Introduction
Isostatic pressing is an essential technique in the manufacturing industry, used for shaping and consolidating materials. It involves subjecting a material to uniform pressure from all directions, resulting in enhanced density and improved mechanical properties. Isostatic pressing is widely employed in various industries, including aerospace, automotive, and healthcare, due to its ability to produce complex and high-quality components. Understanding the different types and applications of isostatic pressing techniques is crucial for businesses seeking to optimize their manufacturing processes and achieve superior product outcomes. In this blog post, we will delve into the comprehensive analysis of isostatic pressing techniques, exploring their definitions, features, and advantages in detail.
Understanding Isostatic Pressing
Definition of Isostatic Pressing
Isostatic pressing is a powder processing technique that involves applying equal pressure in all directions to a material, typically a powder compact. This process is used to increase the density and achieve the required shapes of products under high pressure.
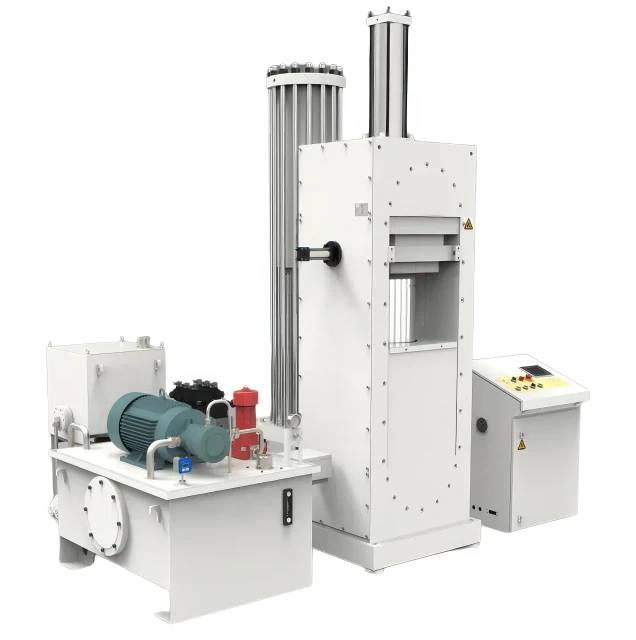
The isostatic pressing process works by placing the products in a closed container filled with liquid and applying equal pressure to each surface. This pressure is transmitted through the medium to the powder, resulting in uniform compaction and consolidation.
Key Features of Isostatic Pressing
-
Alternative Processes: Isostatic pressing is a unique powder processing technique that uses fluid pressure to compact the part. Unlike other processes that exert forces on the powder through an axis, isostatic pressing utilizes all-around pressure.
-
Working of Isostatic Press: Isostatic pressing enables the production of various types of materials from powder compacts by reducing their porosity. The powder mixture is compacted and encapsulated using isostatic pressure, which is pressure equally applied from all directions. This confinement of the metal powder within a flexible membrane or hermetic container allows for uniform pressurization.
-
Isostatic Forming Technology: Isostatic forming involves placing the powder specimen to be pressed in a high-pressure container and using the incompressible nature of the liquid or gas medium to uniformly pressurize the specimen. This technology provides isotropic, ultra-high molding pressure for products. Depending on the molding temperature, isostatic pressing can be categorized as hot isostatic pressing (HIP), warm isostatic pressing (WIP), or cold isostatic pressing (CIP).
-
Differences from Uniaxial Pressing: Isostatic pressing shares similarities with uniaxial pressing in terms of powder requirements and general process steps. However, there are important differences. Isostatic pressing takes place under hydrostatic conditions, where the pressure is transmitted equally in all directions. This reduces or eliminates die wall friction. Additionally, the tooling consists of elastomeric molds instead of rigid dies, allowing for flexibility and ease of pressure application.
-
Global Isostatic Pressing Market Introduction: Isostatic pressing is a manufacturing process that achieves maximum uniformity of density and microstructure without the geometrical limitations of uniaxial pressing. It involves subjecting a material to high pressure in a sealed container filled with a fluid or gas medium. This pressure is evenly distributed, resulting in uniform compaction and consolidation.
Isostatic pressing can be performed in different temperature conditions. Cold isostatic pressing (CIP) is used for compact green parts at ambient temperatures, warm isostatic pressing (WIP) is used for shaping and pressing material at a warm temperature, and hot isostatic pressing (HIP) is used for fully consolidated parts at elevated temperatures through solid-state diffusion.
Isostatic pressing offers the advantage of uniform pressure distribution, leading to improved product performance and density distribution. This technique is widely used in various industries, including high-temperature refractory, ceramics, cemented carbide, lanthanon permanent magnet, carbon material, and rare metal powder.
Different Types of Isostatic Pressing
Isostatic pressing refers to a powder metallurgy (PM) procedure that evenly presses a powder compact in all directions to provide the greatest possible uniformity of density and microstructure without the geometrical restrictions of uniaxial pressing.
Isostatic Cold Pressing
Cold isostatic presses are generally used in room temperature environments and are suitable for temperature-sensitive materials such as ceramics and metal powders. This type of isostatic pressing involves the compaction of powders encased in elastomer molds. Cold isostatic pressing can improve the density, structure, and properties of materials.
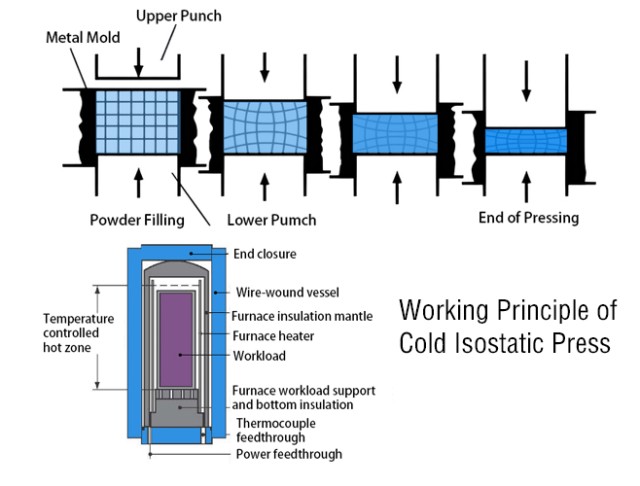
Isostatic Warm Pressing
Warm isostatic presses work at medium temperatures and are suitable for materials with certain temperature requirements, such as plastics and rubber. They operate by heating the gas to a specific temperature and applying a uniform pressure to the material through a closed vessel. Warm isostatic pressing can enhance the density, structure, and properties of materials.
Isostatic Hot Pressing
Hot isostatic pressing (HIP) is a process that compresses materials under high temperatures and pressure. It improves the mechanical properties of castings by eliminating internal microporosity. Hot isostatic pressing can be performed through wet bag pressing or dry bag pressing methods. It is commonly used in industries such as manufacturing, automotive, electronics and semiconductor, medical, aerospace and defense, energy and power, research and development, and others.
Isostatic pressing works by confining the metal powder within a flexible membrane or hermetic container, which acts as a pressure barrier between the powder and the pressurizing medium, whether it's a liquid or gas. The high-pressure gas or liquid is applied equally from all directions, ensuring uniform compaction of the powder mixture.
The decision between cold, warm, or hot isostatic pressing depends on the specific goals of your project and the characteristics of the materials involved. Cold isostatic pressing is suitable for temperature-sensitive materials, warm isostatic pressing is ideal for materials with certain temperature requirements, and hot isostatic pressing is used for materials with high-temperature requirements.
In summary, different types of isostatic pressing offer distinct approaches to materials processing, each with its own advantages. By choosing the appropriate type of isostatic pressing for your project, you can achieve optimal density and microstructure uniformity in your materials.
Isostatic Cold Pressing
Process of Isostatic Cold Pressing
Isostatic cold pressing, also known as cold isostatic pressing (CIP), is a manufacturing process used to create products with more uniform properties and precise dimensions. In this process, a mold made from an elastomer material such as urethane, rubber, or polyvinyl chloride is filled with powder material. The mold is then placed in a chamber filled with a working fluid, typically oil or water, and pressurized using an external pump. The pressure is applied uniformly over the entire surface of the mold, resulting in improved compaction of the powder and densification of the finished product.
Subtypes: Dry Bag and Wet Bag Isostatic Pressing
Isostatic cold pressing can be further divided into two subtypes: dry bag isostatic pressing and wet bag isostatic pressing.
Dry Bag Isostatic Pressing
In dry bag isostatic pressing, the powder material is directly pressed into a fixed forming die (sleeve) inside the high-pressure cylinder. This process is suitable for mass production of simple shapes and parts and is convenient for automation.
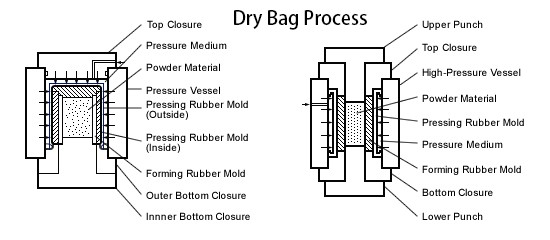
Wet Bag Isostatic Pressing
In wet bag isostatic pressing, the powder material is enclosed in a flexible mold bag, which is then submerged in a high-pressure liquid in a pressure vessel. Isostatic pressure is applied to the outer surfaces of the mold to compress the powder into a desired shape. Wet bag isostatic pressing offers strong adaptability, the ability to produce multiple shapes in one high-pressure cylinder, and is ideal for small batch production and the production of large and complex parts.
Advantages of Each Subtype
Both dry bag and wet bag isostatic pressing offer several advantages over traditional uniaxial pressing methods.
Dry Bag Isostatic Pressing Advantages
- More uniform product properties and greater homogeneity
- Greater flexibility in the shape and size of the finished product
- Longer aspect ratios possible, allowing for the production of long thin pellets
- Ability to process materials with different characteristics and shapes
- Reduced cycle times and improved productivity
Wet Bag Isostatic Pressing Advantages
- Ideal for multi-shape and small to large quantity production
- Ability to press large and complex parts
- Shorter production process and lower cost compared to other methods
- Strong applicability and suitability for experimental research
Wet bag process
In summary, isostatic cold pressing offers numerous advantages in terms of product properties, flexibility, and productivity. The choice between dry bag and wet bag isostatic pressing depends on the specific requirements of the production process, such as the shape and quantity of the parts to be produced.
Isostatic Warm Pressing
Isostatic warm pressing (IWP) is a variant of cold isostatic pressing (CIP) that involves the use of a heating element. It utilizes warm water or a similar medium to apply uniform pressure to powdered products from all directions. This cutting-edge technology allows for isostatic pressing at a temperature that does not exceed the boiling point of the liquid medium.
Applications of Isostatic Warm Pressing
Isostatic warm pressing has various applications across different industries. Some of the key applications include:
-
Metal Powder Compaction: Isostatic warm pressing is commonly used in the manufacturing of metal parts through powder compaction. It allows for the production of complex shapes and high-density components with improved mechanical properties.
-
Ceramic and Composite Materials: IWP is also utilized in the production of ceramic and composite materials. This process helps in achieving uniform compaction and high-density structures, resulting in improved material properties such as strength, toughness, and thermal conductivity.
-
Medical and Dental Implants: Isostatic warm pressing is employed in the production of medical and dental implants. The process allows for the fabrication of intricate and customized shapes with high precision and mechanical strength.
-
Electronics and Semiconductor Components: IWP is used in the manufacturing of electronics and semiconductor components. It enables the production of parts with precise dimensions, high density, and excellent electrical properties.
Application of isostatic pressure and temperature pressure(Ceramics, dental implants, metal powder pressing, electronic and semiconductor components)
Benefits of Isostatic Warm Pressing
Isostatic warm pressing offers several advantages over traditional pressing methods. Some of the key benefits include:
-
Uniform Pressure Distribution: The use of warm water or a similar medium ensures that pressure is applied uniformly from all directions. This results in uniform compaction and eliminates the formation of voids or defects in the pressed material.
-
Improved Material Properties: Isostatic warm pressing allows for the production of high-density components with enhanced mechanical and physical properties. The uniform pressure distribution helps in achieving consistent material properties throughout the pressed part.
-
Complex Shape Formation: IWP enables the fabrication of complex shapes that are difficult to achieve using traditional pressing methods. The flexibility of the jacket mold and the uniform pressure application make it possible to produce intricate and customized parts.
-
High Precision and Accuracy: Isostatic warm pressing ensures high precision and accuracy in the fabrication of parts. The controlled temperature and pressure parameters result in consistent dimensions and tight tolerances.
In conclusion, isostatic warm pressing is a valuable technology that finds applications in various industries. It offers benefits such as uniform pressure distribution, improved material properties, complex shape formation, and high precision. This process is instrumental in the production of high-quality components with enhanced mechanical and physical properties.
Isostatic Hot Pressing
Understanding Isostatic Hot Pressing
Hot isostatic pressing (HIP) is a manufacturing process that utilizes elevated temperature and isostatic gas pressure to eliminate porosity and increase density in metals, ceramics, polymers, and composite materials. This process improves the material's mechanical properties and workability. HIP is commonly used for the elimination of microshrinkage in castings, powder consolidation, diffusion bonding, sintering, pressure-assisted brazing, and fabrication of metal matrix composites.
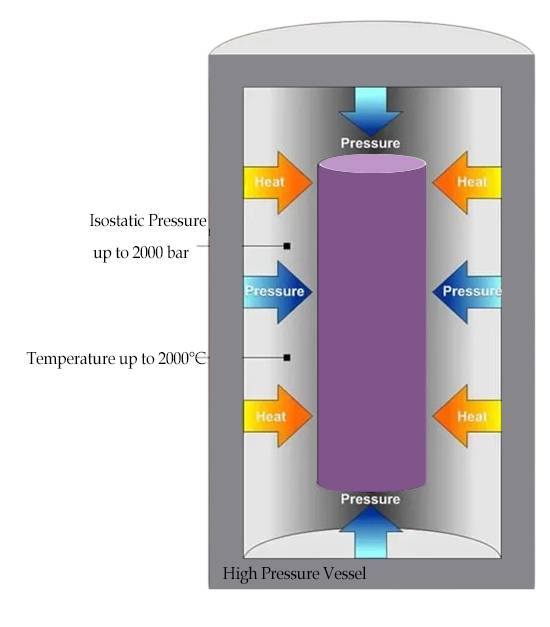
Working Medium and Sheathing Materials
Isostatic hot pressing applies equal force over the entire product, regardless of shape or size. The process involves using a gas or liquid as the working medium to deliver force to a hermetically sealed container filled with the material powder. The container is then subjected to elevated temperatures. The working medium ensures that the pressure is evenly distributed, allowing for uniform compaction and consolidation of the material. Common working mediums include argon gas and oil.
Applications of Isostatic Hot Pressing
Isostatic hot pressing technology finds applications in various industries, including castings, powder metallurgy, ceramics, porous materials, near-net forming, material bonding, plasma spraying, and the manufacture of high-end graphite. The ability to apply equal pressure in all directions makes isostatic hot pressing particularly beneficial for ceramic and refractory applications. It enables the formation of product shapes with precise tolerances, reducing the need for costly machining.
Isostatic hot pressing is a versatile manufacturing process that offers numerous benefits in terms of material density, microstructure uniformity, and mechanical properties. It is widely used in industries requiring high-quality, defect-free materials.
Conclusion
In conclusion, isostatic pressing techniques offer a wide range of benefits for various industries. The ability to apply uniform pressure in all directions ensures consistent and high-quality results. Isostatic cold pressing, with its dry bag and wet bag subtypes, provides flexibility and precision in shaping materials. Isostatic warm pressing is ideal for applications that require improved strength and density. Isostatic hot pressing, on the other hand, offers the highest level of compaction and is commonly used for manufacturing ceramics and composites. By understanding the different types of isostatic pressing and their applications, businesses can make informed decisions to enhance their production processes.
If you are interested in this product you can browse our company website:https://kindle-tech.com/product-categories/isostatic-press, we always insist on the principle of quality first. During the production process, we strictly control every step of the process, using high quality materials and advanced production technology to ensure the stability and durability of our products. to ensure that their performance meets the highest standards. We believe that only by providing customers with excellent quality can we win their trust and long-term cooperation.
CONTACT US FOR A FREE CONSULTATION
KINTEK LAB SOLUTION's products and services have been recognized by customers around the world. Our staff will be happy to assist with any inquiry you might have. Contact us for a free consultation and talk to a product specialist to find the most suitable solution for your application needs!