Yes, metal can be remelted. Remelting is a common process in metallurgy and manufacturing, where metals are heated to their melting point to be reshaped, recycled, or purified. This process is widely used in industries such as automotive, construction, and electronics, where metal recycling and reuse are essential for sustainability and cost-efficiency. The ability to remelt metals depends on their properties, such as melting point, purity, and alloy composition. While most metals can be remelted multiple times without significant degradation, some may lose certain properties or require additional treatments to restore their original quality.
Key Points Explained:
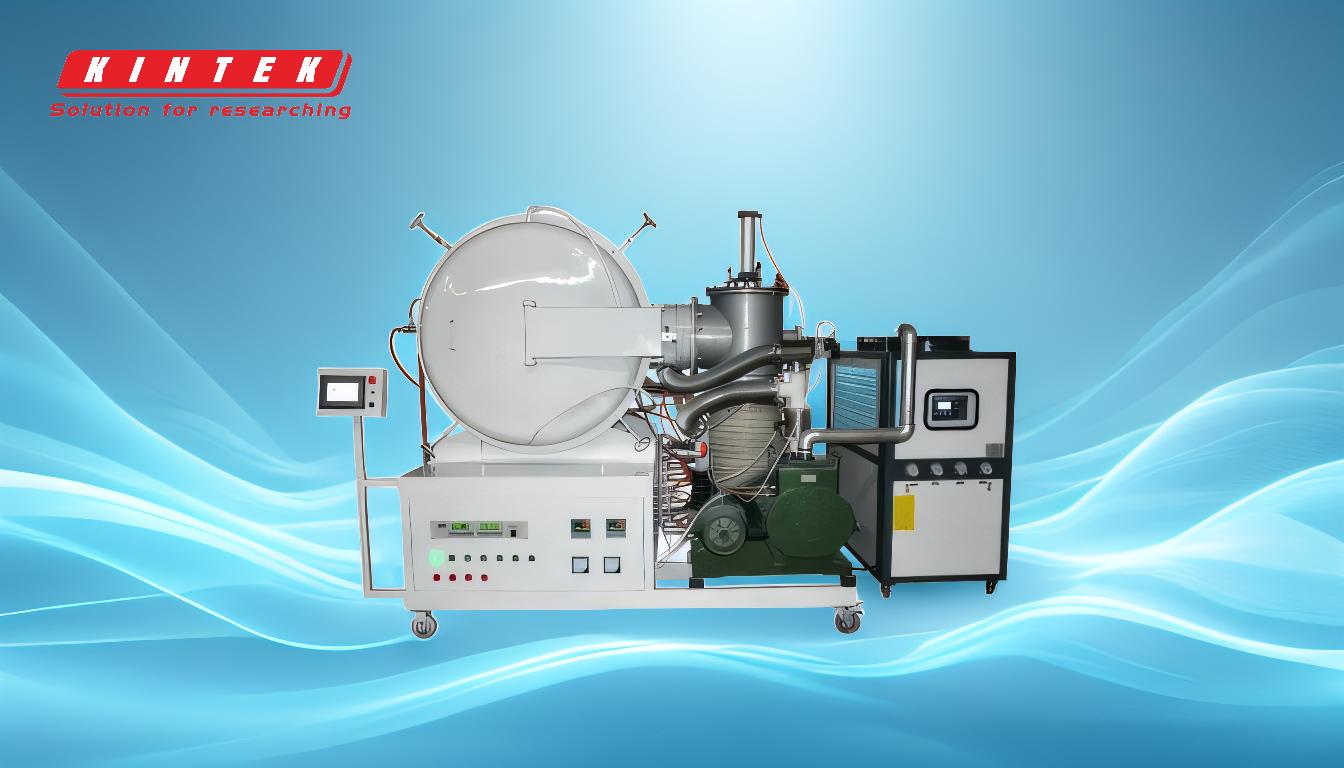
-
The Science of Remelting Metals
- Metals are crystalline structures that can transition from solid to liquid when heated to their melting point.
- The melting point varies depending on the type of metal (e.g., aluminum melts at 660°C, while iron melts at 1538°C).
- Remelting allows metals to be reshaped into new forms, such as ingots, sheets, or complex components.
-
Applications of Metal Remelting
- Recycling: Scrap metal is often remelted to produce new products, reducing waste and conserving natural resources.
- Manufacturing: Remelting is used to create alloys, cast parts, or refine metals for specific applications.
- Purification: Impurities can be removed during the remelting process, improving the metal's quality.
-
Factors Affecting Remelting
- Purity: Contaminants or impurities can affect the remelting process and the final product's quality.
- Alloy Composition: Alloys may require precise temperature control to maintain their properties during remelting.
- Oxidation: Exposure to air during remelting can lead to oxidation, which may require protective atmospheres or fluxes.
-
Challenges and Limitations
- Some metals, like magnesium, are highly reactive and require special handling during remelting.
- Repeated remelting can degrade certain properties, such as strength or ductility, especially in alloys.
- Energy consumption and environmental impact are considerations, as remelting requires significant heat input.
-
Equipment and Techniques for Remelting
- Furnaces: Induction furnaces, arc furnaces, and crucible furnaces are commonly used for remelting.
- Protective Atmospheres: Inert gases like argon or nitrogen are used to prevent oxidation.
- Fluxes: Chemical agents are added to remove impurities and improve metal quality.
-
Economic and Environmental Benefits
- Remelting reduces the need for mining and refining raw materials, lowering costs and environmental impact.
- It supports circular economy practices by enabling the reuse of metal scrap.
-
Examples of Remelted Metals
- Aluminum: Widely recycled in industries like packaging and automotive manufacturing.
- Steel: Scrap steel is remelted to produce new steel products, such as beams or car parts.
- Copper: Used in electrical wiring and plumbing, copper is frequently remelted for reuse.
By understanding these key points, purchasers of equipment and consumables can make informed decisions about the types of metals and processes suitable for their specific needs. Remelting is a versatile and sustainable practice that plays a critical role in modern manufacturing and resource management.
Summary Table:
Aspect | Details |
---|---|
Science of Remelting | Metals transition from solid to liquid at their melting point. |
Applications | Recycling, manufacturing, and purification of metals. |
Key Factors | Purity, alloy composition, and oxidation control. |
Challenges | Reactivity, property degradation, and energy consumption. |
Equipment | Induction furnaces, arc furnaces, and protective atmospheres. |
Benefits | Cost savings, reduced environmental impact, and circular economy support. |
Examples | Aluminum, steel, and copper are commonly remelted metals. |
Discover how metal remelting can transform your operations—contact our experts today to learn more!