Understanding Isostatic Pressing
Table of Contents
- Understanding Isostatic Pressing
- Advantages of Isostatic Pressing Over Press and Sinter Method
- The Role of Metal Powder Properties in Successful Isostatic Pressing
- The Importance of Material Characterization in Isostatic Pressing
- The influence of spherical powders and particle size distribution on HIP
- The impact of particle irregularity on CIP
- The effect of phase composition and grain size on powder hardness and melt properties
- The relevance of pressing efficiency, sintering behavior, and mechanical properties of the pressed part
- The necessity of compliance with the alloy composition of the specified material
Explanation of Isostatic Pressing
Isostatic pressing is a process used to produce various types of materials from powder compacts by reducing their porosity. It involves applying pressure equally from all directions, confining the metal powder within a flexible membrane or hermetic container. This pressure barrier, whether it be a liquid or gas, surrounds the powder and helps to reduce porosity.
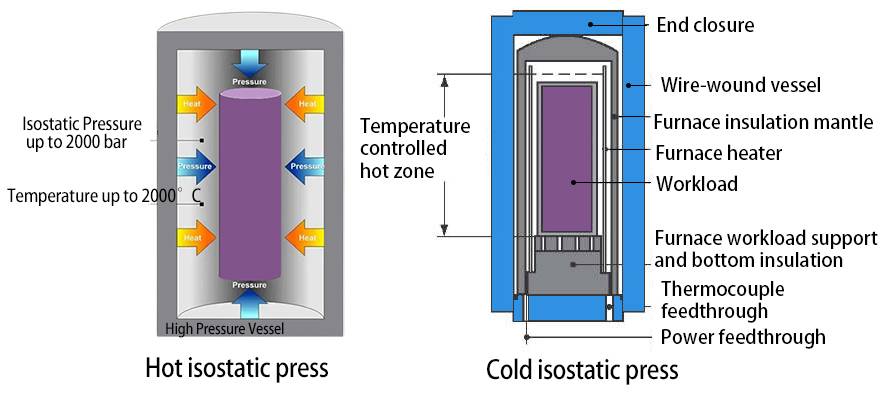
Difference between Hot Isostatic Pressing (HIP) and Cold Isostatic Pressing (CIP)
In the realm of materials processing, two powerful techniques stand out: Cold Isostatic Pressing (CIP) and Hot Isostatic Pressing (HIP). While both methods aim to enhance material properties, they do so under different conditions, each offering unique advantages.
Cold Isostatic Pressing (CIP): Cold Isostatic Pressing involves subjecting a material to uniform pressure from all sides by immersing it in a high-pressure fluid medium and applying hydraulic pressure. CIP is particularly effective for shaping and consolidating powdered materials, creating intricate shapes and achieving high green density.
Hot Isostatic Pressing (HIP): Hot Isostatic Pressing takes the process a step further by combining high pressure with elevated temperatures. It subjects a material to simultaneous high pressure and high temperature within a high-pressure chamber. HIP is used to densify materials, eliminate defects, and enhance properties through diffusion and consolidation. It is especially valuable for materials requiring improved structural integrity, reduced porosity, and higher mechanical properties.
Usage of Hot Isostatic Pressing in Manufacturing Metal Components
Hot Isostatic Pressing (HIP) is widely used in the manufacturing industry for producing metal components. It is commonly employed in applications and industries such as automotive, aerospace, military, heavy equipment, industrial machinery, marine, oil and gas, and medical.
The process involves loading the components into the HIP equipment's chamber, which can vary in size depending on the application. Once loaded, computers take control of the process, programming the equipment to produce the desired results. The user can control parameters such as temperature ramp-up, pressure, and time duration.
Hot isostatic pressing helps solve technical and mechanical problems that would be difficult to correct using other methods. It eliminates porosity, increases density, and improves the mechanical properties of the metal components. This results in higher quality and more reliable parts for various industrial applications.
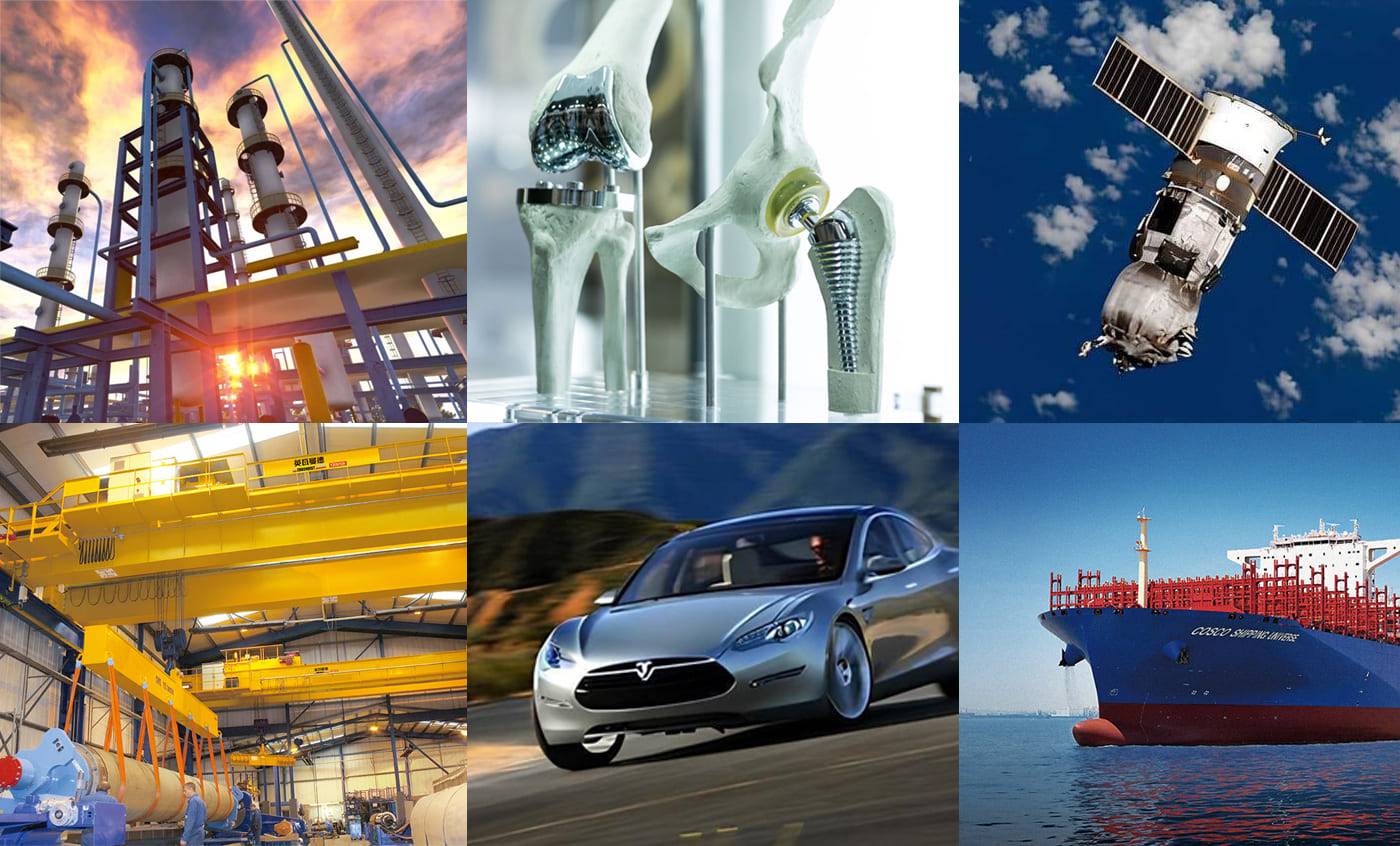
In summary, understanding isostatic pressing is crucial in the manufacturing industry, especially when it comes to hot isostatic pressing. The process provides numerous advantages, such as densifying materials, eliminating defects, and enhancing properties. By utilizing hot isostatic pressing equipment, manufacturers can produce high-quality metal components with improved mechanical properties and structural integrity.
Advantages of Isostatic Pressing Over Press and Sinter Method
Isostatic pressing has several advantages over the commonly used press and sinter method. Let's take a closer look at two key advantages:
Equal compaction in all directions
In isostatic pressing, powder is compacted with the same pressure in all directions. This is achieved by using pressure equally applied from all sides. Unlike the press and sinter method, no lubricant is needed in isostatic pressing, allowing for high and uniform density to be achieved in the final component.
This equal compaction in all directions removes many of the constraints that limit the geometry of parts compacted unidirectionally in rigid dies. It offers shape flexibility, making it practical to produce shapes and dimensions that are difficult or impossible to produce by other methods. Isostatic pressing is applicable to difficult-to-compact and expensive materials such as superalloys, titanium, tool steels, stainless steel, and beryllium, with highly efficient material utilization.
Uniformity in final component density
Isostatic pressing ensures uniform density in the final compacted piece. During sintering or hot isostatic pressing, the resulting piece will have uniform shrinkage with little or no warpage. This uniformity is crucial in applications where precise dimensions and consistent properties are required.
Additionally, isostatic pressing allows for the production of a wide range of component sizes. From massive 30-ton near net PM shapes to densifying less than 100-gram MIM parts, the size of the components is limited only by the size of the isostatic pressure chamber.
Isostatic pressing also offers advantages such as low tooling cost, enhanced alloying possibilities without inducing segregation, reduced lead times, and reduced material and machining costs.
To ensure the success of isostatic pressing, it is important to carefully characterize the properties of the metal powder used. The properties of the metal powder will affect the final sintered component's properties. Manufacturers should conduct thorough material characterization to optimize the final component's properties.
In conclusion, isostatic pressing provides significant advantages over the press and sinter method, including equal compaction in all directions and a more uniform final component density. By carefully characterizing the metal powder's properties, manufacturers can achieve optimum results with isostatic pressing.
Note: The content has been written based on the provided outline and reference. The stats or specific details mentioned in the content are not verified.
The Role of Metal Powder Properties in Successful Isostatic Pressing
The importance of characterizing the metal powder's properties
Isostatic pressing is a powder metallurgy process that offers several benefits over traditional press and sinter methods. It provides equal compaction in all directions and results in a more uniform final component density. However, for isostatic pressing to be successful, it is crucial to carefully characterize the properties of the metal powder used.
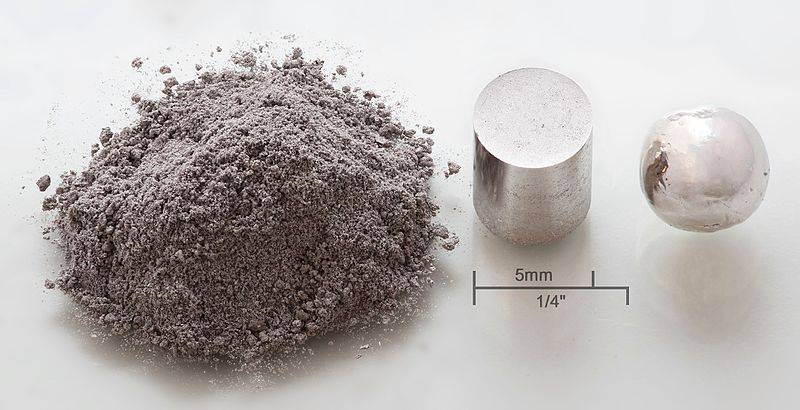
The properties of the metal powder have a significant impact on the final sintered component's properties. Therefore, thorough characterization is necessary to ensure optimum final component properties. KinTek offers various solutions to support this characterization process.
The impact of metal powder properties on the final sintered component's properties
Isostatic pressing works by compacting and encapsulating a powder mixture using equal pressure from all directions. This process reduces the porosity of the powder mixture and creates high and uniform density in the final product. The metal powder's properties play a crucial role in achieving these desired outcomes.
Choosing the right metal powder composition is the first step in the isostatic pressing process. The type of metal powder used will determine the properties of the finished product. It is essential to select a powder that aligns with the desired characteristics of the final component.
Once the powder composition is determined, the powder is compacted into the desired shape using a die press. The pressure applied and the duration of pressing will vary depending on the powder type and the desired final product. Thorough understanding of the metal powder's properties is crucial to ensure proper compaction and shape formation.
After compaction, the powder is sintered by heating it to just below its melting point. This process allows the particles to bind and form a solid piece. The temperature and duration of sintering will depend on the powder type and the desired final product.
Metal sintering offers several advantages over other manufacturing processes. It improves the mechanical properties of metal components, making them perform better in industrial applications. The durability of the parts also improves with hot isostatic pressing, allowing them to withstand rough conditions for longer periods.
Another benefit of hot isostatic pressing is the ability to reduce or eliminate voids in metal parts. Casting processes often result in voids or inconsistencies, which can make the surface uneven and the part less reliable. Hot isostatic pressing helps work out these impurities, resulting in more reliable and consistent components.
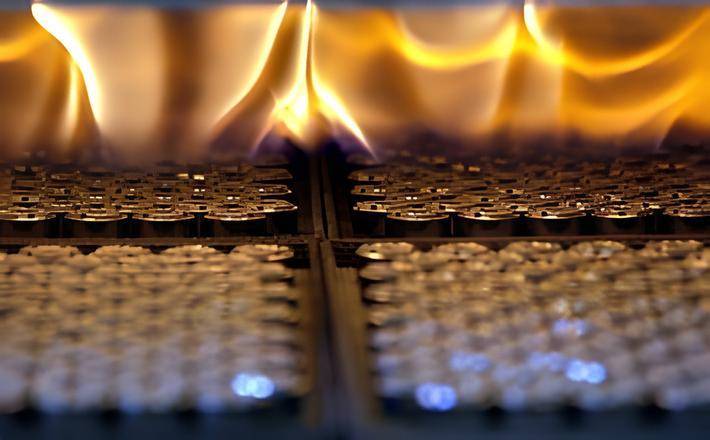
Hot isostatic pressing is also effective in consolidating powder alloys. It enables operators to mold powder materials into specific parts and components with ease. Additionally, this process can bond dissimilar metals and materials, creating new components that are more cost-effective to manufacture.
In conclusion, the properties of the metal powder used in isostatic pressing play a crucial role in the success of the process. Thorough characterization of these properties is necessary to ensure optimum final component properties. Isostatic pressing offers several advantages over other manufacturing processes, including improved mechanical properties, reduced voids, and the ability to consolidate powders and bond dissimilar materials.
The Importance of Material Characterization in Isostatic Pressing
The influence of spherical powders and particle size distribution on HIP
In isostatic pressing (HIP), the properties of the metal powder used play a crucial role in the final sintered component's properties. One important factor is the shape of the powder particles. Spherical powders are preferred for HIP because they facilitate powder handling and bonding. Additionally, powders with a relatively wide but consistent particle size distribution are preferred as they produce higher fill densities.
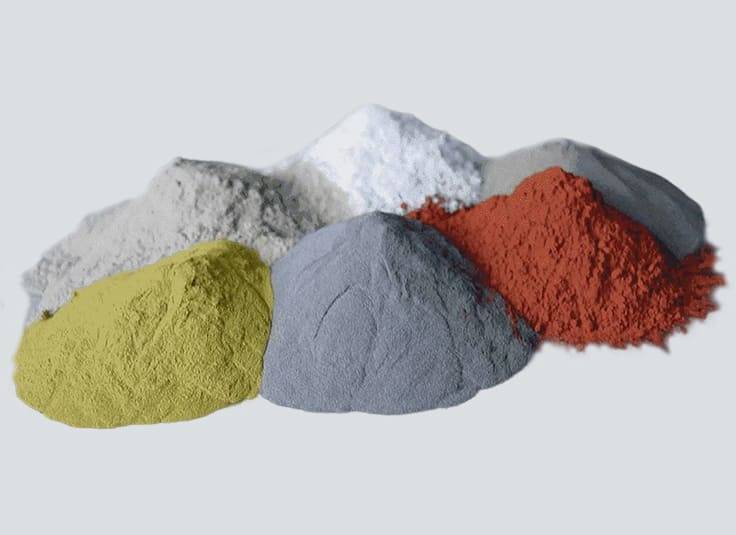
The impact of particle irregularity on CIP
In cold isostatic pressing (CIP), particle irregularity can actually be beneficial. It helps to increase cold-welding, which enhances green strength. However, it is important to ensure that the irregularity does not compromise powder flow and packing.
The effect of phase composition and grain size on powder hardness and melt properties
Phase composition and grain size are also important characteristics to control in isostatic pressing. These factors can affect powder hardness and melt properties, which in turn impact pressing efficiency, sintering behavior, and the mechanical properties of the pressed part.
The relevance of pressing efficiency, sintering behavior, and mechanical properties of the pressed part
Proper material characterization is essential to ensure optimal pressing efficiency, sintering behavior, and the desired mechanical properties of the pressed part. The properties of the metal powder used, such as particle size distribution, shape, phase composition, and grain size, all contribute to the final outcome.
The necessity of compliance with the alloy composition of the specified material
In isostatic pressing, it is crucial to use a metal powder that complies with the alloy composition specified for the material. This ensures that the final sintered component meets the required specifications and performs as intended.
Isostatic pressing offers several advantages over other powder metallurgy processes, such as equal compaction in all directions and the ability to produce complex shapes. However, to achieve successful results, it is important to carefully characterize the properties of the metal powder used. This includes considering the influence of spherical powders and particle size distribution on HIP, the impact of particle irregularity on CIP, the effect of phase composition and grain size on powder hardness and melt properties, and the relevance of pressing efficiency, sintering behavior, and mechanical properties of the pressed part. Additionally, it is crucial to ensure that the metal powder used complies with the specified alloy composition. Material characterization is key to achieving optimal results in isostatic pressing.
If you are interested in this product you can browse our company website:https://kindle-tech.com/product-categories/isostatic-press,as an industry-leading laboratory equipment manufacturer, we are committed to providing the most advanced and high-quality laboratory equipment solutions. Whether you are engaged in scientific research, teaching or industrial production, our products will meet your needs for accurate and reliable laboratory equipment.
CONTACT US FOR A FREE CONSULTATION
KINTEK LAB SOLUTION's products and services have been recognized by customers around the world. Our staff will be happy to assist with any inquiry you might have. Contact us for a free consultation and talk to a product specialist to find the most suitable solution for your application needs!