Introduction
Table of Contents
Welcome to our comprehensive overview of the Benchtop KBr Pellet Press! In this blog post, we will explore the features, benefits, and applications of this compact and cost-effective tool. If you're looking for a way to compress powdered materials into uniform pellets without contamination, then the KBr Pellet Press might just be the perfect solution for you. Whether you're working in a pharmaceutical, biological, nutrition, or spectrographic lab, this hand-operated press offers convenience and efficiency in a small package. So let's dive in and discover how this tool can enhance your laboratory operations!
Benchtop KBr Pellet Press: Compact and Cost-Effective
Ideal for compressing powdered materials into pellet form
KINTEK offers a range of benchtop KBr pellet presses that are designed to meet the needs of industry and research laboratories. These presses are ideal for compressing powdered materials into pellet form, providing a convenient and cost-effective solution without the need for expensive tablet making machinery.

The KBr pellet press is compact and hand-operated, requiring minimal bench space and no fixed mounting. This makes it a versatile option that can be used anywhere in the laboratory. Despite its small size, the press is capable of producing uniform pellets in a polished die, without any risk of contamination.
Compact and hand-operated, requiring minimal bench space and no fixed mounting
The benchtop KBr pellet press from KINTEK is specifically designed for laboratories with space restrictions. Its compact size allows it to fit easily on a benchtop, without taking up valuable space. Additionally, being hand-operated, it does not require any fixed mounting, making it easy to use and move around as needed.
Despite its small size, the benchtop pellet press offers the same level of customization options and high quality as larger alternatives. It is available in both automatic and manual models, allowing for greater flexibility and customization to suit the specific requirements of the task at hand.
Produces uniform pellets without contamination
One of the key advantages of the benchtop KBr pellet press is its ability to produce uniform pellets without any risk of contamination. The press utilizes a polished die to ensure consistent pellet shape and size, resulting in reliable and accurate analysis.
The pellets produced by the KBr pellet press are cylindrical in shape with flat ends. The height or thickness of the pellets can be adjusted based on the amount of material compressed and the force applied during the pressing process. The dies are not fastened down, allowing for easy reloading and quick turnaround times.
The KBr pellet press is particularly well-suited for laboratories engaged in pharmaceutical, biological, nutrition, and spectrographic operations. It is an excellent device for preparing small samples to be analyzed in an emission spectrometer.
In conclusion, the benchtop KBr pellet press from KINTEK provides a compact and cost-effective solution for compressing powdered materials into pellet form. Its versatility, ease of use, and ability to produce uniform pellets without contamination make it an ideal choice for laboratories with limited space and budget constraints.
Pellet Characteristics
Cylindrical shape with flat ends
Pellets produced in a Pellet Press have a cylindrical shape with flat ends. This shape is favored for several reasons. Firstly, the cylindrical shape means there are only two edges to perform as stress concentrators, reducing the chance of fracture. Secondly, the pellet can be easily cut to suit various tests that will be applied to it, such as X-ray fluorescence (XRF) and infrared (IR) spectroscopy.

Height or thickness depends on the amount of material compressed and the force applied
The height or thickness of the pellets depends on two factors: the amount of material compressed and the force applied. The Pellet Press applies a fixed load or force to the material between the platens. The pressure experienced by the material depends on the area over which the force is applied. The anvil in the Pellet Press can be raised or lowered to adjust the thickness of the pellets. This flexibility allows for the production of pellets of any desired thickness using the maximum force of the press.
Quick reloading with non-fastened, auto-aligning dies
The dies used in the Pellet Press are not fastened down. They automatically align with the press ram and can be easily slipped out from under the ram for quick reloading. This feature ensures a smooth and efficient pellet production process, without the need for time-consuming die fastening.
Overall, the cylindrical shape, adjustable height, and quick reloading capability of the Pellet Press make it a convenient and efficient tool for compressing powdered materials into uniform pellets. These characteristics contribute to the quality and usability of the pellets in various applications, including spectroscopy, analysis, and testing.
Compressive Force Mechanism
A hydraulic press is a powerful tool that utilizes Pascal's Law to generate a large mechanical force from a modest initial effort. This force is achieved through a compressive force mechanism that involves hand pressure on a lever attached to a large steel cam. Let's explore how this mechanism works and its applications in more detail.
How Does a Hydraulic Press Use Pascal's Law?
In a hydraulic press, a small mechanical force (F1) is applied to a small area (A1). As the fluid is moved in one location, it inevitably moves elsewhere within that channel. This movement of fluid generates hydraulic pressure, which is then transmitted to a larger area (A2), resulting in a magnified mechanical force (F2). This principle is known as Pascal's Law and forms the basis of hydraulic press operation.

What Is a Hydraulic Press Used For?
A hydraulic press finds various applications, particularly in laboratory settings. One common use is in sample preparation for analysis. By compressing particles into pellets or thin films, a hydraulic press creates homogenous samples suitable for spectroscopic examination. This process involves forcing particles together, ensuring a firm and uniform pellet structure.
The Compressive Force Mechanism
The KINTEK Manual Hydraulic Press is an example of a hydraulic press that utilizes the compressive force mechanism. The user applies pressure by hand, using a lever to pump pressure into the hydraulic fluid system. This pressure is then transferred to a secondary area, resulting in a powerful force of up to 25 tons.
The hydraulic press consists of a mainframe, control systems, and power systems. Hydraulic fluid is forced into a small cylindrical piston (plunger cylinder), which drives the fluid into a larger piston (ram cylinder). The movement of the larger piston generates varying degrees of mechanical pressure, which is transmitted to an anvil that directly presses on the workpiece to be shaped.
The hydraulic pistons, or pumps, can be operated manually, pneumatically, or electrically, depending on the specific application. They generate a fixed amount of pressure, typically measured in tons. For low-force applications, a basic manual pump can suffice, while electric and pneumatic pumps provide larger and more consistently applied forces.
The compressive force in this press is developed by hand pressure on a lever attached to a large steel cam. This press system is designed to provide a steadily increasing mechanical advantage up to a ratio of approximately 50 to 1 at the end of the stroke. Thus, a force of 20 pounds applied to the lever develops approximately 1000 pounds on the press ram, which is sufficient to produce firm pellets from most powdered materials, typically without the need for adding a binder.
Considerations and Applications
When using pellet dies for pressing powders, there is a trade-off between the size of the required pellet and the compaction pressure that can be achieved. Pellet dies have a maximum rated load that limits the pressure to under 1000 MPa. However, even with as little as 0.5 tonnes of load in a 5 mm die, a pressure of 250 MPa can be achieved. In contrast, a 40 mm die would require over 30 tonnes of load to achieve the same pressure.
The Kin-Tech benchtop Pellet Press is a compact and hand-operated press that offers a convenient and economical means of compressing powdered materials into pellet or tablet form. It requires minimal bench space and no fixed mounting, making it ideal for laboratory use. The press produces uniform pellets in a polished die and ejects them smoothly into a receiver, minimizing the risk of contamination.
Additionally, other compression technologies such as hot pressing, cold isostatic pressing, hot isostatic pressing, and hot extrusion can generate products that are almost fully dense. However, these methods may lead to nanograin coarsening and recrystallization in some cases. As an alternative, shock compression, which utilizes short heating times and high-pressure shock waves, has been developed and achieved success in compressing nanopowders.
In conclusion, the compressive force mechanism in a hydraulic press allows for the generation of powerful forces through the application of hand pressure on a lever. This mechanism finds applications in sample preparation and compaction of powdered materials, offering a versatile and efficient solution for various industries and laboratory settings.
Variable Anvil Setting
The anvil in the Pellet Press is attached to a heavy screw post, allowing for height adjustment. This feature enables the production of pellets of any desired thickness using the maximum force of the press. By rotating the anvil to raise or lower the die, you can control the thickness of the pellets. This is particularly useful when compressing light or fluffy materials, as you can raise the die after each ram stroke to compensate for the reduction in volume.
Not only does the variable anvil setting allow for thickness adjustment, but it can also be used to adjust the amount of pressure applied to a pellet. By keeping the anvil at a fixed setting and taking the ram through its full stroke, you can ensure that duplicate pellets of equal density are produced. This is achieved by using equal amounts of sample for each pellet.
The Pellet Press, provided by KinTek, is a compact and hand-operated press that allows you to compress powdered materials into pellet or tablet form. It is a convenient and economical alternative to expensive tablet making machinery. The press produces uniform pellets in a polished die and ejects them smoothly into a receiver, minimizing the risk of contamination.
The pellets produced by the Pellet Press are cylindrical in shape with flat ends. The height or thickness of the pellets depends on the amount of material compressed and the force applied. The dies are not fastened down, making reloading quick and easy.
To enhance ease of use, die sets in the 13mm to 40mm range have been redesigned to incorporate an outer shield of aluminum. This reduces the weight of the dies while maintaining their strength and durability. Additionally, the dies can be evacuated with a vacuum pump to reduce moisture in the sample.
For abrasive samples, die sets in the 13mm to 40mm size range are available with optional tungsten carbide polished anvils. These anvils are extremely hard and ensure the preparation of high-quality pellets and briquettes.
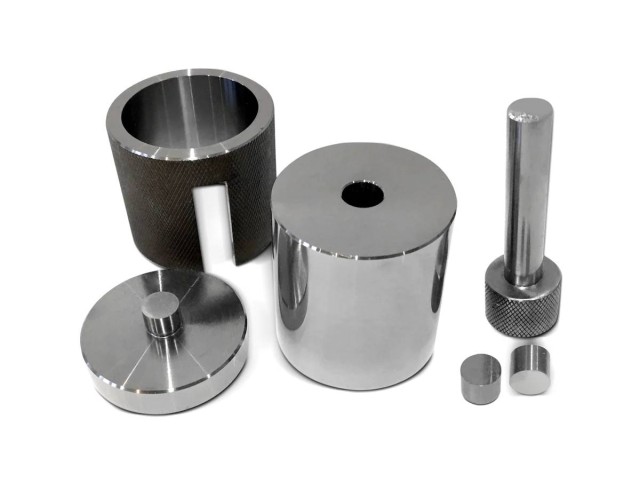
In conclusion, the variable anvil setting in the Pellet Press provides flexibility and control in the production of pellets. It allows for the adjustment of pellet thickness and pressure, ensuring the production of pellets with desired characteristics. Additionally, the Pellet Press itself is a convenient and economical tool for compressing powdered materials into pellet or tablet form.
Applications of the KBr Pellet Press
The KBr Pellet Press is a versatile device that finds its applications in various laboratory operations. It is particularly beneficial for labs engaged in pharmaceutical, biological, nutrition, and spectrographic operations. Additionally, it is highly suitable for preparing small samples for analysis in an emission spectrometer.
Spectroscopic Analysis
One of the primary applications of the KBr Pellet Press is in spectroscopic analysis. Spectroscopists rely on this device to fabricate pellets from a matrix of KBr and an organic sample. These pellets are then used for infrared spectroscopy, allowing researchers to study the molecular composition and structure of the sample.

X-ray Fluorescence Spectroscopy
Inorganic samples can also be processed using the KBr Pellet Press for x-ray fluorescence (XRF) spectroscopy. The press is capable of briquetting these samples, enabling accurate analysis of their elemental composition.
Thin Film Preparation
The KBr Pellet Press is also useful for pressing thin polymer films using heated platens. This method is commonly employed for transmission sampling by IR spectroscopy. The press ensures uniform compression of the film, resulting in consistent and reliable data.
Other Applications
Apart from the aforementioned applications, the KBr Pellet Press has various other uses. It can be utilized for pill making, where powdered materials are compressed into solid pills. Additionally, it is suitable for laminating processes, ensuring the efficient production of laminated materials.
The KBr Pellet Press is a compact and hand-operated device that provides an economical solution for compressing powdered materials. It eliminates the need for expensive laboratory presses and pellet dies, making it a cost-effective choice for labs of all sizes. Furthermore, its small size and portability allow for flexible usage within the laboratory without the need for fixed mounting.
The pellets produced by the KBr Pellet Press are cylindrical in shape with flat ends. The height or thickness of the pellets can be adjusted based on the amount of material compressed and the force applied. The press features polished dies that produce uniform pellets and smoothly eject them into a receiver, minimizing the risk of contamination.
With its wide range of applications and user-friendly design, the KBr Pellet Press is an invaluable tool for laboratories involved in various scientific disciplines. Its versatility and efficiency make it an essential asset for researchers seeking accurate and reliable sample preparation for spectroscopic analysis.
Conclusion
In conclusion, the Benchtop KBr Pellet Press is a compact and cost-effective solution for compressing powdered materials into pellet form. Its hand-operated design requires minimal bench space and no fixed mounting, making it convenient for use in various laboratory settings. The press produces uniform pellets without contamination, ensuring accurate and reliable results. With its variable anvil setting, it allows for the production of pellets of any desired thickness and the adjustment of pressure applied. The KBr Pellet Press is widely used in pharmaceutical, biological, nutrition, and spectrographic labs, making it an essential tool for sample preparation in these fields.
CONTACT US FOR A FREE CONSULTATION
KINTEK LAB SOLUTION's products and services have been recognized by customers around the world. Our staff will be happy to assist with any inquiry you might have. Contact us for a free consultation and talk to a product specialist to find the most suitable solution for your application needs!