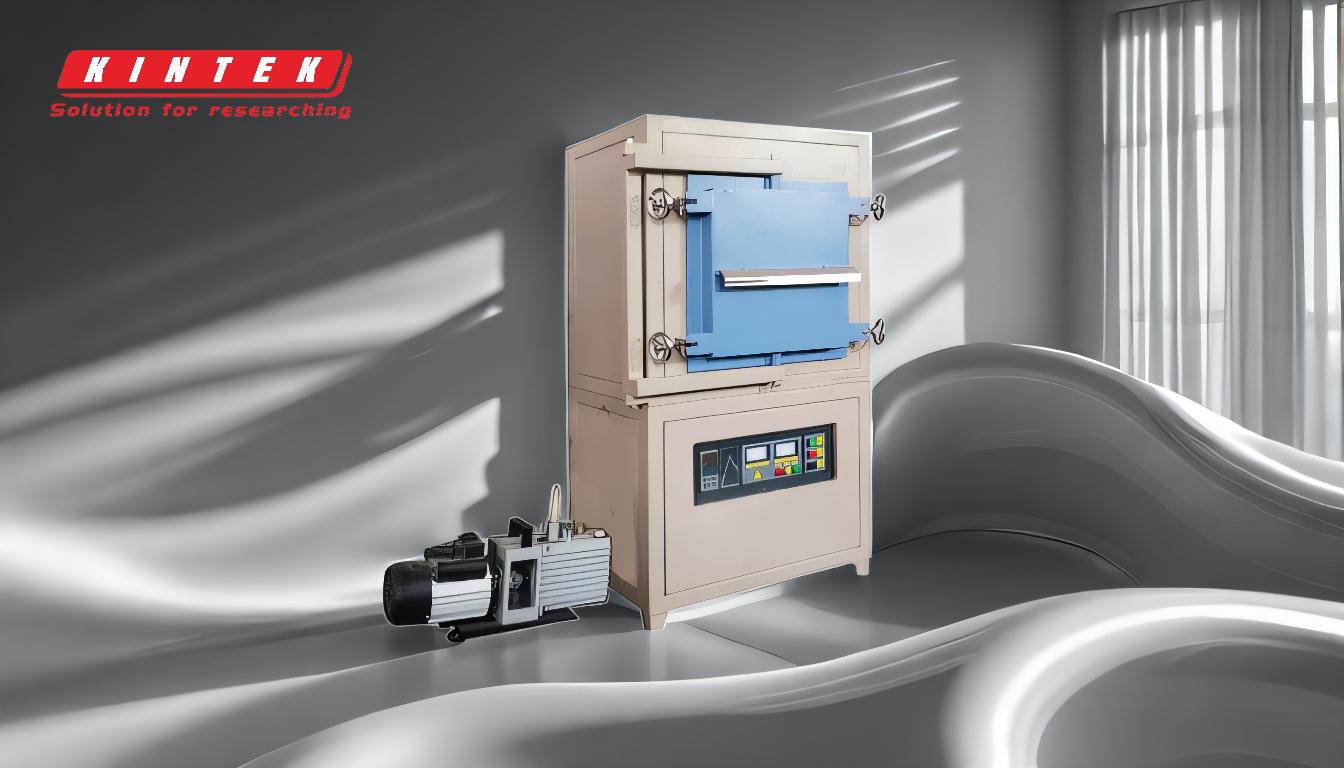
-
Chemical Reaction Control:
- The furnace atmosphere can either encourage or prevent chemical reactions on the surface of the material. For example:
- Reactive Atmospheres: Used in processes like carburizing, where the atmosphere introduces carbon to the surface of the metal to harden it.
- Inert Atmospheres: Protect materials from oxidation or other harmful reactions, preserving their integrity.
- Without proper control, unwanted reactions (e.g., oxidation, decarburization) can render the parts unsuitable for their intended purpose.
- The furnace atmosphere can either encourage or prevent chemical reactions on the surface of the material. For example:
-
Material Protection and Surface Modification:
- The atmosphere can act as a protective barrier, preventing harmful elements like oxygen or moisture from reacting with the material.
- Alternatively, it can facilitate surface changes, such as the formation of protective coatings or the introduction of specific elements to alter material properties.
-
Thermal Conduction and Uniform Heating:
- The furnace atmosphere can function as a thermal conductor, transferring heat from the furnace walls to the workpiece. This ensures uniform temperature distribution within the chamber, which is critical for consistent material properties.
- Proper airflow and temperature control are essential to avoid hot or cold spots that could lead to uneven treatment.
-
Facilitation of Specific Processes:
- Different furnace atmospheres are required for specific heat treatment processes. For example:
- Carburizing: Requires a carbon-rich atmosphere to harden the surface of steel.
- Annealing: Often uses inert gases like nitrogen or argon to prevent oxidation.
- The ability to replace the atmosphere with a second gaseous medium allows for the creation of specialized surface finishes or chemical alterations.
- Different furnace atmospheres are required for specific heat treatment processes. For example:
-
Quality Assurance and Process Control:
- Proper monitoring and control of the furnace atmosphere ensure that the desired chemical reactions occur correctly, meeting the required specifications for the treated materials.
- This is especially important in industries where material performance is critical, such as aerospace, automotive, and tool manufacturing.
-
Impact on Final Product Properties:
- The furnace atmosphere directly impacts the mechanical properties (e.g., hardness, strength, ductility) and surface characteristics (e.g., corrosion resistance, wear resistance) of the treated materials.
- A well-controlled atmosphere ensures that the final product meets the necessary standards and performs reliably in its intended application.
By understanding and controlling the furnace atmosphere, manufacturers can achieve precise and repeatable results, ensuring the quality and performance of the treated materials. This makes the furnace atmosphere a critical factor in industrial heat treatment processes.
Summary Table:
Key Aspect | Role in Furnace Atmosphere |
---|---|
Chemical Reaction Control | Encourages or prevents surface reactions (e.g., carburizing, oxidation prevention). |
Material Protection | Acts as a barrier against harmful elements like oxygen or moisture. |
Thermal Conduction | Ensures uniform heat distribution, preventing hot or cold spots. |
Process Facilitation | Enables specific treatments like carburizing or annealing with tailored atmospheres. |
Quality Assurance | Ensures consistent material properties and adherence to specifications. |
Final Product Properties | Directly impacts hardness, strength, corrosion resistance, and wear resistance of materials. |
Optimize your heat treatment processes with precise furnace atmosphere control—contact our experts today!