Definition of a Filter Press
Table of Contents
A filter press is a piece of equipment used in liquid/solid separation. It separates liquids and solids using pressure filtration. The slurry is pumped into the filter press and is dewatered under pressure. The design of the filter press is based on the volume and type of slurry that needs to be dewatered. There are various configurations of filter presses available, including sidebar automatic, manual overhead, automatic dual overhead beam, stainless steel clad, explosion-proof filter presses, vacuum filter presses, and hand filter presses.
Characteristics of a Filter Press
- Control over the filtration process: Filter presses offer a high degree of control over the filtration process, allowing for precise separation of liquids and solids.
- Cost-effectiveness: Filter presses are cost-effective compared to other liquid/solid separation methods.
- Easy to clean and maintain: Filter presses are easy to clean and maintain, ensuring efficient and reliable operation.
- Limited capacity: Laboratory filter presses have a limited capacity compared to industrial-scale filter presses.
- Manual operation: Some filter presses may require manual operation, which can be time-consuming.
- Limited pressure options: Laboratory filter presses have limited pressure options compared to industrial-scale filter presses.
Different configurations of a Filter Press
- Sidebar automatic: This configuration of a filter press is fully automated and offers high efficiency in liquid/solid separation.
- Manual overhead: This filter press configuration requires manual operation but is suitable for small-scale filtration applications.
- Automatic dual overhead beam: This configuration of a filter press combines automation with high capacity for efficient filtration.
- Stainless steel clad: Filter presses can be constructed with stainless steel cladding for durability and corrosion resistance.
- Explosion-proof: Some filter presses are designed for use in hazardous environments and are explosion-proof.
- Vacuum filter press: This type of filter press uses vacuum pressure for enhanced dewatering.
- Hand filter press: Hand filter presses are manually operated and are suitable for small-scale filtration needs.
Laboratory filter press
Filter presses are widely used in various industries and applications, including food and beverage processing, chemical manufacturing, mining, power generation, aggregates, asphalt and cement production, steel mills, and municipal plants. The size of filter presses can vary, ranging from small lab-scale presses to larger presses with capacities of 1500 and 2000 mm filter plates.
To optimize filter press operations, it is important to consider the four main components: the frame, filter plates, manifold (piping and valves), and filter cloth. These components can be customized to suit specific application needs. The working principle of a filter press involves the distribution of solids evenly during the fill cycle, which then form the filter cake on the filter cloth. The filtrate exits the filter plates, yielding clean filtered water. Once the chambers are full of solids, the cycle is complete, and the filter cakes can be released.
The design of a filter press depends on various factors, including filtration cycle time, desired cake dryness, cloth life, and the need for manual or automated plate shifting. Additional features such as automatic plate shifters, cloth washing systems, drip trays, cake shields, and safety light curtains can also be incorporated based on industry, application, and operational considerations.
Key Components of a Filter Press
A filter press is a pressure filtration method that is used to separate solids from liquids. It consists of several key components that work together to optimize its operation. Understanding these components is essential for efficient and effective filtration.
Frame
The frame of a filter press is typically made of carbon steel and is mounted on a skid. It provides the structure and support for the other components. The frame includes sidebars and a moveable head, also known as a follower, which can be extended to facilitate cake discharge.
Filter Plates
Filter plates are an essential part of a filter press. They are placed in the press in a specific order and function to hold the filter cloth in place. The plates have a recessed chamber design, allowing for the accumulation of solids during the filtration process. The number of chambers and the size of the filter plates depend on the specific application and filtration capacity required.
Manifold (Piping and Valves)
The manifold, consisting of piping and valves, plays a crucial role in the operation of a filter press. It is responsible for directing the flow of the filtrate, the liquid that passes through the filter plates, out of the press. The manifold typically has center feed and four corner filtrate outlets. The design may vary depending on whether the filter press uses corner feed or center feed membranes.
Filter Cloth
Filter cloth is a key ingredient in optimizing filter press operations. It is placed between the filter plates and serves as the medium through which the solids are captured while allowing the liquid to pass through. The choice of filter cloth material depends on the specific application and the desired filtration efficiency.
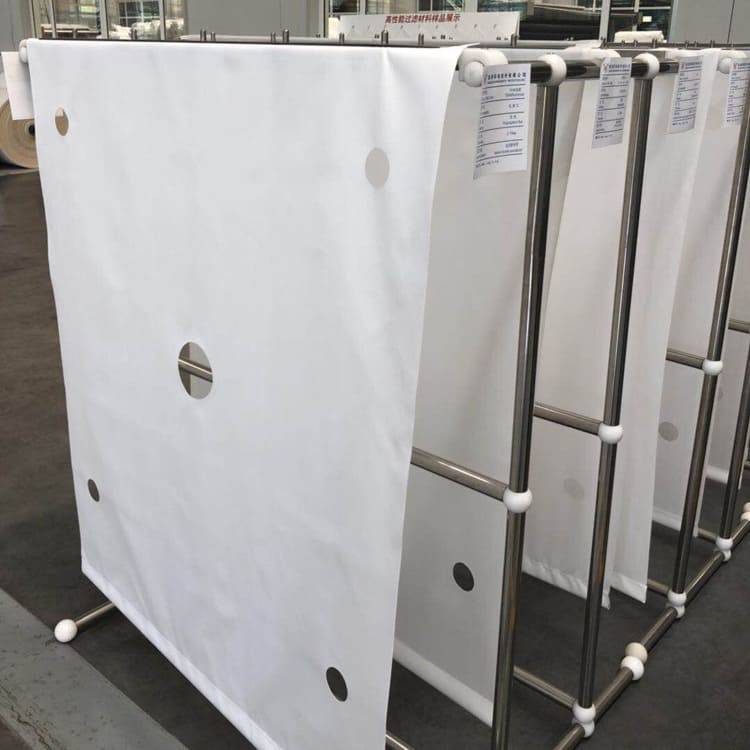
How Does a Filter Press Work?
The working principle of a filter press involves the pumping of slurry into the machine, distributing the solids evenly during the fill cycle. The solids accumulate on the filter cloth, forming a filter cake, while the filtrate exits the filter plates through the corner ports into the manifold, resulting in clean filtered water.
Additional Considerations
The design of a filter press is influenced by various factors, including filtration cycle time, desired cake dryness, cloth life, and the preference for manual or automated plate shifting. Some filter presses are designed for fully automatic, 24-hour operation in harsh environments like mines or chemical manufacturing plants. Additional features and systems, such as automatic plate shifters, cloth washing systems, drip trays, cake shields, and safety light curtains, can be included based on the specific industry, application, and operational requirements.
Understanding the key components of a filter press and their functions is crucial for optimizing its performance and achieving efficient solid-liquid separation. By selecting the appropriate frame, filter plates, manifold, and filter cloth, businesses can ensure the success of their filtration processes.
Working Principle of a Filter Press
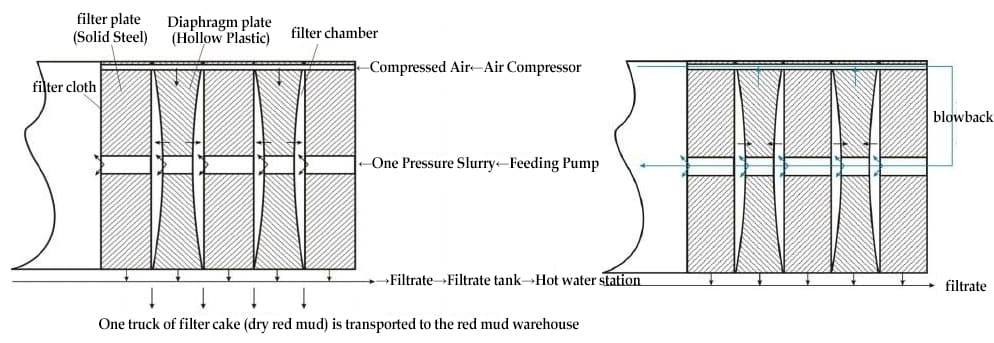
Distribution of solids during the fill cycle
During the fill cycle of a filter press, the slurry is pumped into the machine, and the solids are distributed evenly. This ensures that the filter cake is formed uniformly on the filter cloth.
Formation of filter cake
As the slurry is pumped into the filter press, the solids in the slurry build up on the filter cloth, forming a filter cake. The filter cake traps the solid particles while allowing the filtrate to pass through.
Role of pressure in filtration
Pressure plays a crucial role in the filtration process of a filter press. As the slurry is pumped into the filter press, pressure is applied to the system. This pressure forces the liquid to pass through the filter cloth, leaving behind the solid particles in the filter cake.
Completion of filtration cycle
Once the chambers of the filter press are full and the filter cakes are formed, the filtration cycle is complete. The filter cakes can then be released from the filter press. In some cases, automatic plate shifters are used to speed up the cycle time.
In summary, the working principle of a filter press involves the distribution of solids during the fill cycle, the formation of a filter cake, the application of pressure for filtration, and the completion of the filtration cycle. This process allows for effective liquid/solid separation and is widely used in various industries.
Applications of Filter Press
Range of sizes for different industries
Filter presses are available in a wide range of sizes to cater to the specific needs of different industries. From small lab-scale 150 mm presses to larger ones with 1500 and 2000 mm filter plates, there is a filter press suitable for every industry's requirements.
Applications in food and beverage processing
The food and beverage industry extensively uses filter presses for liquid/solid separation. These presses are used to remove impurities, clarify liquids, and separate solids from liquids in processes such as juice filtration, wine clarification, and syrup filtration.
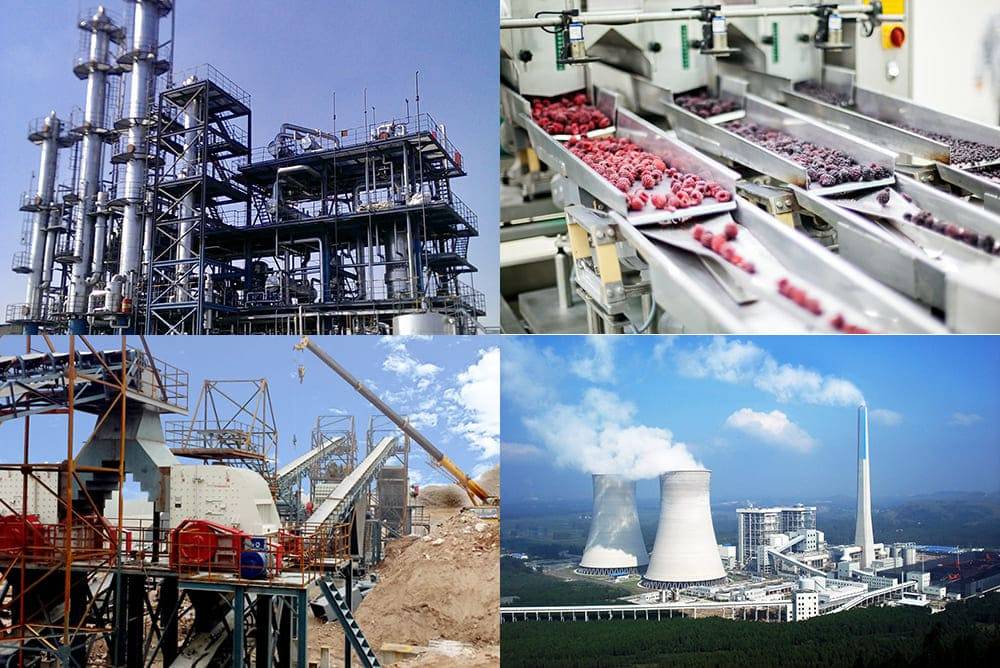
Applications in chemical manufacturing
Filter presses are widely used in chemical manufacturing for various filtration processes. They are used to separate solids from liquids, remove impurities, and recover valuable chemicals. Chemical processes such as drug synthesis, dye production, and chemical purification often involve the use of filter presses.
Applications in mining
The mining industry relies on filter presses for dewatering purposes. Filter presses are used to separate solids from mining slurries, reducing the moisture content and facilitating the handling and disposal of the solid waste. They are crucial in the production of minerals such as coal, iron ore, and copper.
Applications in power generation
Filter presses play a vital role in power generation plants, particularly in the treatment of wastewater and sludge. They are used to remove solids from the water before it is discharged, ensuring compliance with environmental regulations. Filter presses are also used in the dewatering of coal ash, a byproduct of coal-fired power plants.
Applications in aggregates, asphalt, and cement production
The aggregates, asphalt, and cement industries utilize filter presses for the separation of solids from liquids. Filter presses are used to dewater slurry generated during aggregate washing, separate solids from asphalt emulsions, and recover valuable materials in cement production.
Applications in steel mills
Steel mills rely on filter presses for the treatment of wastewater and sludge. Filter presses are used to remove solids from the mill's effluent, ensuring compliance with environmental regulations. They are also used in the dewatering of sludge generated during the steelmaking process.
Applications in municipal plants
Municipal wastewater treatment plants use filter presses for the dewatering of sludge. Filter presses are used to separate the solid waste from the wastewater, reducing its volume and facilitating its disposal. They play a crucial role in the efficient and sustainable operation of municipal wastewater treatment facilities.
In conclusion, filter presses have a wide range of applications in various industries. From food and beverage processing to chemical manufacturing, mining, power generation, and municipal plants, filter presses are essential for liquid/solid separation processes. Their versatility, efficiency, and cost-effectiveness make them a valuable tool in many industrial operations.
Customizing a Filter Press
Considerations for design
When customizing a filter press, there are several important factors to consider. The industry, application, and operational considerations will guide the specifics of the design. Some of the key considerations include:
-
Filtration cycle time: The time it takes for the filter press to complete a filtration cycle is an important factor to consider. This will depend on the desired cake dryness and the specific application requirements.
-
Cake dryness: Depending on the application, different levels of cake dryness may be required. The filter press design should be able to achieve the desired cake dryness efficiently.
-
Cloth life: The lifespan of the filter cloth used in the filter press is another important consideration. The design should ensure that the cloth can withstand the intended usage and provide optimal filtration performance.
-
Manual or automated plate shifting: Depending on the level of automation desired, the filter press can be designed for manual or automated plate shifting. Automated plate shifting can improve efficiency and reduce labor requirements.
-
Other factors: There are many other factors to consider when customizing a filter press, such as the desired filtration capacity, the material of construction, and additional features/systems like automatic plate shifters, cloth washing system, drip trays, cake shields, and safety light curtains.
Diagram of filter press
Factors influencing filtration capacity
The filtration capacity of a filter press is determined by several factors:
-
Size of the filter press: The size of the filter press, including the number of chambers and the size of the filter plates, will affect the filtration capacity. Larger filter presses with more chambers and larger filter plates will generally have a higher filtration capacity.
-
Pressure options: The pressure at which the filter press operates can also influence the filtration capacity. Higher pressures can increase the filtration rate and improve the overall capacity of the filter press.
-
Material of construction: The material of construction of the filter press can impact its filtration capacity. Different materials may have different flow characteristics and resistance to fouling, which can affect the filtration capacity.
Importance of number of chambers
The number of chambers in a filter press is an important design consideration. The number of chambers will determine the overall filtration capacity of the filter press. More chambers allow for more solids to be filtered and can increase the overall throughput of the system. However, adding more chambers can also increase the size and cost of the filter press. The number of chambers should be chosen based on the specific application requirements and desired filtration capacity.
Relevance of filter plate size
The size of the filter plates in a filter press is another important design consideration. Larger filter plates can accommodate more solids and increase the filtration capacity of the system. However, larger filter plates can also increase the size and cost of the filter press. The filter plate size should be chosen based on the desired filtration capacity and the available space for the filter press.
Material of construction
The material of construction of the filter press is a crucial consideration, as it can impact the filtration performance and the durability of the system. Common materials of construction for filter presses include stainless steel, polypropylene, and cast iron. The material should be chosen based on the compatibility with the process fluids, the desired corrosion resistance, and the overall longevity of the filter press.
Additional features
There are several additional features that can be added to a filter press to enhance its functionality and safety. Some of these features include:
-
Automatic plate shifters: Automatic plate shifters can speed up the filtration cycle by automatically moving the filter plates to discharge the filter cakes.
-
Cloth washing system: A cloth washing system can help to clean the filter cloth and improve its lifespan and filtration performance.
-
Drip trays: Drip trays can collect any excess filtrate that may drip from the filter press, preventing spills and maintaining a clean working environment.
-
Cake shields: Cake shields can prevent the filter cakes from sticking to the filter cloth, improving the cake release and reducing maintenance requirements.
-
Safety light curtains: Safety light curtains can provide an additional layer of protection by detecting any obstructions and automatically stopping the operation of the filter press.
In conclusion, customizing a filter press involves considering various factors such as design considerations, filtration capacity, number of chambers, filter plate size, material of construction, and additional features. By carefully considering these factors, a filter press can be tailored to meet the specific needs of the application, ensuring optimal filtration performance and efficiency.
If you are interested in this product you can browse our company website:https://kindle-tech.com/product-categories/heated-lab-press, we understand that every customer's needs are unique. Therefore, we offer a flexible customisation service to meet your specific requirements. Whether it is the specification, functionality or design of the equipment, we are able to personalise it to suit your needs. Our dedicated team will work closely with you to ensure that the customised solution will perfectly meet your experimental needs.
CONTACT US FOR A FREE CONSULTATION
KINTEK LAB SOLUTION's products and services have been recognized by customers around the world. Our staff will be happy to assist with any inquiry you might have. Contact us for a free consultation and talk to a product specialist to find the most suitable solution for your application needs!