Brazing and soldering are indeed possible for dissimilar materials, but they come with unique challenges due to the differences in thermal expansion, melting points, and chemical compatibility between the materials. These processes are performed in controlled environments to ensure proper bonding. Brazing typically involves higher temperatures and stronger filler materials, making it suitable for joining metals with significant differences in properties. Soldering, on the other hand, uses lower temperatures and is often used for electronics or delicate applications. Both methods require careful selection of filler materials and surface preparation to ensure a strong and durable joint.
Key Points Explained:
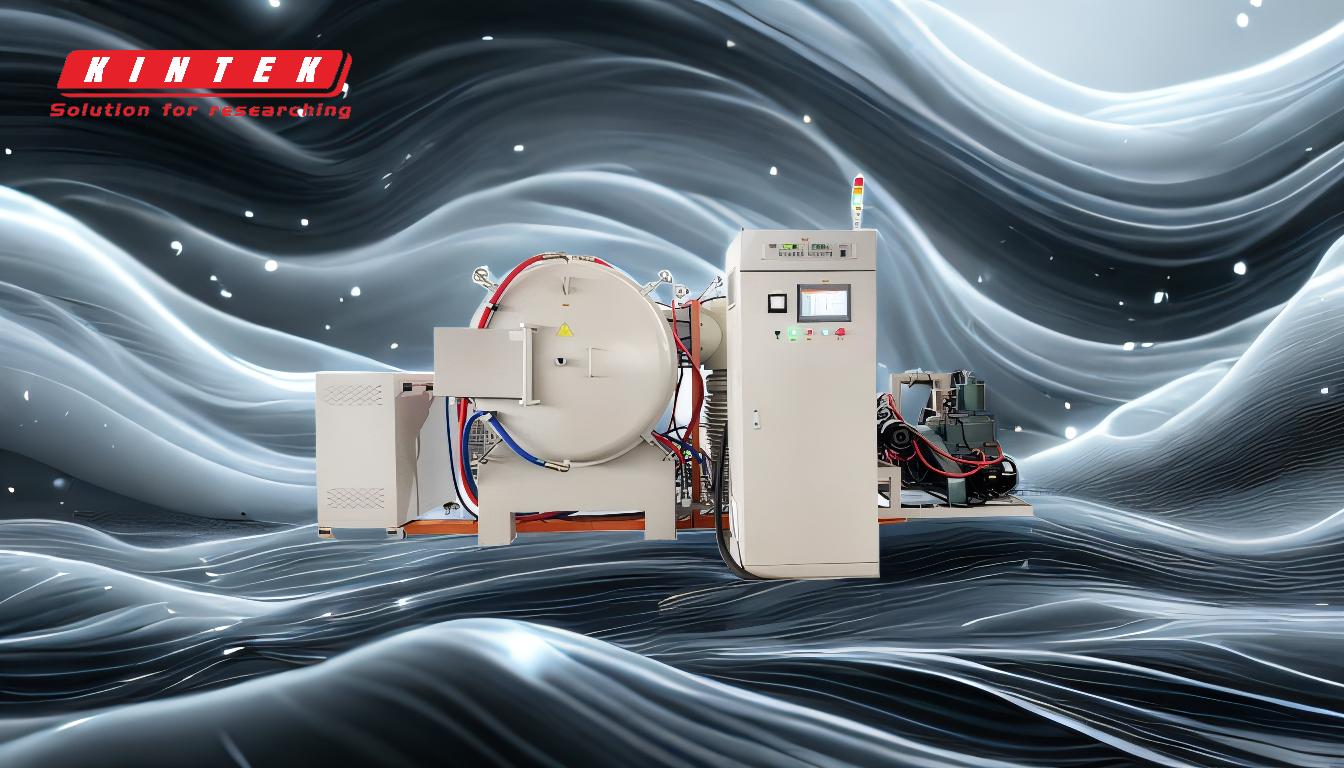
-
Definition and Applicability of Brazing and Soldering:
- Brazing and soldering are joining techniques used to bond dissimilar materials without melting the base materials.
- Brazing uses filler materials with melting points above 450°C, while soldering uses fillers with melting points below 450°C.
- These methods are particularly useful when welding is not feasible due to material incompatibilities or thermal sensitivity.
-
Challenges in Joining Dissimilar Materials:
- Thermal Expansion Differences: Dissimilar materials often have different coefficients of thermal expansion, which can lead to stress and cracking during cooling.
- Melting Point Variations: Materials with vastly different melting points require precise temperature control to avoid damaging the lower-melting-point material.
- Chemical Compatibility: Some materials may react unfavorably with the filler material, leading to weak joints or corrosion.
-
Process Considerations:
- Surface Preparation: Proper cleaning and surface preparation are critical to ensure good wetting and adhesion of the filler material.
- Filler Material Selection: The filler must be compatible with both base materials and provide the necessary strength and corrosion resistance.
- Temperature Control: Precise temperature management is essential to prevent overheating or insufficient bonding.
-
Applications of Brazing and Soldering for Dissimilar Materials:
- Brazing: Commonly used in aerospace, automotive, and HVAC industries to join metals like steel, copper, and aluminum.
- Soldering: Widely used in electronics to join components made of different metals, such as copper and gold.
-
Advantages of Brazing and Soldering:
- Versatility: Can join a wide range of materials, including metals, ceramics, and composites.
- Minimal Distortion: Lower heat input compared to welding reduces the risk of warping or distortion.
- Cost-Effectiveness: Often more economical than welding for certain applications.
-
Limitations:
- Joint Strength: Brazed and soldered joints may not be as strong as welded joints, depending on the materials and filler used.
- Temperature Sensitivity: Some materials may degrade or oxidize at the temperatures required for brazing or soldering.
By carefully addressing these challenges and considerations, brazing and soldering can be effectively used to join dissimilar materials, providing a reliable and cost-effective solution for many industrial applications.
Summary Table:
Aspect | Details |
---|---|
Definition | Brazing and soldering join dissimilar materials without melting base materials. |
Temperature Range | Brazing: >450°C; Soldering: <450°C. |
Challenges | Thermal expansion differences, melting point variations, chemical compatibility. |
Process Considerations | Surface preparation, filler material selection, precise temperature control. |
Applications | Brazing: Aerospace, automotive, HVAC. Soldering: Electronics. |
Advantages | Versatility, minimal distortion, cost-effectiveness. |
Limitations | Joint strength, temperature sensitivity. |
Need help with brazing or soldering dissimilar materials? Contact our experts today for tailored solutions!