Brazing is a metal-joining process that involves heating a filler metal above its melting point and distributing it between two or more close-fitting parts by capillary action. The filler metal used in brazing has a lower melting point than the base metals being joined. Typically, brazing is performed at temperatures above 450°C (842°F) but below the melting point of the base metals. The exact temperature depends on the materials being joined and the filler metal used. Brazing is widely used in industries such as automotive, aerospace, and HVAC due to its ability to create strong, leak-proof joints without melting the base materials.
Key Points Explained:
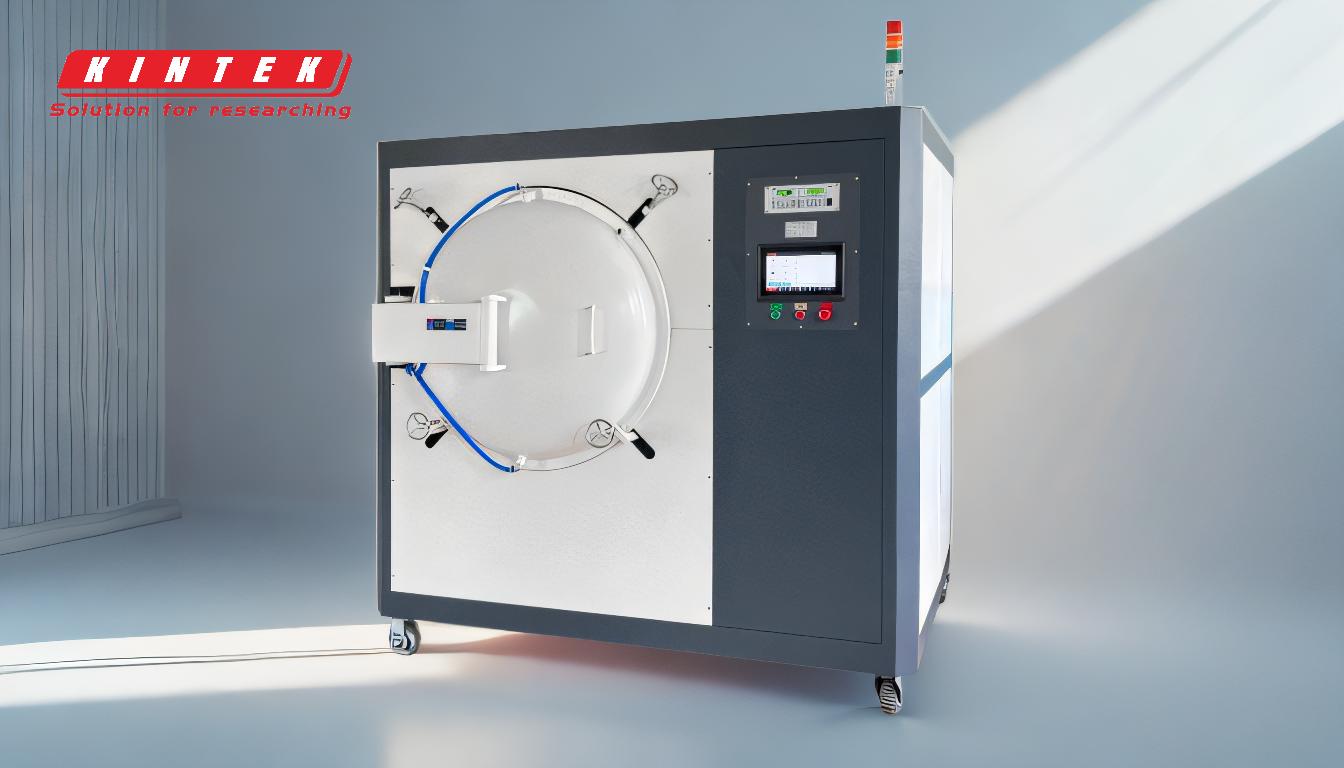
-
Definition of Brazing:
- Brazing is a metal-joining process where a filler metal is heated above its melting point and drawn into the joint by capillary action. Unlike welding, the base metals do not melt during brazing. This process is ideal for joining dissimilar metals and creating strong, durable joints.
-
Temperature Range for Brazing:
- Brazing typically occurs at temperatures above 450°C (842°F) but below the melting point of the base metals. The exact temperature depends on the filler metal and the materials being joined. For example:
- Silver brazing alloys often require temperatures between 600°C (1112°F) and 900°C (1652°F).
- Aluminum brazing is usually performed at lower temperatures, around 580°C (1076°F) to 620°C (1148°F).
- Brazing typically occurs at temperatures above 450°C (842°F) but below the melting point of the base metals. The exact temperature depends on the filler metal and the materials being joined. For example:
-
Factors Influencing Brazing Temperature:
- Filler Metal Composition: Different filler metals have varying melting points. For instance, copper-phosphorus alloys melt at lower temperatures than nickel-based alloys.
- Base Metal Properties: The thermal conductivity and melting point of the base metals influence the required brazing temperature.
- Joint Design: The gap between the parts being joined affects capillary action and heat distribution, which in turn impacts the brazing temperature.
-
Advantages of Brazing:
- Strong Joints: Brazed joints are often stronger than the filler metal itself due to the metallurgical bond formed.
- Versatility: Brazing can join dissimilar metals and materials with different thermal expansion rates.
- Leak-Proof Seals: The capillary action ensures a tight, leak-proof joint, making it ideal for applications like refrigeration and plumbing.
-
Applications of Brazing:
- Automotive Industry: Used for joining components like radiators, air conditioning systems, and fuel lines.
- Aerospace: Critical for assembling lightweight, high-strength structures.
- HVAC Systems: Ensures durable and leak-free connections in heating, ventilation, and air conditioning systems.
-
Comparison with Soldering and Welding:
- Soldering: Occurs at lower temperatures (below 450°C) and is typically used for electrical connections or low-stress applications.
- Welding: Involves melting the base metals to form a joint, which requires much higher temperatures and can distort the materials.
By understanding the temperature range and factors influencing brazing, manufacturers and engineers can select the appropriate materials and techniques to achieve high-quality, durable joints for various applications.
Summary Table:
Aspect | Details |
---|---|
Temperature Range | Above 450°C (842°F) but below the melting point of base metals. |
Example Temperatures | Silver brazing: 600°C–900°C; Aluminum brazing: 580°C–620°C. |
Key Factors | Filler metal composition, base metal properties, joint design. |
Advantages | Strong joints, versatility, leak-proof seals. |
Applications | Automotive, aerospace, HVAC systems. |
Discover how brazing can enhance your manufacturing process—contact our experts today!