Introduction to Magnetron Sputtering
Overview of Magnetron Sputtering Process
Magnetron sputtering is a sophisticated physical vapor deposition (PVD) technology that involves the deposition of a thin film onto a substrate. This process is conducted within a vacuum chamber, where a target material is subjected to a high-energy plasma. The plasma, generated by a combination of a sputtering gas and a strong magnetic field near the target, causes atoms or molecules of the target material to be ejected and subsequently deposited onto the substrate.
The magnetic field plays a crucial role in magnetron sputtering, as it confines the plasma to a region close to the target. This confinement ensures that the energetic ions within the plasma primarily interact with the target material, minimizing damage to the growing thin film on the substrate. The process begins with the evacuation of the chamber to achieve high vacuum conditions, which reduces background gas pressures and potential contaminants. Subsequently, the sputtering gas is introduced into the chamber, and the pressure is regulated to the milliTorr range using a precision control system.
In essence, magnetron sputtering is a plasma-based deposition process where ions strike the target, causing atoms to be ejected. These atoms then travel through the vacuum environment and incorporate into the growing film on the substrate. The intricate interplay between the magnetic field, plasma, and vacuum conditions ensures the precise and efficient formation of thin films, making magnetron sputtering a versatile and widely-used technique in various industrial applications.
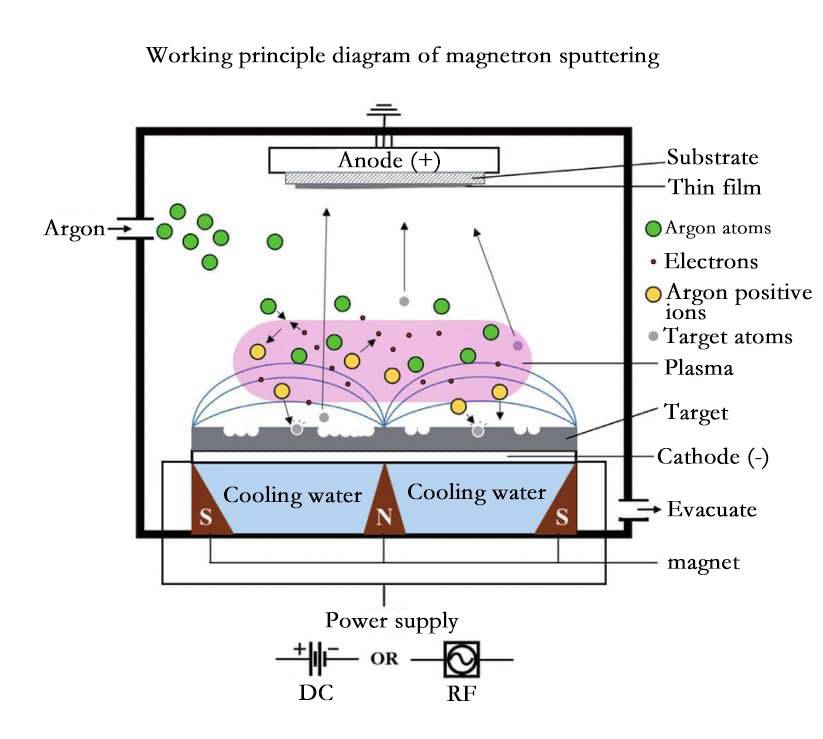
Causes of Target Material Sparking
Oxidation of Target Material Surface
The interaction between the target material and oxygen molecules within the vacuum chamber is a critical factor in the sputtering process. When the target material is exposed to oxygen, it can undergo a chemical reaction, resulting in the formation of oxides on its surface. These oxides, while initially stable, can later decompose under the high-energy conditions of the sputtering process.
The decomposition of these oxides releases gases, which can accumulate within the vacuum chamber. This accumulation can lead to localized pressure changes and, in extreme cases, cause sparks. The sparks are a result of the sudden release of energy from the decomposition process, which can disrupt the sputtering environment and potentially damage the equipment.
To mitigate this issue, it is essential to control the atmosphere within the vacuum chamber. This involves maintaining a low concentration of reactive gases like oxygen, ensuring that the environment remains stable and conducive to the sputtering process. Additionally, regular cleaning of the target material surface can prevent the buildup of oxides, thereby reducing the risk of sparking.
Surface Defects on Target Material
Surface defects on the target material, such as tiny cracks or holes, can significantly impact the sputtering process. These imperfections act as localized points of weakness, where the electrical discharge during sputtering becomes concentrated. This concentration of discharge can lead to the formation of strong local arcs, which are intense electrical discharges that can ignite the target material.
The presence of such defects is particularly problematic because they disrupt the uniform distribution of the sputtering process. Instead of a smooth, even coating, the defects cause the energy to be focused in specific areas, leading to localized overheating and potential ignition. This not only compromises the quality of the coating but also poses a safety risk to the equipment and operators.
To mitigate the risk of sparking due to surface defects, it is crucial to inspect and prepare the target material thoroughly before the sputtering process begins. This includes identifying and addressing any surface imperfections, ensuring that the material is in optimal condition for the coating application.
Improper Sputtering Conditions
Improper sputtering conditions can significantly contribute to target ignition during the magnetron sputtering process. These conditions often arise from a combination of high or low power settings during target heating and uneven magnetic fields. High power settings can cause excessive heating, leading to rapid vaporization and subsequent ignition of the target material. Conversely, low power settings may result in insufficient heating, causing localized overheating and sparking due to uneven distribution of energy.
Moreover, an uneven magnetic field can disrupt the uniform distribution of plasma within the vacuum chamber, leading to concentrated discharges at specific points on the target surface. This concentration of energy can create strong local arcs, which are prone to ignition. The table below summarizes the effects of these improper conditions:
Condition | Effect |
---|---|
High Power Setting | Excessive heating, rapid vaporization, and target ignition |
Low Power Setting | Insufficient heating, localized overheating, and sparking |
Uneven Magnetic Field | Disrupted plasma distribution, concentrated discharges, and ignition |
Addressing these issues requires a meticulous approach to setting and maintaining the sputtering parameters, ensuring that the power and magnetic field are both stable and evenly distributed.
Solutions to Prevent Target Ignition
Ensure Target Surface Cleanliness
Cleaning the target surface before the sputtering process is a critical step to prevent the occurrence of sparks. This procedure involves meticulously removing any dirt, contaminants, and particularly oxides that may have formed on the surface of the target material. Oxides are particularly problematic as they can decompose under the high-energy conditions of sputtering, releasing gases that can lead to localized arcs and ignition.
To ensure thorough cleanliness, several methods can be employed:
- Mechanical Cleaning: Using brushes or abrasive materials to physically remove surface contaminants.
- Chemical Cleaning: Submerging the target in specific solvents or acids that can dissolve oxides and other impurities.
- Ultrasonic Cleaning: Utilizing ultrasonic waves to dislodge and remove particles embedded in the surface.
- Ion Beam Cleaning: Bombarding the target surface with an ion beam to remove contaminants at the atomic level.
The choice of cleaning method depends on the nature of the contaminants and the specific requirements of the sputtering process. Regardless of the method used, the goal is to achieve a pristine surface that is free from any substances that could interfere with the sputtering process or cause unwanted sparks. This meticulous preparation ensures that the target material is in optimal condition for the deposition of a high-quality thin film.
Control Vacuum Chamber Atmosphere
Maintaining the atmosphere within a controllable range is crucial to prevent the concentration of oxygen and other gases from reaching a flammable level. This involves creating and sustaining a modified atmosphere within the vacuum chamber, which can significantly reduce the risk of target material sparking during magnetron sputtering.
To achieve this, a sealed vessel is essential. This could be a work tube with specialized end seals designed for use with tube furnaces, or a retort commonly used in chamber furnaces. These vessels help in isolating the internal environment from external influences, thereby allowing precise control over the atmospheric conditions.
The process of evacuating a vessel reduces the number of atoms and molecules inside. However, achieving a perfect vacuum is practically impossible; even in a vacuum of less than 10-7 mbar, there are still approximately 109 particles per cubic centimeter. This residual gas presence must be managed carefully to prevent any buildup of flammable gases.
KINTEK offers a range of standard gas packages and associated equipment designed to assist in creating and maintaining these modified atmospheres. These products are not only versatile but also adaptable, allowing for greater operational flexibility. For instance, optional modified atmosphere equipment and accessories enable the use of the same products for multiple applications involving different gases, vacuum levels, or even no modified atmosphere at all.
By meticulously controlling the vacuum chamber atmosphere, the likelihood of target material ignition during magnetron sputtering can be significantly reduced, ensuring a safer and more efficient coating process.
Set Reasonable Sputtering Conditions
Adjusting sputtering conditions is crucial to prevent ignition and ensure the optimal performance of the magnetron sputtering process. The specific settings should be meticulously tailored to the characteristics of the target material and the specifications of the equipment. This involves fine-tuning parameters such as power levels, magnetic field configurations, and vacuum chamber pressures.
For instance, power levels should be carefully calibrated to match the target material's thermal properties. Excessive power can cause overheating, leading to localized arcs and ignition, while insufficient power may not effectively vaporize the material, resulting in poor coating quality. Similarly, magnetic field configurations need to be balanced to create an even distribution of plasma, avoiding concentrated discharge that can trigger sparks.
Additionally, maintaining an appropriate vacuum chamber pressure is essential. Too high a pressure can allow residual gases to interact with the target material, causing unwanted reactions and potential ignition. Conversely, too low a pressure can lead to inefficient plasma formation, affecting the sputtering process.
By systematically adjusting these conditions, operators can significantly reduce the risk of target material ignition, ensuring a stable and efficient sputtering process.
Regular Equipment Inspection
Regular equipment inspection is a critical practice in the context of magnetron sputtering to ensure the longevity and efficiency of the process. This routine maintenance involves a thorough examination of all components, from the vacuum chamber to the power supply units, to identify any signs of wear or malfunction. By adhering to a strict inspection schedule, operators can detect and address potential issues before they escalate into more significant problems.
One of the primary focuses of these inspections is to verify that all mechanical parts are functioning correctly. This includes checking for any loose connections, misaligned components, or signs of physical damage. Additionally, electrical systems must be scrutinized to ensure that they are operating within safe parameters, preventing any potential short circuits or power surges that could lead to equipment failure or, worse, safety hazards.
Moreover, regular inspections help in maintaining the integrity of the vacuum environment within the chamber. Any leaks or degradation in the vacuum seals can compromise the sputtering process, leading to suboptimal film deposition and potential target material sparking. By identifying and rectifying such issues promptly, operators can maintain a stable and controlled atmosphere necessary for high-quality coating applications.
In summary, regular equipment inspection is not merely a preventive measure but an essential aspect of ensuring the continuous and safe operation of magnetron sputtering equipment. It encompasses a comprehensive assessment of both mechanical and electrical components, ensuring that the entire system operates as intended, thereby minimizing the risk of target material sparking and other related issues.
CONTACT US FOR A FREE CONSULTATION
KINTEK LAB SOLUTION's products and services have been recognized by customers around the world. Our staff will be happy to assist with any inquiry you might have. Contact us for a free consultation and talk to a product specialist to find the most suitable solution for your application needs!