Introduction: What is Isostatic Pressing?
Isostatic pressing (IP) is a manufacturing process used to improve the mechanical properties of castings. It involves applying uniform pressure from all directions to a material using a liquid or gas medium. This process helps to reduce porosity and improve the strength, ductility, and fatigue resistance of castings. IP is commonly used in the aerospace, automotive, and medical industries to produce high-quality components. There are different types of IP, including cold isostatic pressing (CIP), hot isostatic pressing (HIP), and warm isostatic pressing (WIP). Each type of IP has its own unique advantages and disadvantages, depending on the application.
Table of Contents
Benefits of Isostatic Pressing for Castings
Isostatic pressing is a proven method of improving the mechanical properties of castings. In this section, we will discuss some of the benefits of isostatic pressing for castings.
Improved Density and Uniformity
Isostatic pressing involves subjecting a casting to high pressure from all directions, which helps to eliminate any internal voids or porosity in the material. This results in a denser and more uniform structure, which in turn improves the strength, toughness, and fatigue resistance of the casting. The improved density and uniformity of the casting also help to reduce the risk of cracking or distortion during machining or heat treatment, which can be a major concern for many types of castings.
Improved Surface Finish and Dimensional Accuracy
Isostatic pressing can also help to improve the surface finish and dimensional accuracy of castings. The uniform pressure applied during the process helps to eliminate any surface irregularities, resulting in a smoother and more uniform surface finish. Additionally, the elimination of internal voids and porosity helps to improve the dimensional accuracy of the casting, resulting in a more precise final product.
Increased Resistance to Corrosion and Wear
Isostatic pressing can also increase the resistance of castings to corrosion and wear. The elimination of internal voids and porosity helps to create a more homogeneous structure that is less susceptible to corrosion and wear. Additionally, isostatic pressing can be used to enhance the alloying elements within the casting, further increasing its resistance to corrosion and wear.
Enhanced Fatigue Resistance
One of the most significant benefits of isostatic pressing for castings is the enhanced fatigue resistance it provides. The elimination of internal voids and porosity helps to create a more uniform structure that is less susceptible to fatigue failure. This can be particularly important in applications where the casting is subjected to cyclic loading, such as in aerospace or automotive applications.
Reduced Scrap and Losses
Isostatic pressing can also help to reduce scrap and losses during the production process. By creating a more uniform and homogeneous structure, isostatic pressing can help to minimize defects and improve the overall quality of the casting. This, in turn, can help to reduce the amount of scrap and losses during the production process, resulting in a more efficient and cost-effective production process.
In conclusion, isostatic pressing is a highly effective way to improve the quality and performance of castings. The process offers several benefits, including improved density and uniformity, enhanced surface finish and dimensional accuracy, increased resistance to corrosion and wear, enhanced fatigue resistance, and reduced scrap and losses. These benefits make isostatic pressing a popular choice for a range of industries, including aerospace, automotive, and medical device manufacturing.
Types of Isostatic Pressing
Isostatic pressing is an effective way of improving the mechanical properties of castings. There are two main types of isostatic pressing: cold isostatic pressing (CIP) and hot isostatic pressing (HIP).
Cold Isostatic Pressing (CIP)
Cold isostatic pressing (CIP) involves the application of pressure to a material at room temperature. It is typically used to consolidate powders into solid shapes. In CIP, the powder mixture is compacted and encapsulated using isostatic pressure, which is uniformly applied from all directions. This method is particularly useful for materials such as ceramics, metals, plastics, and carbon. The process of CIP offers several benefits, including high and uniform density, the ability to form product shapes to precise tolerances, and efficient material utilization.
Warm Isostatic Pressing (WIP)
Warm isostatic pressing (WIP) is similar to cold isostatic pressing, but the shapes are pressed at a warm temperature of about 100°C. This method is useful for materials that require higher processing temperatures than those typically used in CIP.
Hot Isostatic Pressing (HIP)
Hot isostatic pressing (HIP) is performed at high temperatures and pressures and is used to remove porosity and defects from castings by diffusing gas atoms out of the material. HIP is particularly effective for improving the properties of superalloys used in high-performance applications such as aerospace components. In this process, parts are heated in an inert gas, generally argon, which applies "isostatic" pressure uniformly in all directions. This causes the material to become "plastic" allowing voids to collapse under the differential pressure. The surfaces of the voids diffusion bond together to effectively eliminate the defects achieving near theoretical density, while improving mechanical properties of the parts such as investment castings.
In conclusion, isostatic pressing is a valuable technique for enhancing the strength and quality of castings, and has numerous applications in a wide range of industries. Isostatic pressing offers several benefits, including high and uniform density, the ability to form product shapes to precise tolerances, and efficient material utilization. The choice of which type of isostatic pressing to use depends on the material being processed and the desired end result.
Working of Isostatic Press
Isostatic pressing is a powder metallurgy forming process that involves applying equal pressure in all directions to a powder compact. It is used to achieve maximum uniformity of density and microstructure without the geometrical limitations of uniaxial pressing.
The working of an isostatic press involves the following steps:
Step 1: Placing the Casting in a High-Pressure Vessel
The casting is placed in a high-pressure vessel that is filled with a liquid or gas. The vessel is designed to withstand high pressure and is sealed off to prevent any leaks.
Step 2: Pressurizing the Vessel
The vessel is then pressurized to a predetermined level. This results in the application of pressure to the casting from all directions. The pressure is maintained for a specific period, during which the material is compressed and densified.
Step 3: Compression and Densification
During the pressurization process, the material is compressed and densified. This results in a significant reduction in porosity and an increase in density. The uniform pressure applied from all directions ensures that the material is of the same size in all directions.
Step 4: Removing the Casting
Once the pressurization process is complete, the vessel is depressurized, and the casting is removed. The resulting casting has improved mechanical properties such as improved strength, toughness, and resistance to wear and fatigue.
Isostatic pressing is particularly beneficial for castings that are made from materials that are difficult to densify using other methods. It is also useful for creating complex shapes and components that require high levels of accuracy and precision.
In conclusion, isostatic pressing is a highly effective method for improving the mechanical properties of castings. The process results in castings that are stronger, more durable, and more resistant to wear and fatigue. It is a popular choice for manufacturers who require high-quality components for demanding applications.
Advantages of Isostatic Pressing
Isostatic pressing is a technique used to improve the mechanical properties of castings. This process offers several advantages over traditional casting methods. In this section, we will discuss the advantages of isostatic pressing in detail.
Improved Mechanical Properties
Isostatic pressing produces castings with improved mechanical properties such as increased strength, hardness, and wear resistance. This makes isostatic pressing an ideal technique for producing components that require high strength and durability, such as those used in aerospace and automotive applications.
Uniform Density
Isostatic pressing allows for the production of castings with uniform density, which is not possible with traditional casting methods. The pressure applied uniformly from all directions removes any porosity or voids that may have formed during the casting process. This results in a denser and more uniform structure, which in turn improves the mechanical properties of the casting.
Production of Complex Shapes
Isostatic pressing allows for the production of complex shapes with high precision and accuracy, which is not possible with traditional casting methods. The technique can be used to produce difficult shapes that cannot be produced by other methods. Additionally, it can be used to produce large-sized materials. The only limitation to the size of materials produced by this method is the size of the pressure vessel.
Consistency and Repeatability
Isostatic pressing can be used to produce parts with a high degree of consistency and repeatability. This makes it a popular choice for mass production. The process can be automated for high-volume production, such as in spark plug insulator manufacturing.
Corrosion Resistance
Isostatic pressing improves the corrosion resistance of a material. Thus materials that undergo this process have a longer lifespan than most other materials.
Advantages in Powder Metallurgy
Isostatic pressing is used in powder metallurgy. It is used for the compacting step of powder metallurgy that comes just before the sintering step. In powder metallurgy, CIP is often used to produce complex shapes and dimensions.
Refractory Metals
Isostatic pressing is used to produce refractory metals. They include tungsten, molybdenum, and tantalum. Tungsten, for example, is used to manufacture wires for filaments in the lamp industry. Generally, refractory metals have a high melting point and are resistant to wear and tear.
In conclusion, Isostatic pressing is a valuable technique for improving the mechanical properties of castings and offers several advantages over traditional casting methods. The technique can produce castings with improved mechanical properties, uniform density, complex shapes, consistency and repeatability, corrosion resistance, and is advantageous in powder metallurgy and refractory metals.
Hot Isostatic Pressing for Densification Treatment
Hot Isostatic Pressing (HIP) is a process used to improve the mechanical properties of castings by eliminating porosity and densifying the material. The HIP process involves subjecting the casting to high temperature and pressure in an inert gas environment, which promotes material diffusion and consolidation. This results in a more uniform and homogeneous material with improved strength, fatigue resistance, and toughness.
The HIP Process
The HIP process can be broken down into four key steps: powder preparation, degassing and sealing, hot isostatic pressing, and post-processing.
Powder preparation
The first step in the HIP process involves the preparation of a casting or powder material. The material is often in the form of a powder or casting and is designed to meet the specific properties required for the final product.
Degassing and Sealing
Once the material is prepared, it is subjected to a degassing process to remove any trapped gases that could cause porosity. The casting or powder material is then sealed in a metal container using a welded or brazed closure.
Hot Isostatic Pressing
After the material is sealed, it is placed in a hot isostatic press. The press contains an inert gas, usually argon, that is pressurized to 100MPa at 1000°C. The pressurized gas acts as the pressure transfer medium, and the casting or powder material is subjected to equal pressure from all directions. This promotes material diffusion and consolidation, resulting in a more uniform and homogeneous material with improved mechanical properties.
Post-Processing
After the HIP process is complete, the material is removed from the press and subjected to post-processing, which can include heat treatment, machining, and surface finishing. These steps are essential to ensure that the final product meets the required specifications and mechanical properties.
Benefits of HIP
The HIP process offers several benefits over traditional casting and powder metallurgy processes.
Improved Material Properties
The HIP process results in a more uniform and homogeneous material with improved mechanical properties, including strength, fatigue resistance, and toughness.
Near-Net-Shape Components
The HIP process can produce near-net-shape components with complex geometries, reducing the need for additional machining and processing.
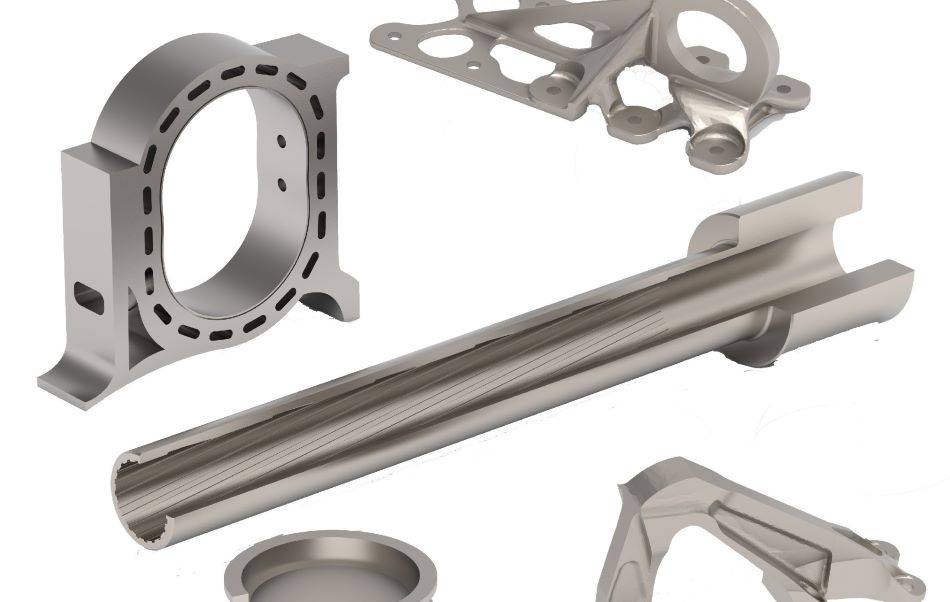
Repair Defects
The HIP process can be used for post-casting treatments to repair defects and improve surface finish.
Reduction in Porosity
The HIP process reduces porosity, resulting in a denser and more uniform material with improved mechanical properties.
In conclusion, hot isostatic pressing is a crucial technology for industries that require high-performance and reliable components that can withstand extreme environments and loads. The HIP process improves the mechanical properties of castings by eliminating porosity and densifying the material, resulting in a more uniform and homogeneous material with improved strength, fatigue resistance, and toughness.
Conclusion
In conclusion, isostatic pressing is a highly effective method for improving the mechanical properties of castings. By applying uniform pressure in all directions, isostatic pressing eliminates porosity and improves density, resulting in stronger and more durable castings. This technique offers numerous benefits over traditional processing methods, including increased efficiency, precision, and flexibility. With its ability to produce high-quality castings with excellent mechanical properties, isostatic pressing is widely used in a variety of industries, including aerospace, automotive, and medical. Overall, isostatic pressing is a valuable tool for manufacturers seeking to improve the quality and performance of their castings.
CONTACT US FOR A FREE CONSULTATION
KINTEK LAB SOLUTION's products and services have been recognized by customers around the world. Our staff will be happy to assist with any inquiry you might have. Contact us for a free consultation and talk to a product specialist to find the most suitable solution for your application needs!