Brazing is a versatile joining process that can indeed join incompatible metals, provided the right conditions and materials are used. The process involves melting a filler metal (with a lower melting point than the base metals) and using it to join the base metals without melting them. This allows for the joining of dissimilar metals, such as stainless steel, nickel, copper, and silver, which might otherwise be difficult or impossible to weld. The use of a controlled atmosphere, such as in a brazing oven, ensures that the metals are protected from oxidation and other contaminants, leading to strong and durable joints.
Key Points Explained:
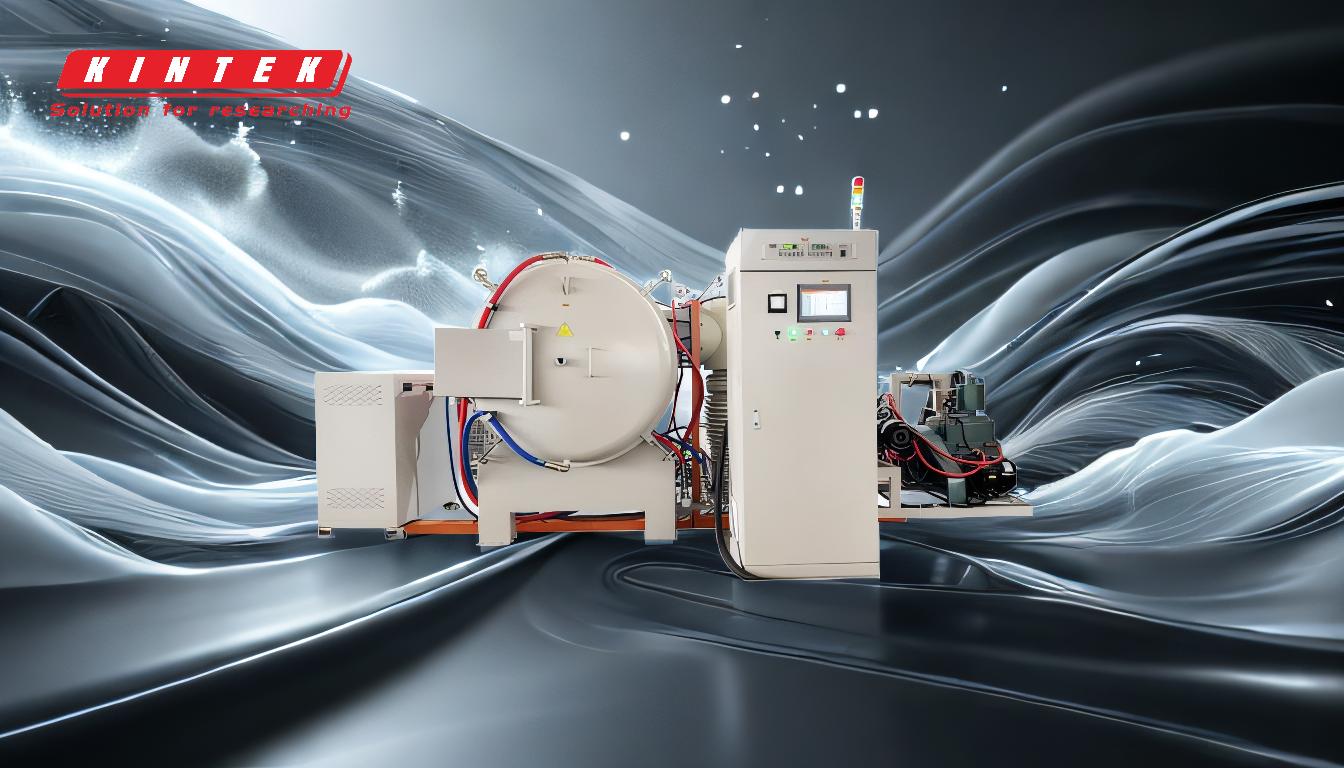
-
Brazing Process Overview:
- Brazing involves heating the base metals and the filler metal to a temperature above the filler's melting point but below the melting point of the base metals.
- The molten filler metal flows into the joint by capillary action, creating a strong bond as it cools and solidifies.
-
Joining Incompatible Metals:
- Brazing is particularly useful for joining metals that are difficult to weld due to differences in melting points, thermal expansion rates, or metallurgical incompatibility.
- For example, stainless steel and copper can be joined effectively using a suitable filler metal, such as a silver-based alloy.
-
Filler Metals:
- The choice of filler metal is crucial in brazing. It must have a lower melting point than the base metals and be compatible with both materials.
- Common filler metals include silver, copper, nickel, and their alloys, each selected based on the specific properties required for the joint.
-
Controlled Atmosphere:
- A controlled atmosphere, such as that provided by a brazing oven, is essential for preventing oxidation and contamination during the brazing process.
- This environment ensures that the filler metal flows smoothly and forms a strong, clean bond with the base metals.
-
Applications:
- Brazing is widely used in industries such as aerospace, automotive, and electronics, where the joining of dissimilar metals is often required.
- It is also used in the production of complex assemblies where traditional welding methods might be impractical.
-
Advantages of Brazing:
- Brazing allows for the joining of dissimilar metals with minimal distortion or damage to the base materials.
- The process can produce strong, leak-proof joints that are resistant to corrosion and thermal stress.
-
Considerations:
- Proper joint design and preparation are critical to the success of the brazing process.
- The thermal expansion rates of the base metals must be considered to prevent stress and cracking in the joint.
In summary, brazing is a highly effective method for joining incompatible metals, offering a range of advantages over other joining techniques. By carefully selecting the appropriate filler metal and using a controlled atmosphere, strong and durable joints can be achieved between a wide variety of metals.
Summary Table:
Key Aspect | Details |
---|---|
Process Overview | Melts filler metal to join base metals without melting them. |
Incompatible Metals | Joins metals like stainless steel, copper, and nickel with ease. |
Filler Metals | Silver, copper, nickel, and alloys chosen for compatibility and performance. |
Controlled Atmosphere | Prevents oxidation, ensuring clean and strong bonds. |
Applications | Aerospace, automotive, electronics, and complex assemblies. |
Advantages | Minimal distortion, leak-proof, corrosion-resistant joints. |
Considerations | Proper joint design and thermal expansion rates are critical. |
Learn how brazing can solve your metal joining challenges—contact our experts today!