Introduction
Table of Contents
Isostatic Pressing, also known as cold or hot isostatic pressing (CIP/HIP), is a manufacturing process used in various industries, including aerospace and defense. This technique involves applying equal pressure from all directions to a material, resulting in uniform density and improved mechanical properties. Isostatic Pressing plays a crucial role in the aerospace and defense industry by manufacturing components such as aerospace castings, jet aircraft engine parts, turbine blades, and even bulletproof materials and gun parts. With the growth projections for the aerospace and defense sector, Isostatic Pressing is expected to play an increasingly significant role in meeting the industry's demands.
Understanding Isostatic Pressing
Definition and process of Isostatic Pressing
Isostatic pressing is a powder processing technique that uses fluid pressure to compact the part. Metal powders are placed in a flexible container, which acts as the mold for the part. Fluid pressure is exerted over the entire outside surface of the container, causing the container to press and form the powder into the correct geometry. This process allows for the production of various types of materials from powder compacts by reducing the porosity of the powder mixture.
The main types: Hot Isostatic Pressing (HIP) and Cold Isostatic Pressing (CIP)
Hot Isostatic Pressing (HIP) is used to reduce the porosity of metals and increase the density of many ceramic materials. It involves compressing a volume of metal powder at high temperatures and pressures to create a product with a homogeneous annealed microstructure and minimal impurities.
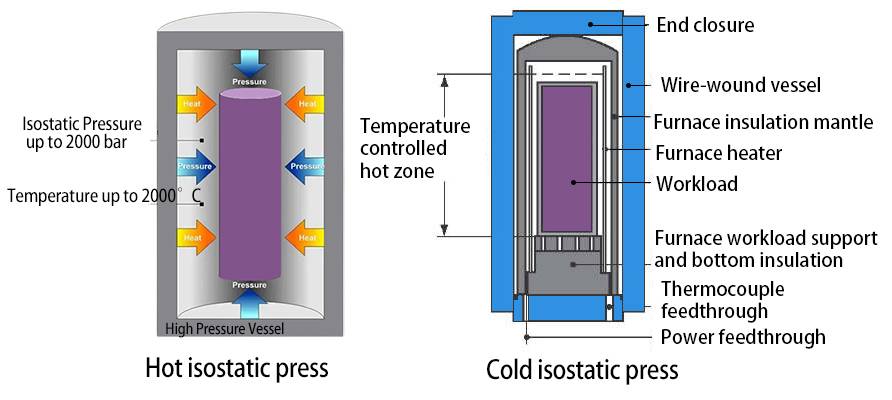
Cold Isostatic Pressing (CIP), on the other hand, subjects a material to uniform pressure from all sides by immersing it in a high-pressure fluid medium and applying hydraulic pressure. CIP is particularly effective for shaping and consolidating powdered materials, creating intricate shapes and achieving high green density.
Capabilities and process types: wet bag pressing and dry bag pressing
Isostatic pressing can be performed using two main process types: wet bag pressing and dry bag pressing. In wet bag pressing, a separate elastomeric mold is loaded outside of the press and then submerged in the pressure vessel. After pressurization and compaction, the mold is removed from the vessel, and the part is retrieved. This process is better suited for the production of large parts but has lower automation capabilities.
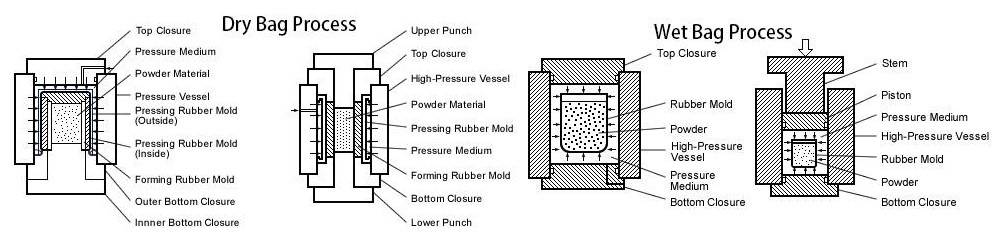
Dry bag pressing, on the other hand, creates a mold that is integrated into the pressure vessel. The powder is added to the mold, the mold is sealed, pressure is applied, and then the part is ejected. This process allows for easier automation and higher production rates.
Scale of operations: small-sized HIP, medium-sized HIP, and large-sized HIP
Isostatic pressing can be performed at different scales of operations, depending on the size of the components being produced. The scale of operations includes small-sized HIP, medium-sized HIP, and large-sized HIP. These different scales allow for the production of components of varying sizes and quantities.
In summary, Isostatic Pressing is a powder processing technique that uses fluid pressure to compact materials and reduce porosity. It includes both Hot Isostatic Pressing (HIP) and Cold Isostatic Pressing (CIP), each offering unique advantages. The process can be performed using wet bag pressing or dry bag pressing, with different capabilities and automation levels. Isostatic pressing can be scaled up or down depending on the size of the components being produced.
Application in Various Industries
The usage of high purity materials extends to a wide range of industries, including manufacturing, automotive, electronics and semiconductor, medical, aerospace and defense, energy and power, research and development, and others. These materials have proven to be highly adaptable and beneficial in these sectors.
Manufacturing Industry
In the manufacturing industry, high purity materials find applications in various areas such as tooling, machine components, and specialty applications. Materials like tool steels, carburizing steels, HSLA (High-Strength Low-Alloy) steels, alloyed steels, stainless steels, alloys, super alloys, titanium, and titanium alloys are commonly used.
Automotive Industry
High purity materials are also extensively used in the automotive industry. They are utilized in the production of architectural ironmongery, panels, sheets, dyes, molds, and various components. These materials contribute to the durability, strength, and overall performance of automotive vehicles.
Electronics and Semiconductor Industry
The electronics and semiconductor industry heavily relies on high purity materials for the manufacturing of electronic devices and components. These materials play a crucial role in the production of semiconductor devices, electronics, photovoltaics, biomedical and dental products, optical devices, batteries, fuel cells, and supercapacitors. They are essential for high-technology applications.
Medical Industry
In the medical field, high purity materials find application in the production of ceramic or metal implants, biomedical devices, and dental products. These materials are carefully selected for their biocompatibility, durability, and resistance to corrosion, ensuring optimal performance and patient safety.
Aerospace and Defense Industry
The aerospace and defense industry also benefits from the use of high purity materials. These materials are utilized in the production of components for aircraft, spacecraft, and defense systems. They contribute to the strength, reliability, and performance of these critical applications.
Energy and Power Industry
In the energy and power sector, high purity materials play a vital role in the production of components for power generation, transmission, and storage. They are used in applications such as commercial heat treatment, specialty applications, and the production of batteries, fuel cells, and supercapacitors.
Research and Development
High purity materials are extensively used in research and development activities across various industries. These materials serve as a foundation for innovation, allowing scientists and engineers to explore new possibilities and develop advanced technologies.
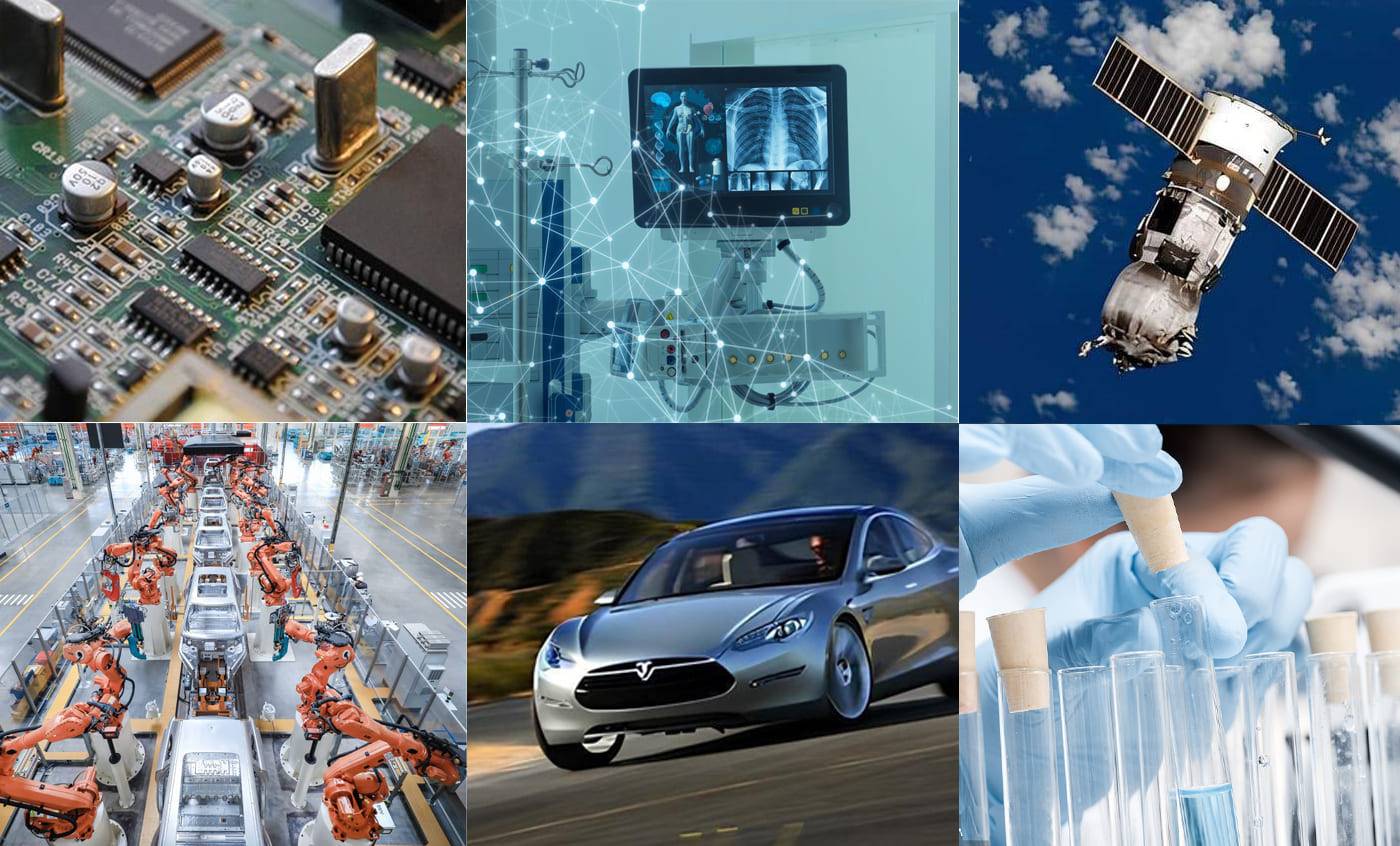
Other Industries
Apart from the aforementioned industries, high purity materials are also utilized in other sectors such as pharmaceuticals, food, environmental protection, optics, watches, jewelry, and thin film applications (e.g., window tint, food packaging). The versatility and adaptability of these materials make them suitable for a wide range of applications.
Overall, high purity materials have proven to be indispensable in various industries, enabling technological advancements, improving product performance, and contributing to the overall progress of society.
Isostatic Pressing in Aerospace and Defense Industries
Role of Isostatic Pressing in aerospace and defense industry
Isostatic pressing plays a crucial role in the aerospace and defense industry. It is used for manufacturing aerospace castings, jet aircraft engine components, and turbine blades. The process allows for the consolidation of powders and defect healing of castings, resulting in high-quality and durable products. Isostatic pressing is especially beneficial in the aerospace industry due to its ability to apply a uniform and equal force over the entire product, regardless of its shape or size.
Use in manufacturing aerospace castings, jet aircraft engine components, and turbine blades
Isostatic pressing is widely used in the aerospace industry for manufacturing various components. It is commonly used in the production of aerospace castings, including complex shapes and intricate designs. The process ensures the consolidation of powders and eliminates any defects, resulting in high-quality castings that meet the stringent requirements of the aerospace industry.
Additionally, isostatic pressing is utilized in the manufacturing of jet aircraft engine components. The process allows for the production of engine parts with precise tolerances and high density, ensuring optimal performance and efficiency. Isostatic pressing is especially beneficial for turbine blades, which require high strength and durability to withstand the extreme conditions of aerospace applications.
Production of bulletproof materials and gun parts in defense industry
In the defense industry, isostatic pressing plays a vital role in the production of bulletproof materials and gun parts. The process allows for the consolidation of powders to create dense and high-strength materials that provide effective ballistic protection. Isostatic pressing ensures uniformity and eliminates defects, resulting in reliable and durable bulletproof materials.
Moreover, isostatic pressing is utilized in the manufacturing of gun parts, including barrels, receivers, and triggers. The process allows for the production of components with precise dimensions and high density, ensuring optimal performance and reliability in defense applications.
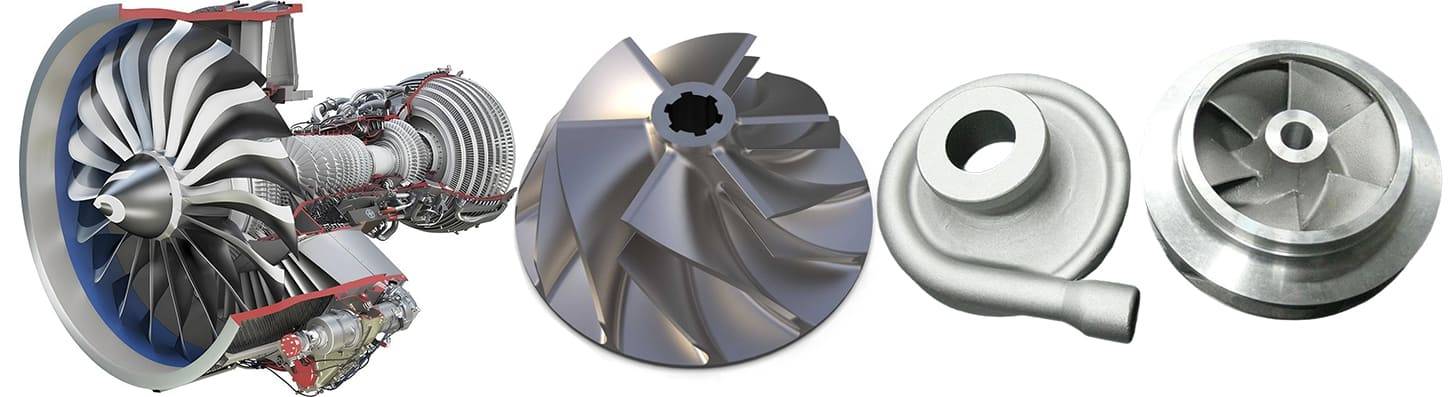
Growth projections for the aerospace and defense sector
The aerospace and defense sector is experiencing rapid growth, driven by increasing demand for advanced space systems, aircraft, and defense capabilities. According to the India Brand Equity Foundation, the aerospace and defense sector is projected to reach $70 billion by 2030. This growth is attributed to the demand for advanced infrastructure and the need for technological advancements in the industry.
The growing aerospace and defense sector presents significant opportunities for the isostatic pressing market. As the industry continues to expand, the demand for aerospace castings, jet aircraft engine components, turbine blades, bulletproof materials, and gun parts will increase. Isostatic pressing, with its ability to produce high-quality and durable components, will play a crucial role in meeting the growing demands of the aerospace and defense sectors.
In conclusion, isostatic pressing plays a vital role in the aerospace and defense industries. It is used for manufacturing aerospace castings, jet aircraft engine components, turbine blades, bulletproof materials, and gun parts. The process ensures the production of high-quality and durable components that meet the stringent requirements of these industries. With the projected growth of the aerospace and defense sectors, the demand for isostatic pressing is expected to increase, further driving the market growth.
Conclusion
In conclusion, isostatic pressing plays a crucial role in the aerospace and defense industries. It is used extensively in manufacturing aerospace castings, jet aircraft engine components, turbine blades, bulletproof materials, and gun parts. The growth projections for the aerospace and defense sector indicate a significant demand for isostatic pressing technology in the coming years. With increasing investments in HIP technology and notable acquisitions in the market, it is clear that the industry recognizes the value and potential of isostatic pressing. As the aerospace and defense sectors continue to evolve and innovate, isostatic pressing will remain a vital process for achieving high-quality and reliable components.
If you are interested in our products, please visit our company website:https://kindle-tech.com/product-categories/isostatic-press, where innovation has always been a priority. Our R&D team consists of experienced engineers and scientists who closely follow industry trends and are constantly pushing the boundaries of what is possible. Our laboratory equipment incorporates the latest technology to ensure that you can obtain accurate and repeatable results during your experiments. From high-precision instruments to intelligent control systems, our products will provide you with unlimited possibilities for your experimental work.
CONTACT US FOR A FREE CONSULTATION
KINTEK LAB SOLUTION's products and services have been recognized by customers around the world. Our staff will be happy to assist with any inquiry you might have. Contact us for a free consultation and talk to a product specialist to find the most suitable solution for your application needs!